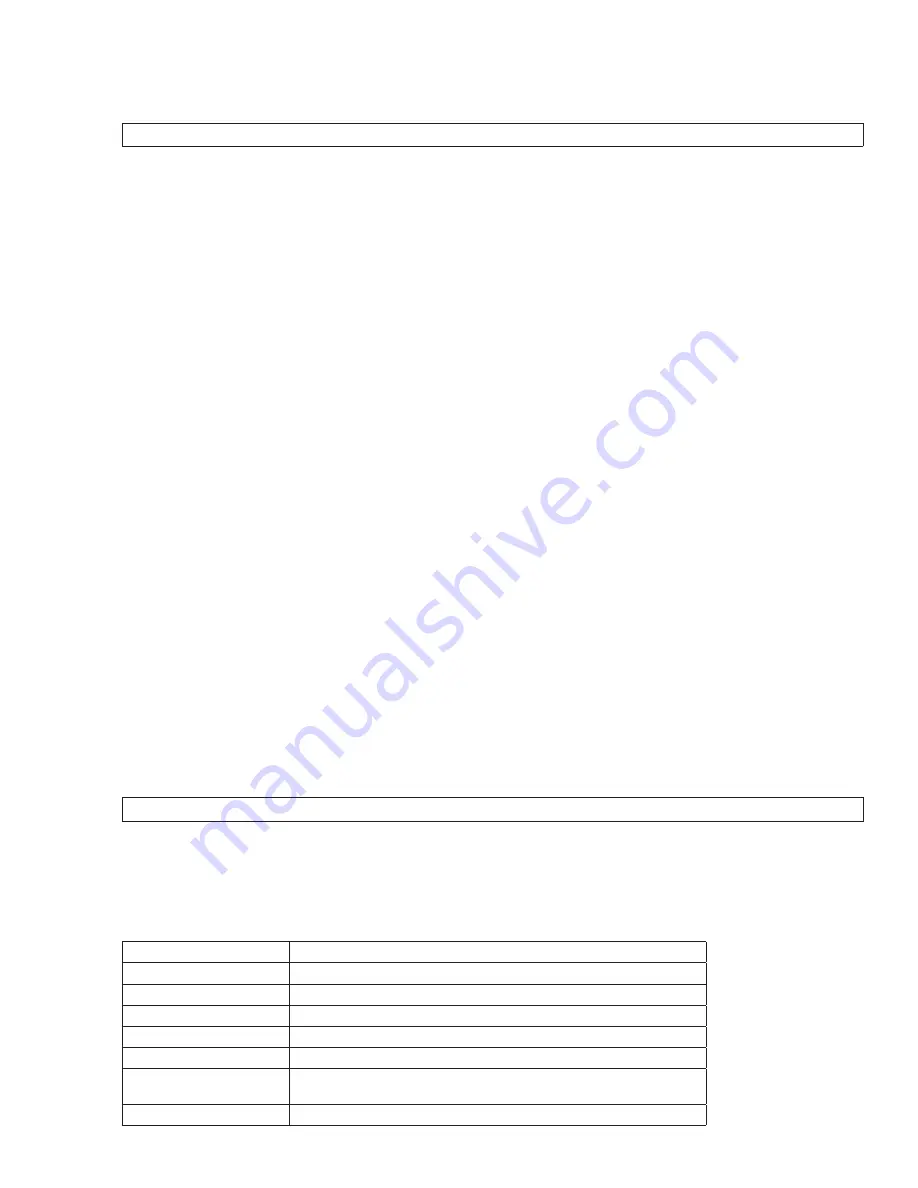
7
4.0 TRAINING
It is the responsibility of the user and purchaser of the Emergency Descent Device to be trained in the correct care and
use of this equipment. The user and purchaser must be aware of the operating characteristics, application limits, and
consequences of improper use of this equipment.
WARNING:
Training must be conducted without exposing the trainee to a fall hazard. Training should be repeated on a periodic basis.
5.0 INSPECTION
5.1 INSPECTION FREQUENCY:
The product shall be inspected before each use by a user and, additionally, by a Competent
Person other than the user at intervals of no longer than one year. A higher frequency of equipment use and harsher
conditions may require increasing the frequency of Competent Person inspections. The frequency of these inspections
should be determined by the Competent Person per the specific conditions of the worksite.
5.2 SERVICE:
The Emergency Descent Device must be sent to an authorized service center every two years for inspection
and service. See Section 6.2.
5.3 RFID TAG:
115 and 200 Ft Emergency Descent Devices are equipped with a RFID Radio Frequency Identification (RFID)
tag (Section 8, Item D). The RFID tag on the Emergency Descent Device can be used in conjunction with the RFID
handheld reading device and the web based RFID portal to simplify inspection and inventory control and provide records
for fall protection equipment. If you are a first-time user, contact a Customer Service representative in the US at 800-
328-1667. If you have already registered, go to www.3M.com. Follow the instructions provided with the handheld RFID
reader or on the web RFID portal to transfer your data to the web log.
5.4 INSPECTION STEPS:
Per the intervals defined in Section 5.1, inspect the Emergency Descent Device as follows:
Step 1.
Inspect the Emergency Descent Device for loose fasteners and bent or damaged parts.
Step 2.
Inspect the Emergency Descent Device housing for distortion, cracks, or other damage. Ensure the descent
brake assembly is not damaged or distorted.
Step 3.
The Emergency Descent Device lifeline must pull out and retract fully. Inspect entire wire rope for cuts, kinks,
broken wires, corrosion, or severely abraded areas. Slide the cable bumper up and inspect the Wire Rope and
ferrules for cracks, corrosion, broken wires, etc.
Step 4.
Device labels must be present and fully legible (see Section 8).
Step 5.
Inspect for corrosion on the device.
Step 6.
Inspect connecting hooks or carabiners for damage, corrosion, and working condition.
Step 7.
Inspect all system components and subsystems according to manufacturer’s instructions.
Step 8.
Record inspection results in the Inspection and Maintenance Log (Section 9) or on the RFID web portal
(Section 5.2).
6.0 MAINTENANCE, SERVICE, STORAGE
6.1 MAINTENANCE AND SERVICE:
Periodically clean the exterior of the Emergency Descent Device with water and mild
detergent. Position the device so excess water can drain out. Clean labels as required. Clean device lifeline with water
and mild detergent. Rinse and thoroughly air dry. Do not force dry with heat. An excess buildup of dirt, paint, etc., may
prevent the lifeline from retracting back into the device.
Additional maintenance and servicing must be completed by an authorized service center. Do not attempt to disassemble
the device.
NOTE:
Only 3M Fall Protection or parties authorized in writing may make repairs to this equipment.
6.2 STORAGE AND TRANSPORT:
Store and transport the Emergency Descent Device in a cool, dry, clean
environment, out of direct sunlight. Avoid areas where chemical or organic vapors are present. Thoroughly inspect the
Emergency Descent Device after extended storage.
7.0 SPECIFICATIONS
7.1 MATERIALS
Housing:
Cast Aluminum
Anchorage Handle:
Stainless Steel
Fasteners:
Stainless Steel
Main Shaft:
Stainless Steel
Connecting Hook:
Stainless Steel
Cable Bumper:
Urethane
Lifeline (Stainless Steel): 3/16” (4.8 mm) dia. 7x19 Aircraft Wire Rope, 3,600 lbs (16 kN)
minimum tensile strength
Finish Paint:
Polyester Baked Finish