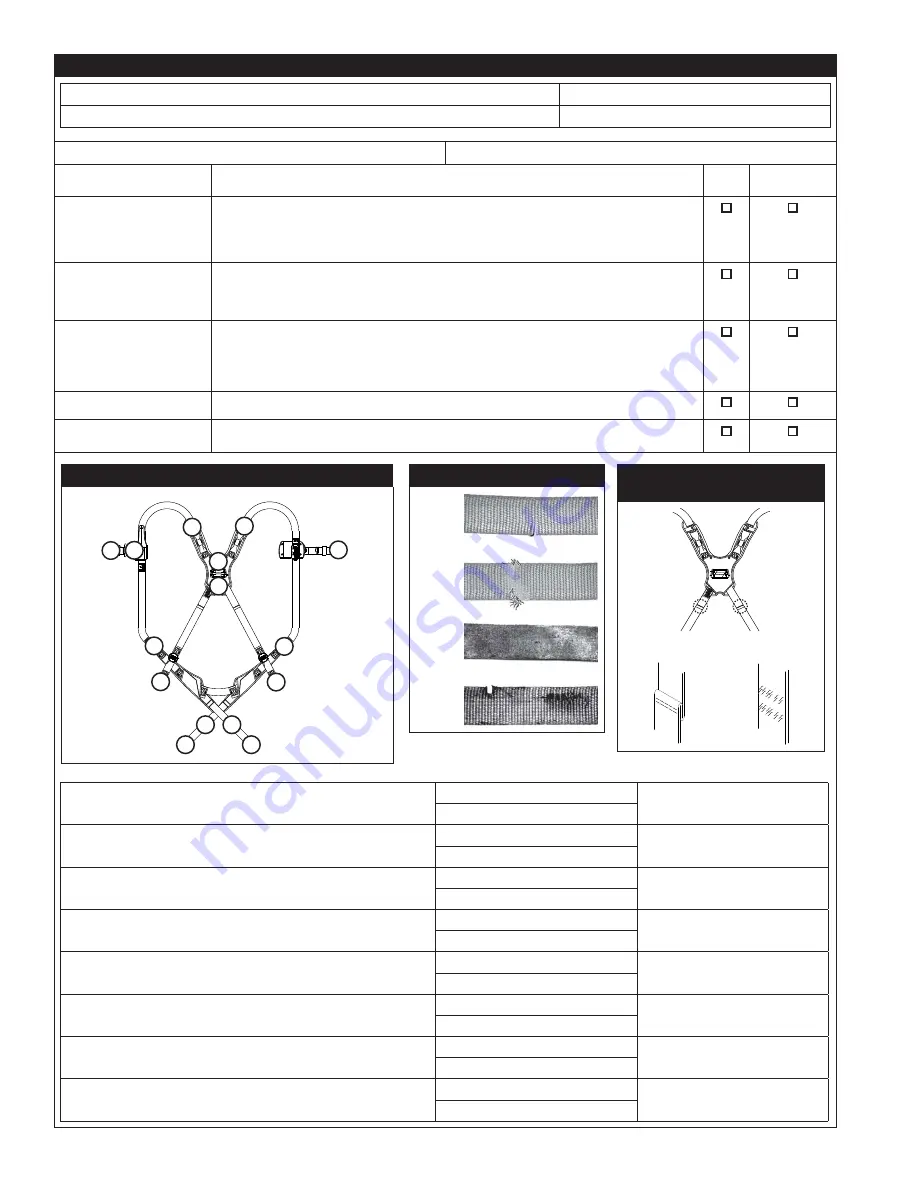
18
Table 1 – Inspection and Maintenance Log
Serial Number(s):
Date Purchased:
Model Number:
Date of First Use:
Inspection Date:
Inspected By:
Component:
Inspection:
(See Section 2.2 for Inspection Frequency)
User
Competent
Person
Harness Hardware
(Diagram 1)
Inspect harness hardware including buckles (1), adjusters (2), D-rings (3), Easy-Link (4),
loop keepers (5), lanyard parking (6), etc. These items must not be damaged, broken, or
distorted, and must be free of sharp edges, burrs, cracks, worn parts, or corrosion. PVC
coated hardware must be free of cuts, rips, tears, holes, etc. in the coating to ensure non-
conductivity. Ensure buckles and adjusters work smoothly.
Webbing & Stitching
(Diagram 2)
Inspect webbing; material must be free of frayed, cut, or broken fibers. Check for tears,
abrasions, mold, burns, or discolouration. Inspect stitching; Check for pulled or cut
stitches. Broken stitches may be an indication that the harness has been impact loaded
and must be removed from service.
Stitched Impact Indicators
(Diagram 3)
The Stitched Impact Indicators are sections of webbing lapped back on themselves and
secured with a specific stitch pattern. The stitch pattern is designed to release when
the harness arrests a fall or is exposed to equivalent force.
If an Impact Indicator
has been activated (indicated), the harness must be removed from service and
destroyed.
Labels
All labels should be present and fully legible. See Figure 15.
System & Subsystem
Components
Inspect each system component or subsystem according to the manufacturer instructions.
Diagram 1 – Hardware
3
4
6
6
1
1
3
2
2
1
1
5
5
1
1
Diagram 2 – Webbing
Cut
Frayed
Heavily
Soiled
Welding
Burns
Diagram 3 – Impact
Indicator
ü
Good
û
Indicated
Corrective Action/Maintenance:
Approved By:
Next inspection due:
Date:
Corrective Action/Maintenance:
Approved By:
Next inspection due:
Date:
Corrective Action/Maintenance:
Approved By:
Next inspection due:
Date:
Corrective Action/Maintenance:
Approved By:
Next inspection due:
Date:
Corrective Action/Maintenance:
Approved By:
Next inspection due:
Date:
Corrective Action/Maintenance:
Approved By:
Next inspection due:
Date:
Corrective Action/Maintenance:
Approved By:
Next inspection due:
Date:
Corrective Action/Maintenance:
Approved By:
Next inspection due:
Date: