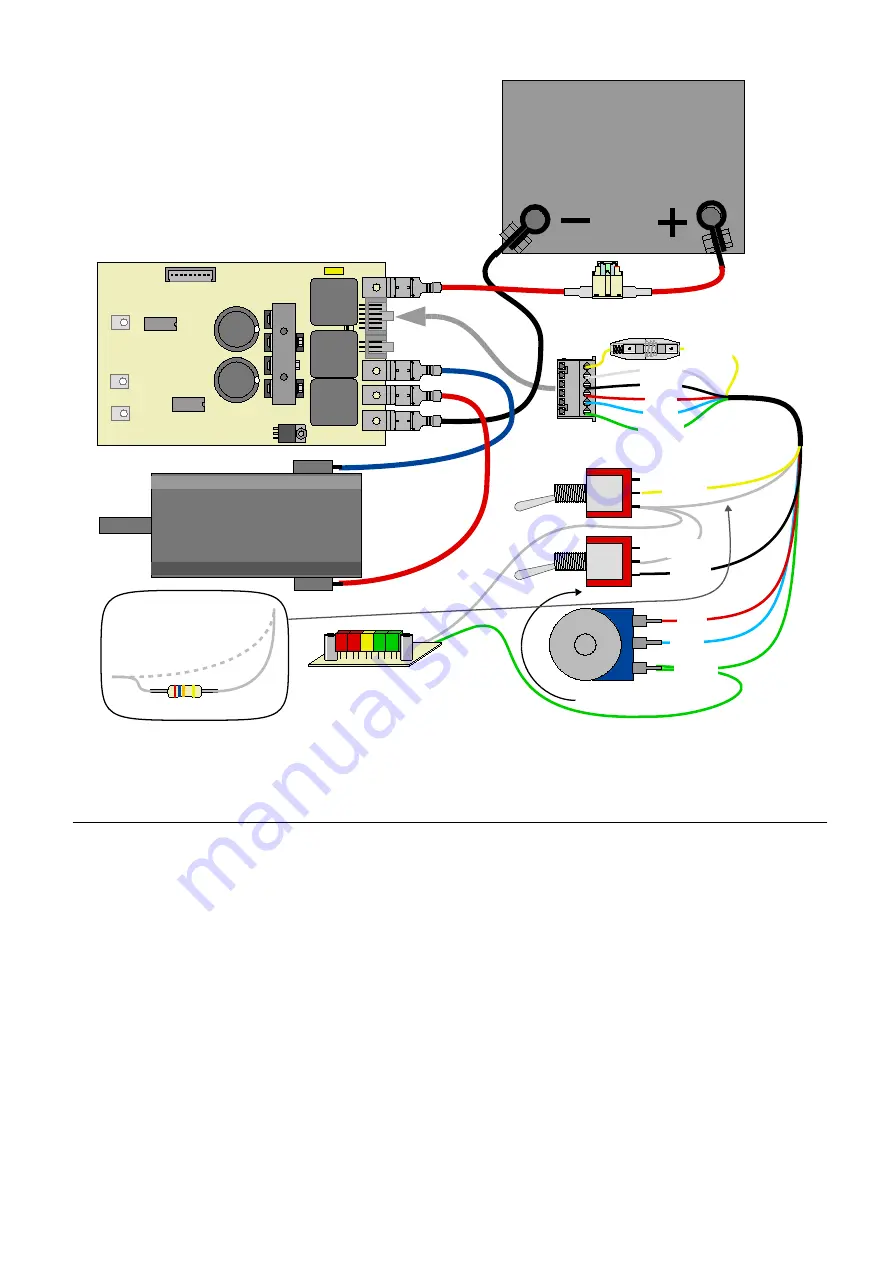
Page 6
Pro-120 controller instructions
6 core cable
Speed control pot
Battery Condition Meter
Ignition wire removed
To fit battery discharge
protection.
Reverse switch
Ignition switch
Black
Green
Blue
Red
Black
Black
Blue
Red
Red
Red
Yellow
White
R fitted (12K)
uvp
Permanent
magnet
motor
Yellow
White
Black
Green
Blue
Red
Fuse or breaker, see text
The diagram shows the simplest connections needed
to use the controller.
More information on wiring follows.
Yellow is directly connected to bve. White
and black may also be bve (depending on the
control switches). Green is battery -ve and blue and
red are the control pot.
Fuse in yellow wire is optional but recommended -
see p 15.
7
Connections
8.01
Battery wiring
Use only good quality battery connectors: the
controller feeds current back the battery during
braking and if a battery connector falls off when
braking this regenerated current can pump up the
voltage on the dud battery connection. Although the
controller is protected against damage, this is not
advised since control is lost. The same will happen if
a fuse or circuit breaker opens during braking.
Wire size.
Use heavy duty wire for the battery leads and make
them as short as possible. This also applies to the
battery linking wire on 24v systems.
4mm (12awg) wire is ‘officially’ rated to handle 41
amps continuously. At 100 amps it gets too hot to
touch within about 60 seconds. We therefore suggest
you use at least 6.0mm² (10awg) wire for battery
connections.
On the 12v controllers, voltage loss in the wire is
important and you may need to use two lengths of
6mm² wire for the battery - depending on their
length. Excessive voltage loss will cause the voltage
8
Power Connections