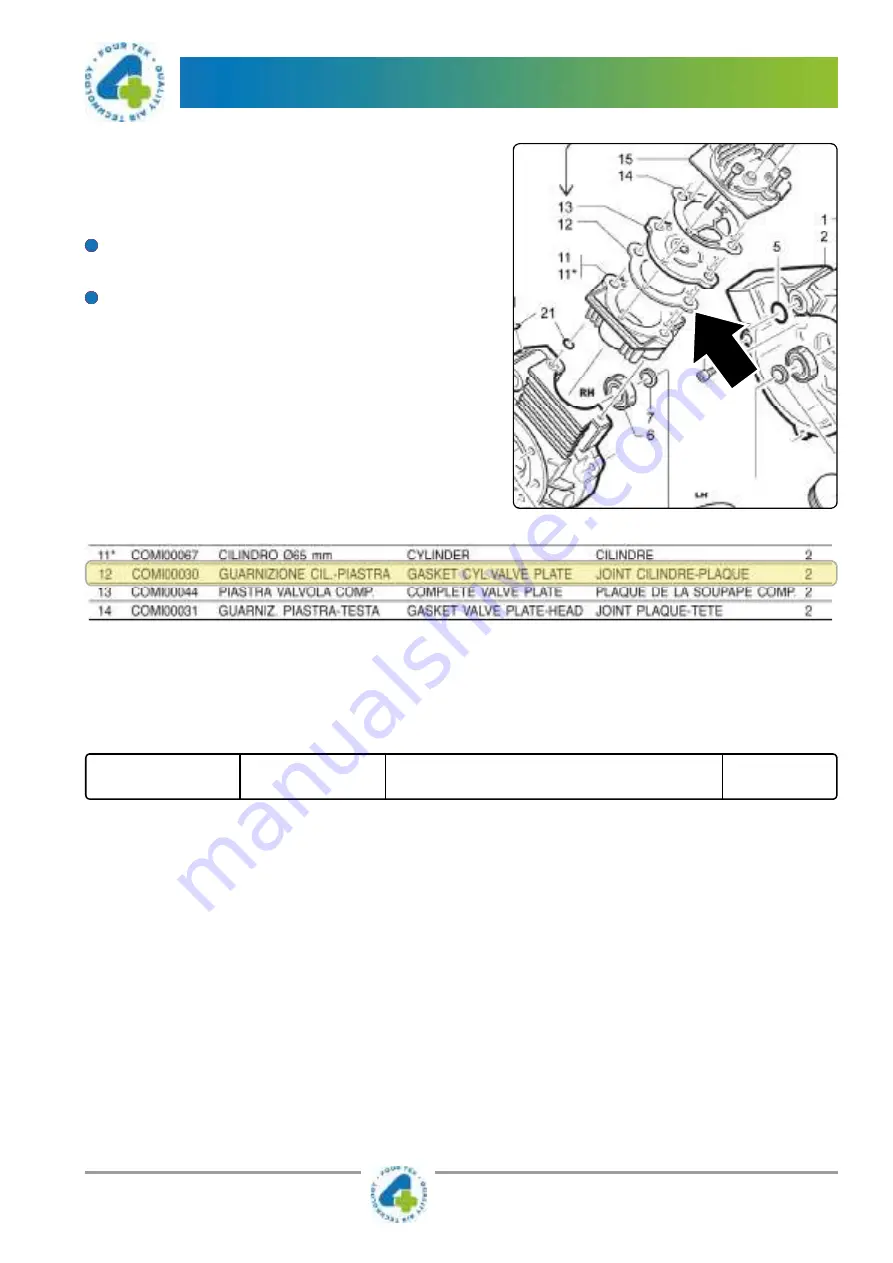
This manual is the property of
. No part of it may be reproduced in any form.
MIRAGE Line Compressors Instruction Manual
9 - 03
How to order replacement parts
Use the following procedure to order replacement
parts:
Find the required part and its number on the
drawings on Page 9-02.
Check the code, description and quantity
against the part number in the table on page
9-03.
Part no.
in drawing
Code
Quantity
Description
12
2
COMI00030
HEAD PLATE GASKET
Fill in the order as follows: