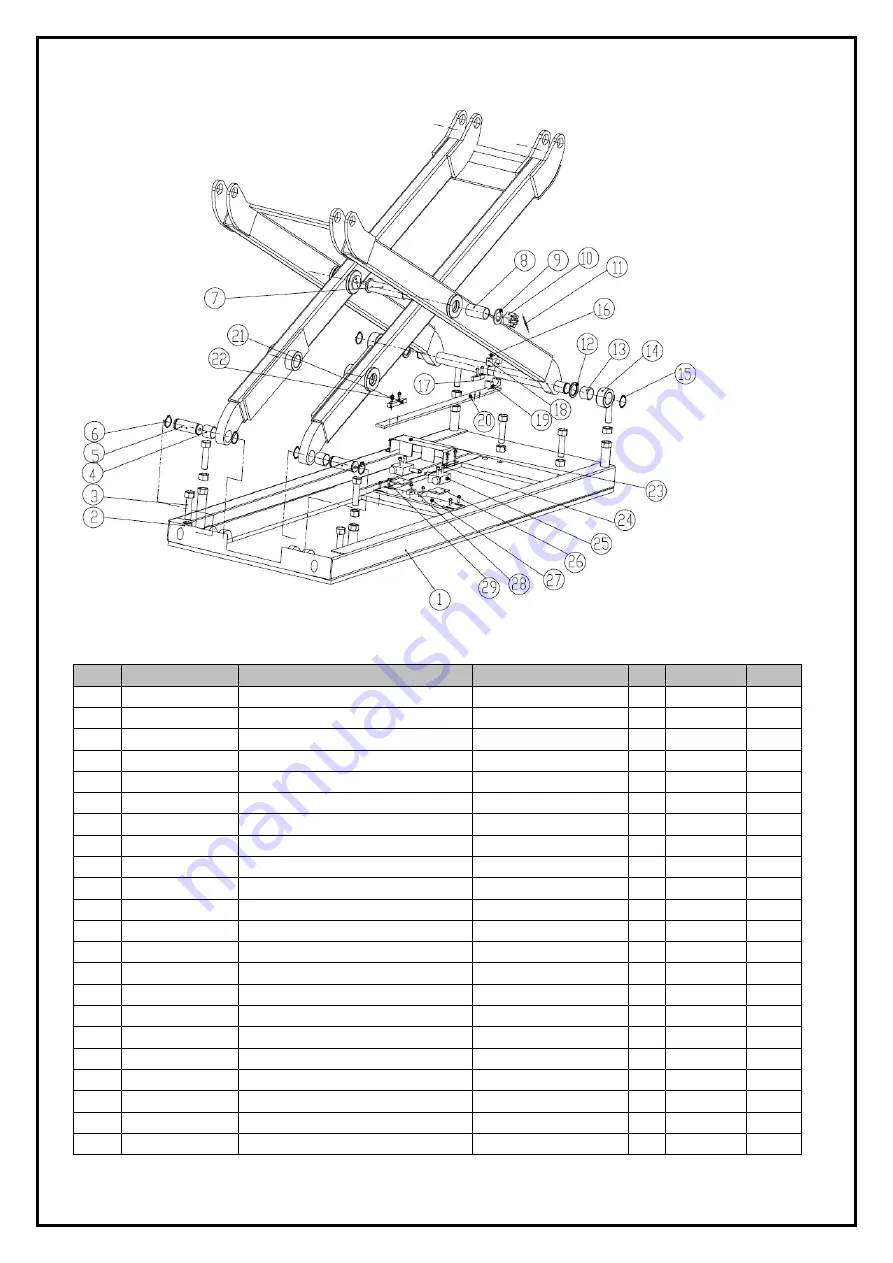
19
S/N
Material#
Name
Spec.
Qty Property
Note
1
Base assembly
FL-8802-A1-B1
1
Welded
2
Hex nut
M16
8
Standard
3
Bolt
M16X50
4
Standard
4
Bearing
3025
2
Standard
5
Shaft A
FL-8802-A2
2
45#
6
Circlip
Φ30
4
Standard
7
Shaft B
FL-8802-A5-B5
2
45#
8
Bearing
3055
2
Standard
9
Flat washer
Φ24
2
Q235A
10
Slotted nut
M24
2
Standard
11
Cotter pin
Φ2.5
2
Standard
12
Washer
FL-8802-A5-B2-C5
2
Q235A
13
Bearing
3025
2
Standard
14
Roller
FL-8802-A5-B2-C4
2
Nylon
15
Circlip
Φ30
2
Standard
16
Inside hex cylinder screw
M4X45
2
Standard
17
Retaining block B for limit switch
FL-8802-A1-B7
1
Q235A
18
Up fixing block
FL-8802-A1-B8
1
Q235A
19
Down fixing block
FL-8802-A1-B9
1
Q235A
20
Draw bar
FL-8802-A1-B6
1
Q235A
21
Retaining block A for limit switch
FL-8802-A1-B3
1
Q235A
22
Cross cap screw
M4X14
2
Standard
Summary of Contents for AutoLift AL-3000BG
Page 13: ...13 OVERALL DIAGRAM ...
Page 14: ...14 SPACE REQUIRED ...
Page 16: ...16 HYDRAULIC CONNECTION ...
Page 18: ...18 WIRING DIAGRAM ...