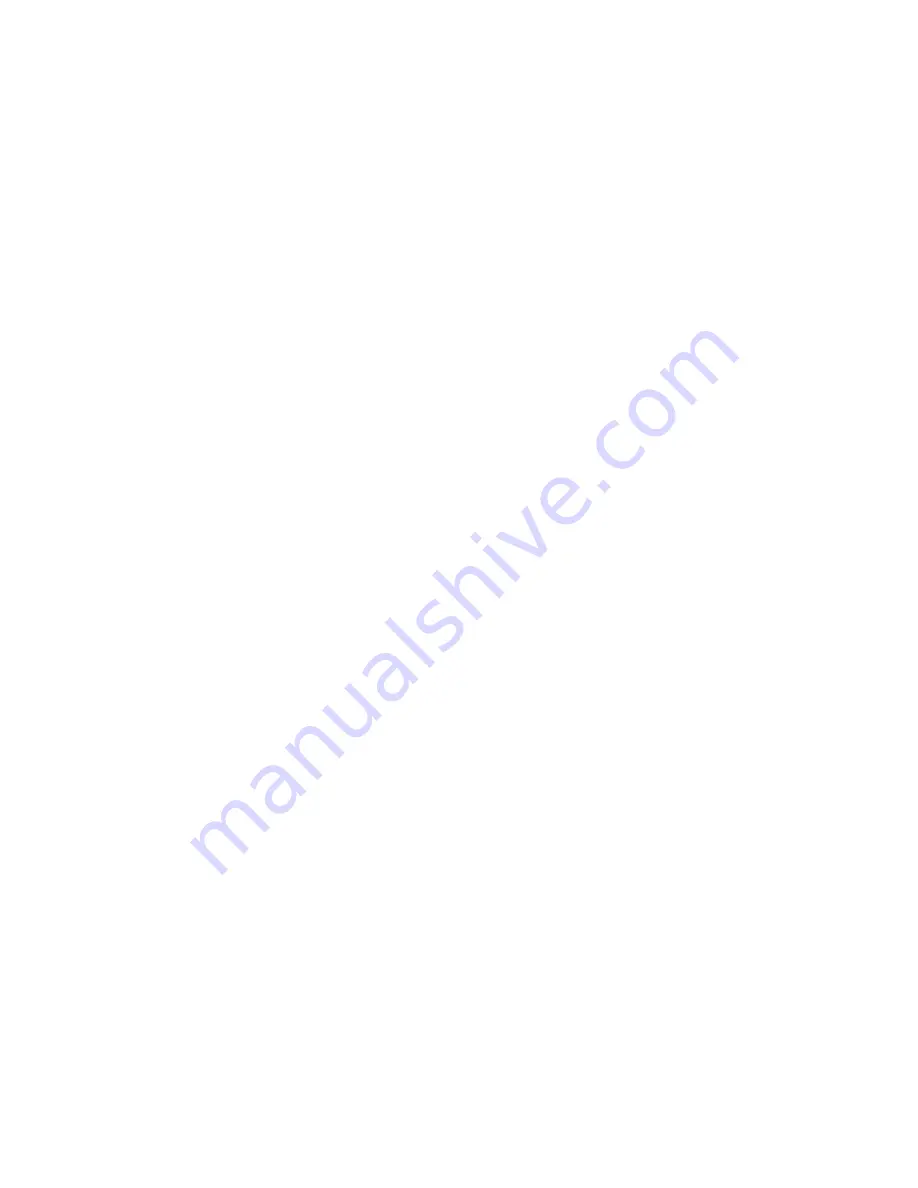
8
closed and everything else is in the proper state, a "call for
heat" condition will be initiated. These leads should be
shorted together, when a thermostat is not being used. If it is
desired that the thermostat control the temperature of the
boiler, the operating setpoint of the system should be set
higher than the temperature that the thermostat is controlling
to. This will allow the thermostat to control the boiler. When
the thermostat closes, a call for heat will be generated until
the thermostat determines that the control temperature has
been reached.
• Air Pressure Sensors (open condition indicates fault):
• Blocked Flue (CCB - required)
• Normally closed switch that opens if the flue becomes
blocked during operation.
• Powered Vent (CCB - optional):
Normally open switch that closes when the powered vent is
operating properly. This input is enabled-disabled by a
dipswitch on the CCB.
• Blower Prover High (FCB - required on stages that have
blowers):
Normally open switch that closes when the air pressures
produced by the high-speed blower is above the trip level.
• Gas Pressure Sensors (open condition indicates fault):
• Low Gas (CCB - optional):
Normally open switch that closes when the gas pressure
rises above the trip level. This input is enabled/disabled by a
dipswitch on the CCB.
• Hi Gas (FCB - optional):
Normally closed switch that opens in the gas pressure
exceeds a set value. This input is enabled/disabled by a
dipswitch on the CCB and FCB's.
• Water Level Sensor (open conditions indicates fault):
• Low Water Cut Off (CCB - optional):
Normally closed switch opens if a low water condition occurs.
This input is enabled/disabled by a dipswitch on the CCB.
• Water Flow Sensor:
• Flow (CCB - required):
Normally open switch that closes when flow exceeds a set
value.
• IRI Gas Valve Sensor:
• IRI Gas Valve (CCB - optional):
Normally open switch that closes when the IRI Gas Valve is
operating correctly. This input is enabled/disabled by a
dipswitch on the CCB.
• Flame Sensor:
• Flame (FCB - required on stage 1 and on stage 2 of a 4 stage
system - optional on others):
Returns a signal to the microprocessor if flame is detected
in the burner. This input is enabled/disabled by a dipswitch
on the FCB.
Outputs from CCB and FCB's :
• Relay Contact Outputs:
• IRI Gas Valve (CCB - 120vac- optional):
Provides electrical power to operate an IRI Gas Valve device.
• Alarm (CCB - 24vac- optional):
Provides electrical power to operate on external alarm. This
can be an audio device (i.e. Sonalert), a visual device (lamp),
or any other device that will operate with the voltage and
current level provided.
• Pump (CCB - 120vac - required on systems that do not have
an external pump):
Provides electrical power to directly operate a pump or the
coil of an externally connected contactor.
• Powered Vent (CCB - 24vac - optional):
Provides electrical power to operate a powered vent.
• Low and High Speed Blowers (FCB - 120vac - required on
stage 1 and on stage 2 of a 4-stage system and optional on
others.):
Independent outputs that provide power to operate low and
high speed blower output. Dip switches on the FCB's enable/
disable the use of blowers on stages 2, 3 and 4.
• Igniter (FCB - 120vac - required on stage 1 and on stage 2 of
a 4-stage system and optional on others.):
Provides power to operate the Silicon Carbide igniter. Dip
switches on the FCB's enables/disables the use of an igniter
on stages 2, 3 and 4.
• Gas Valve (FCB - 24vac - required):
Provides power to activate the gas valve. The gas valve cannot
be activated when the ECO contacts are open.
• Direct Connection Output:
• Low Water Cut Off (CCB - 24vac - optional):
Directly connected to the 24 vac line to provide power to operate
an external LWCO device.
Line Polarity Indicator & Fuse Protection
CCB/FCB Indicator Lamps & Fuses
A green LED is mounted on the PDB to indicate when line voltage
is applied. (The PDB also contains a yellow LED, a red LED,
and a test-run jumper, that are used during installation to verify
proper power connections.) A red LED on the CCB is used to
indicate when the 24 vac input fuse has blown. The FCB's also
have fuses on their 24vac power line. (Recommended
replacement fuses are: Littlefuse p/n 29707.5 for the 7.5 amp
CCB fuse, and Littlefuse p/n 297003 for the 3 amp FCB fuses.)
Repeated failure of fuse is an indication of failure to some
part of the system.
Yellow LED's are located near the micros on the CCB and FCB's.
These LED's are "heartbeat indicators" and blink approximately
twice per second to indicate that the micros are running.
Igniters
The Genesis 400 Series Boilers use a Silicon Carbide Igniter.
Appliance Operating Sequence
NOTE: The following sequence is based on a four-stage system
with all options and two-speed blowers. It is characteristic of
most system configurations.
1.
The EMC5000 controller has four modes of operation:
Initialization, Standby, Running and Service. The internal
CCB and FCB micros control these modes through a
sequence of steps (or States) which are further described
in the "UIM Operating Procedures" section.
2.
When power is applied to the system, it enters the
Initialization mode and the following automatic functions
are performed:
•
A. O. Smith opening screen is displayed on the UIM.
•
The system goes through a self-calibration indicated by the
green running LED blinking and then staying on: next the
red service LED and yellow standby LEDS come on; next
the stage 1 service and running LEDS blink on and off
followed by stage 2, stage 3, stage 4 and then back to stage
1,2,3,4 LEDS.
Summary of Contents for 500
Page 5: ...5 Figure 1A CCB Drawing 211758...
Page 6: ...6 Figure 1B FCB Drawing 211759...
Page 7: ...7 Figure 1C PDB Drawing 211760...
Page 14: ...14 CONNECTION DIAGRAM Drawing 211769 FIGURE 4...
Page 15: ...15...
Page 20: ...20 NOTES...
Page 21: ...21 NOTES...
Page 22: ...22 NOTES...