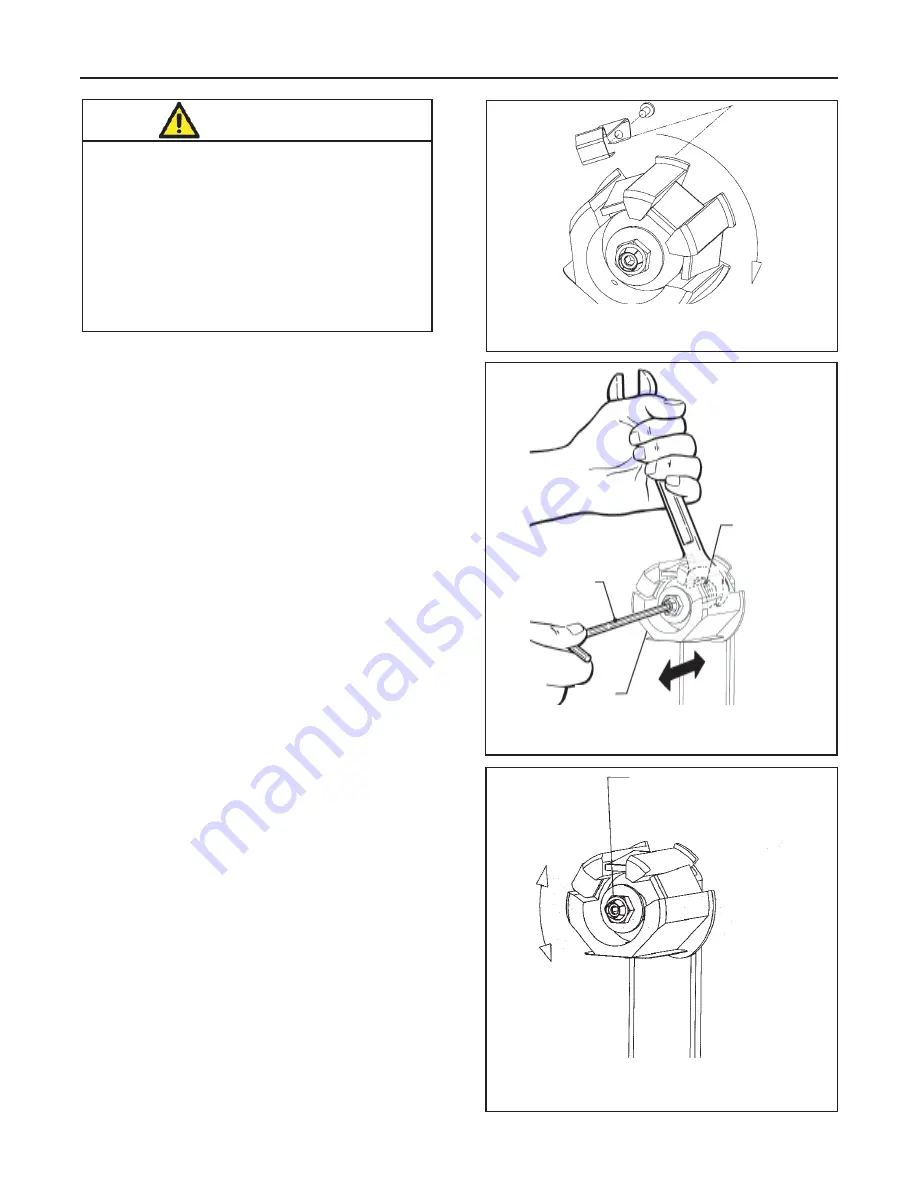
14
Tape Drum Friction Brake
–
Figure 5-3
The tape drum friction brake on each taping head is
pre-set for normal operation to prevent tape roll over
travel. Should tension adjustment be required, turn
the self-locking nut on the shaft to vary compression
of the spring. Turn the nut clockwise to increase the
braking force, and counterclockwise to decrease the
braking force. Adjust brake to minimum tension to
prevent excessive tape roll over travel.
Tape Latch Alignment
–
Figure 5-1
The Latching tape drum assembly is pre-set to
accommodate 72mm [3 inch] wide tape. The tape drum
assembly is adjustable to provide alignment of narrower
tapes.
To move the latch to a position that corresponds to a
new tape core width
(Figure 5-1):
1. Remove screw from the latch.
2. Move to the latch to the position that corresponds to
the tape core width.
3. Replace screw in the new latch location.
To adjust or center the tape width on the centerline
of the taping head, and therefore box center seam,
(Figure 5-2):
1.
Loosen the locking hex nut behind tape drum
bracket on tape drum shaft. Use an adjustable
wrench or 25mm open end wrench.
Note –
To set up 72mm tape drum for 48mm tape,
disassemble tape drum from bracket and install lock nut
between tape drum and bracket as shown in inset,
Figure 5-3.
2. Turn tape drum shaft in or out to center the tape
web (use 5mm hex wrench).
3. Tighten locking hex nut to secure the adjustment.
No other components require adjustment for tape web
alignment.
Note –
Excess braking force will cause poor tape
application and may lead to tape tabbing on
the trailing tape leg.
Adjustments
•
To reduce the risk associated with shear,
pinch, and entanglement hazards:
−
Turn air and electrical supplies off on
associated equipment before performing any
adjustments, maintenance, or servicing the
machine or taping heads
−
Never attempt to work on the taping head
or load tape while the box drive system is
running
WARNING
2+ STD 3" Taping Head - NA
2011 December
Figure 5-1 – Tape Latch Alignment
Figure 5-2 – Tape Web Alignment
Figure 5-3 – Tape Drum Friction Brake
5mm Hex
Wrench
Shaft
25mm Hex
Wrench
Adjustment Nut,
Tape Drum Brake
Summary of Contents for Matic 700a3
Page 4: ...THIS PAGE IS BLANK...
Page 6: ...THIS PAGE IS BLANK...
Page 8: ...8 THIS PAGE IS BLANK...
Page 10: ...10 iv THIS PAGE IS BLANK...
Page 46: ...34 THIS PAGE IS BLANK...
Page 48: ...36 THIS PAGE IS BLANK...
Page 49: ...37 16 TECHNICAL DIAGRAMS 16 1 Electric Diagram 700a3 NA 2011 July...
Page 52: ...40 THIS PAGE IS BLANK...
Page 56: ...44 700a3 NA 700a3 Figure 2806 12 1 11 10 9 7 8 1 4 3 5 6 1 2 2011 July...
Page 72: ...60 Figure 5669 700a3 10 13 14 3 12 4 9 9 8 7 9 7 11 15 6 5 16 9 1 2 5 6 700a3 NA 2011 July...
Page 76: ...64 THIS PAGE IS BLANK...
Page 78: ......
Page 80: ...THIS PAGE IS BLANK...
Page 82: ...THIS PAGE IS BLANK...
Page 86: ...2 THIS PAGE IS BLANK...
Page 122: ...THIS PAGE IS BLANK...
Page 123: ......
Page 124: ......