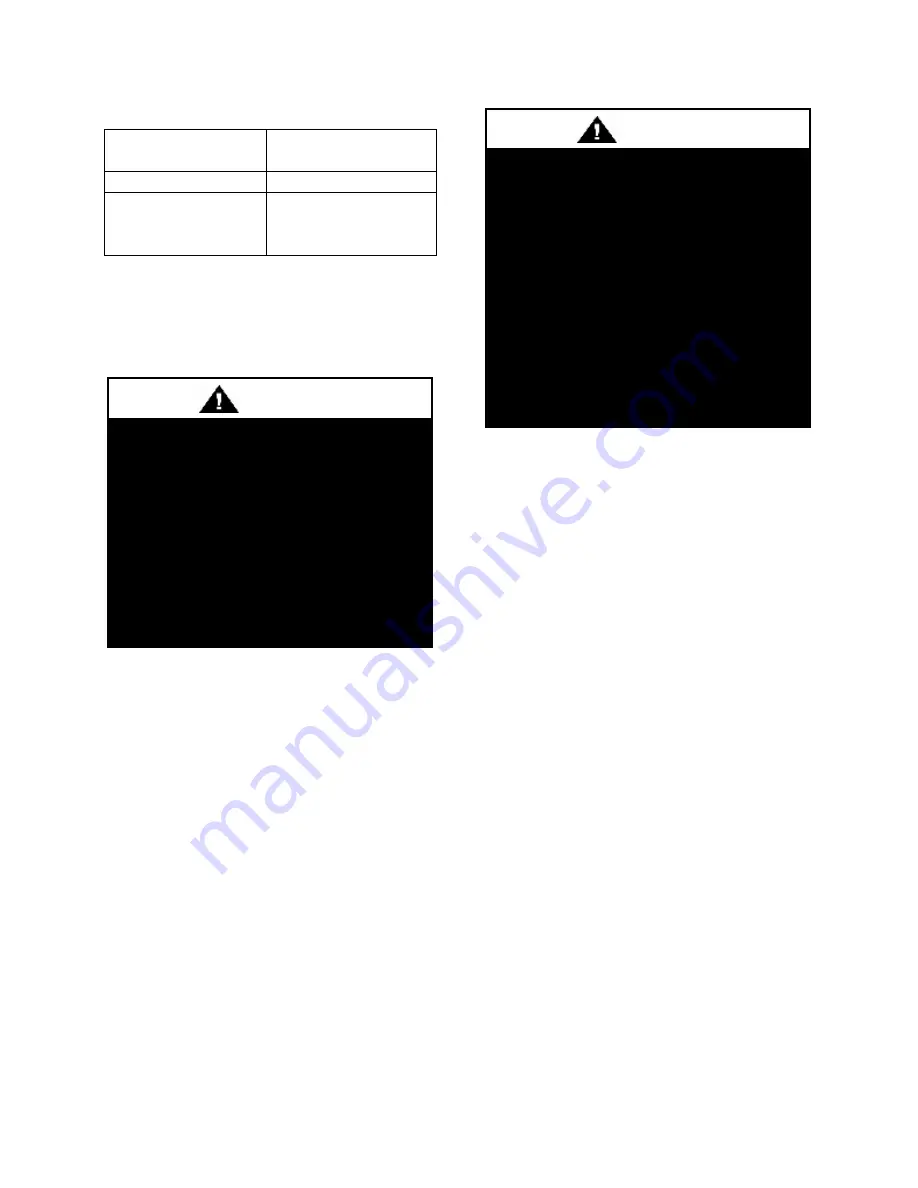
31
Table 3 - Condenser Water Connections
Model (SA-)
Supply and Return
Connection Size
023, 045
1 1/2” MPT
028, 030, 035, 050,
055, 058, 060, 065,
070
2” MPT
Only use approved water pipe material.
Avoid using galvanized material for water
lines/fittings as the material is corrosive and
may cause fouling of the water system.
Condenser water pump must be field sized
and installed between the cooling tower and
self contained unit. System should be sized
in accordance with the ASHRAE Handbook.
Use engineering guidelines to maintain
equal distances for supply and return piping
and limit bend radiuses to maintain balance
in the system. Balancing valves, permanent
thermometers and gauges may be required.
Before connection to the unit, the condenser
water system should be flushed to remove
foreign material that could cause condenser
fouling. A screen strainer with a minimum
of 20 Mesh is provided ahead of the
condenser inlet to prevent condenser fouling
and internal tube damage.
Mineral content of the condenser water must
be controlled. All make-up water has
minerals in it and as the water is evaporated
in the cooling tower, these minerals remain.
As the mineral content of the water
increases, the conductivity of the water
increases.
Field provided and installed water treatment
program must be compatible with stainless
steel, copper, aluminum, ABS plastic, and
PVC. Batch feed processes should never be
used as concentrated chemicals can cause
corrosion. Never use hydrochloric acid
(muriatic acid) or chlorine as it will corrode
stainless steel.
WATER PIPING
Follow national and local codes when
installing water piping. Connections
to
the
unit
should
incorporate
vibration eliminators to reduce noise
and vibration and shutoff valves to
facilitate servicing. Supply and return
water piping must be at least as large
as the unit connections and larger
depending on length of runs, rise and
bends.
CAUTION
PVC (Polyvinyl Chloride) and CPVC
(Chlorinated Polyvinyl Chloride) are
vulnerable to attack by certain
chemicals. Polyolester (POE) oils
used
with
R-410A
and
other
refrigerants, even in trace amounts,
in a PVC or CPVC piping system will
result in stress cracking of the piping
and fittings and complete piping
system failure.
CAUTION
Summary of Contents for SA-023
Page 2: ......
Page 20: ...20 Figure 2 One Piece Single Unit Lifting Details ...
Page 21: ...21 Figure 3 Two Piece Single Unit Coil Section Lifting Details ...
Page 22: ...22 Figure 4 Two Piece Single Unit Fan Section Lifting Details ...
Page 23: ...23 Figure 5 One Piece Dual Unit Lifting Details ...
Page 24: ...24 Figure 6 Two Piece Dual Unit Coil Section Lifting Details ...
Page 25: ...25 Figure 7 Two Piece Dual Unit Fan Section Lifting Details ...
Page 28: ...28 Figure 10 Dual unit with splices after being bolted together ...
Page 63: ...63 ...