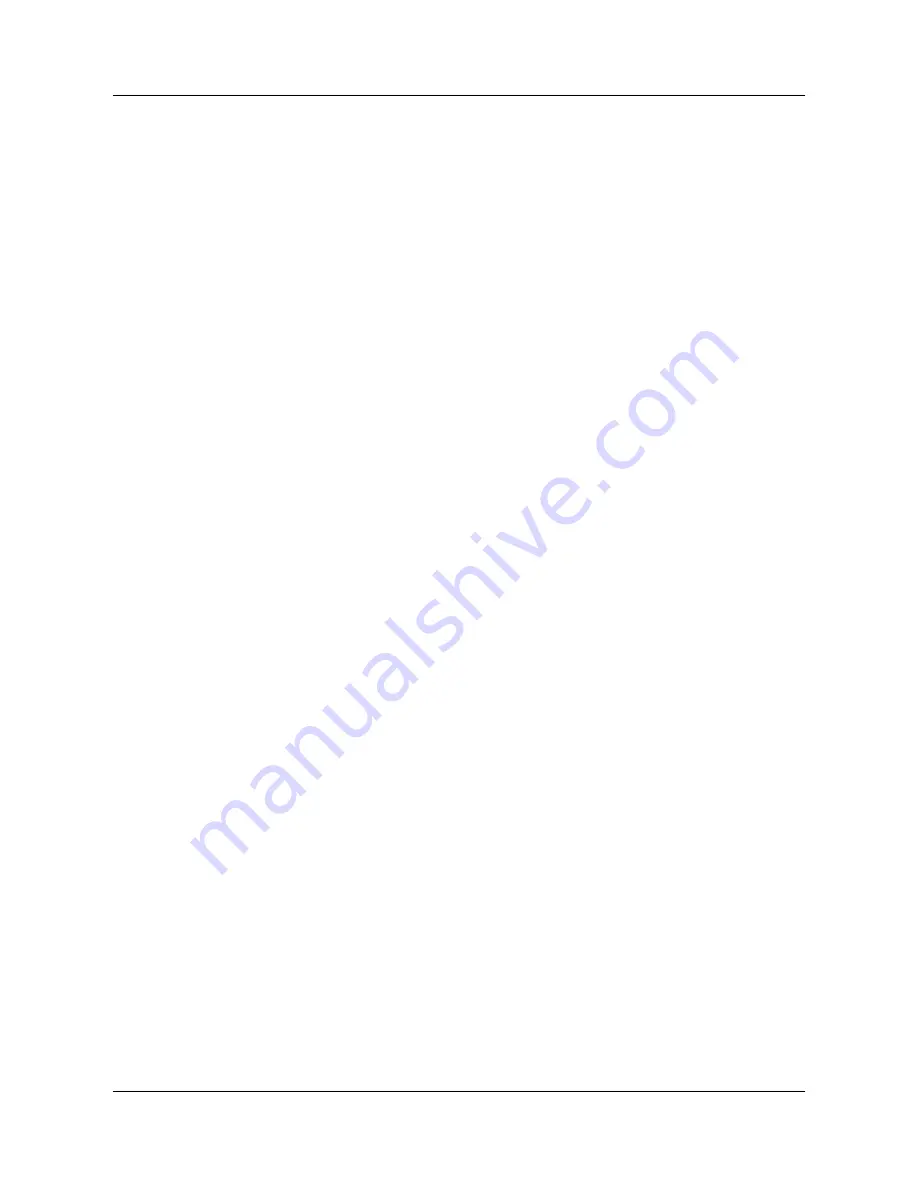
BTR TANK TYPE HEATERS
SERVICE WORKBOOK
A.O. Smith Water Products
Service Handbook
Irving, Texas ©2000
Training Department
50
PARTS LIST FOR BTR Models 120 Through 500(A)
Series 104 Through 109 Series
(Series 106/107 have a service switch on Circuit Board 6522; Series 108/109 have new
main burner production method. Both parts will automatically be shipped
on 104 thru 109 series heaters.)
Item
Parts Description
BTR-120 BTR-154
BTR-180 BTR-199 BTR-200
BTR-250
1
Main Burner, Orifice Bracket
98044(3)
98044(3)
98044(5)
98044(5)
98044(5)
98044(5)
2
Main Burner
192322
98047
192322
192322
192322
098047
3
Main Burner w/Pilot Bracket
193873-0
193873-1
193873-0
193873-0
193873-0
193873-0
4
Pilot Burner, Natural
193314-0
193314-0
193314-0
193314-0
R
193314-4
5
Pilot Burner, Propane
193314-1
193314-1
193314-1
193314-1
193314-1
193314-3
6
Gasket, Cleanout
99036
99036
99036
99036
99036
99036
7
Pressure Plate, Cleanout
99037
99037
99037
99037
99037
99037
8
Screw, Self tapping, Cleanout
69852
69852
69852
69852
69852
69852
9
Control, Ignition Module
193325
193325
193325
193325
193325
193325
10
Control, Dual w/eco
192828
192828
192828
192828
192828
192828
11
Drafthood
193597-0
193597-1
192957-0
192957-0
192957-0
193287
11
Drafthood 110, 111 Series
12
Manifold
76244-0
76244-0
76244-2
76244-2
76244-2
76244-2
13
Instruction Manual, (not illustrated)
193927
193927
193927
193927
193927
193927
14
Main Burner Orifice, Natural
76243-32
76243-30
76243-35
76243-32
76243-32
76243-xx
15
Main Burner, Orifice, Propane
76243-49
76243-46
76243-51
76243-49
76243-48
76243-xx
16
Anode Rod
43817-38 (2) 43817-38 (2)
43817-38 (4) 43817-38 (4) 180618-42 (3)
180618-42 (4)
17
T & P Relief Valve
99465-7
99465-7
99465-7
99465-7
99465-7
192467
18
Transformer
193444
193444
193444
193444
193444
193444
19
Inlet Tube
193729
192626
193729
193729
192626
192626
20
Gas Valve, Natural
192827-2
192827-2
192827-2
192827-2
192827-2
192827-2
21
Gas Valve, LP
192827-3
192827-3
192827-3
192827-3
192827-3
192827-3
22
Off/On Switch
193243
193243
193243
193243
193243
193243
Item
Parts Description
BTR-251 BTR-275
BTR-305 BTR-365
BTR-400
BTR-500
1
Main Burner, Orifice Bracket
98044(7)
98044(5)
98044(7)
98044(9)
98044(9)
98044(9)
2
Main Burner
98047
98047
192322
192322
192322
192322
3
Main Burner w/Pilot Bracket
193873-0
193873-1
193873-0
193873-0
193873-0
193873-0
4
Pilot Burner, Natural
193314-4
193314-4
193314-4
193314-4
193314-4
193314-4
5
Pilot Burner, Propane
193314-3
193314-3
193314-3
193314-3
193314-3
193314-3
6
Gasket, Cleanout
99036
99036
99036
99036
99036
99036
7
Pressure Plate, Cleanout
99037
99037
99037
99037
99037
99037
8
Screw, Self tapping, Cleanout
69852
69852
69852
69852
69852
69852
9
Control, Ignition Module
193325
193325
193325
193325
193325
193325
10
Control, Dual w/eco
192828
192828
192828
192828
192828
192828
11
Drafthood
193287
193287
193287
193287
193287
193287
11
Drafthood 110, 111 Series
12
Manifold
76244-3
76244-2
76244-3
76244-4
76244-4
76244-4
13
Instruction Manual, (not illustrated)
193927
193927
193927
193927
193927
193927
14
Main Burner Orifice, Natural
76243-xx
76243-xx
76243-37
76243-32
76243-31
76243-28
15
Main Burner, Orifice, Propane
76243-xx
76243-xx
76243-48
76243-49
76243-48
76243-44
16
Anode Rod
43817-38 (4) 180618-42 (3) 43817-38 (4) 180618-42(4) 180618-42 (3) 180618-42 (4)
17
T & P Relief Valve
192467
192467
192467
192467
192467
192467
18
Transformer
193444
193444
193444
193444
193444
193444
19
Inlet Tube
NA
192626
NA
192626
192626
192626
20
Gas Valve, Natural
192827-2
192827-2
192827-2
192827-2
192827-2
193366-0
21
Gas Valve, LP
192827-3
192827-3
192827-3
192827-3
192827-3
193366-1
22
Off/On Switch
193243
193243
193243
193243
193243
193243
∗
For complete parts list call 1-800-433-2545
Summary of Contents for 120 trough 500
Page 1: ......