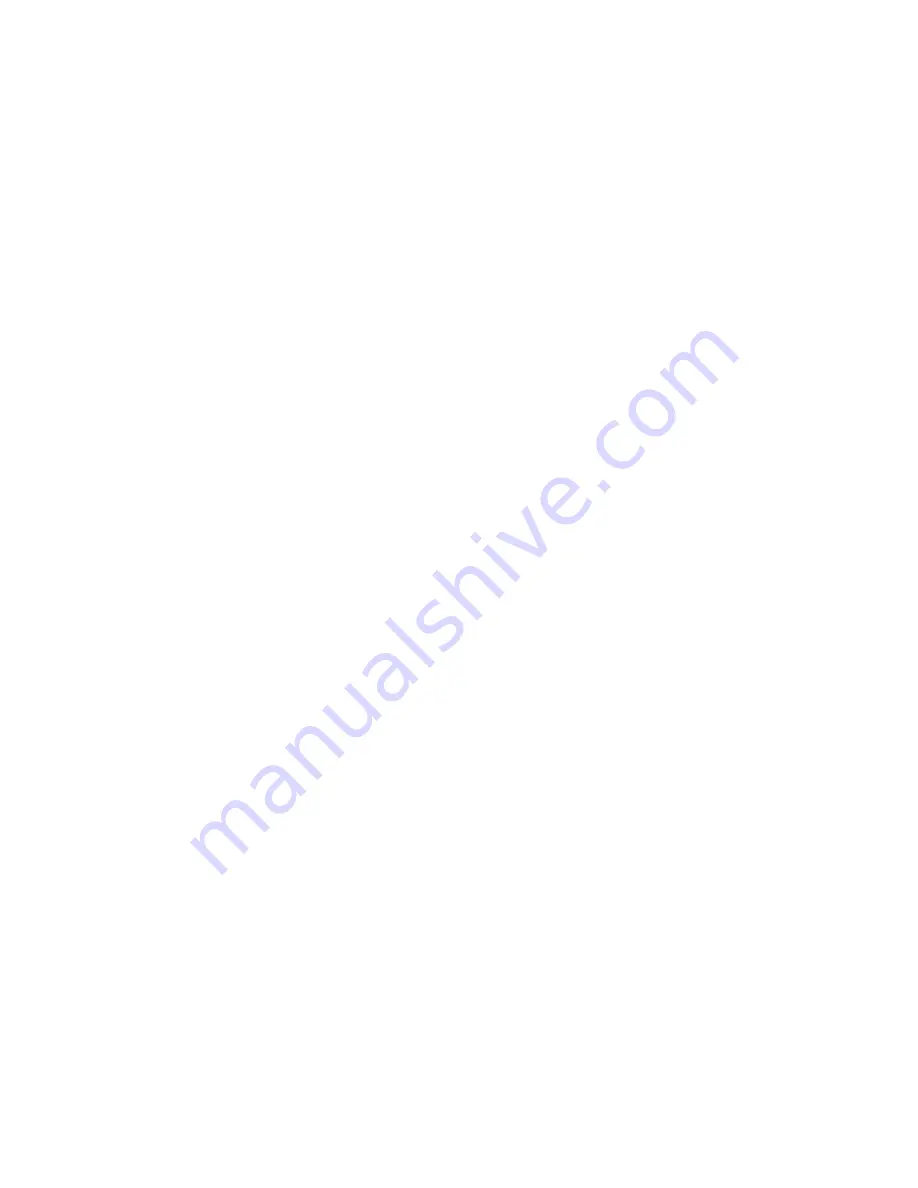
13
Drive Over Temperature Protection
The drive is self protected against high
internal temperatures. There are different
modes of protection; temperature high and
foldback. For foldback protection refer to
Table 8 for more information.
Power Interrupt
Power interrupts can result in a drive trip
that won't harm the drive. The drive can
withstand interrupts of a short duration (1-2
power cycles), but will trip on anything
longer.
Air Cooled Heat Exchanger
Drives cooled by the aluminum air cooled
heat exchanger are designed to be in the air
flow stream of the condenser.
Foldback
To protect the drive components or the
compressor, the compressor speed will
'foldback' or slow down to help reduce risk
to components. The foldback event(s) will
be flagged in the unit controller. This will
allow the operating system to respond and
mitigate the conditions causing foldback.
Troubleshooting
The drive may indicate fault or protection
for various reasons. If fault or protection
occurs, users should power down the drive,
check the drive, and check the drive running
condition carefully. For the description,
check and handling of these faults or
protections, please refer to
Troubleshooting
Table
.
The yellow and red LED of COMM will be
displayed in a circulation of blinking for N
times (N is the protection code) then be off
for 3 seconds. For detailed description of the
protections, please refer to
Troubleshooting
Table.
• Immediate shutdown = The drive will
execute an immediate shut down due to a
condition that may cause damage to the
drive.
• Controlled shutdown = The drive w
ill
execute a controlled shut down due to
systemic or temperature related problems.
• First faults latched = When a fault occurs it
may cause other faults to happen as well. In
order to capture the fault that happened first,
these registers only record the
‘first fault
latched’.
• Current faults = These registers display all
faults that are currently logged by the drive,
including the first faults latched.
Summary of Contents for RQ SERIES
Page 1: ...RQ SERIES Variable Speed Scroll Compressor Supplement...
Page 4: ...4...
Page 17: ...17 Figure 4 U S Drive Model Wiring Diagram Figure 5 U S Wiring Diagram...
Page 33: ......
Page 34: ......
Page 35: ......