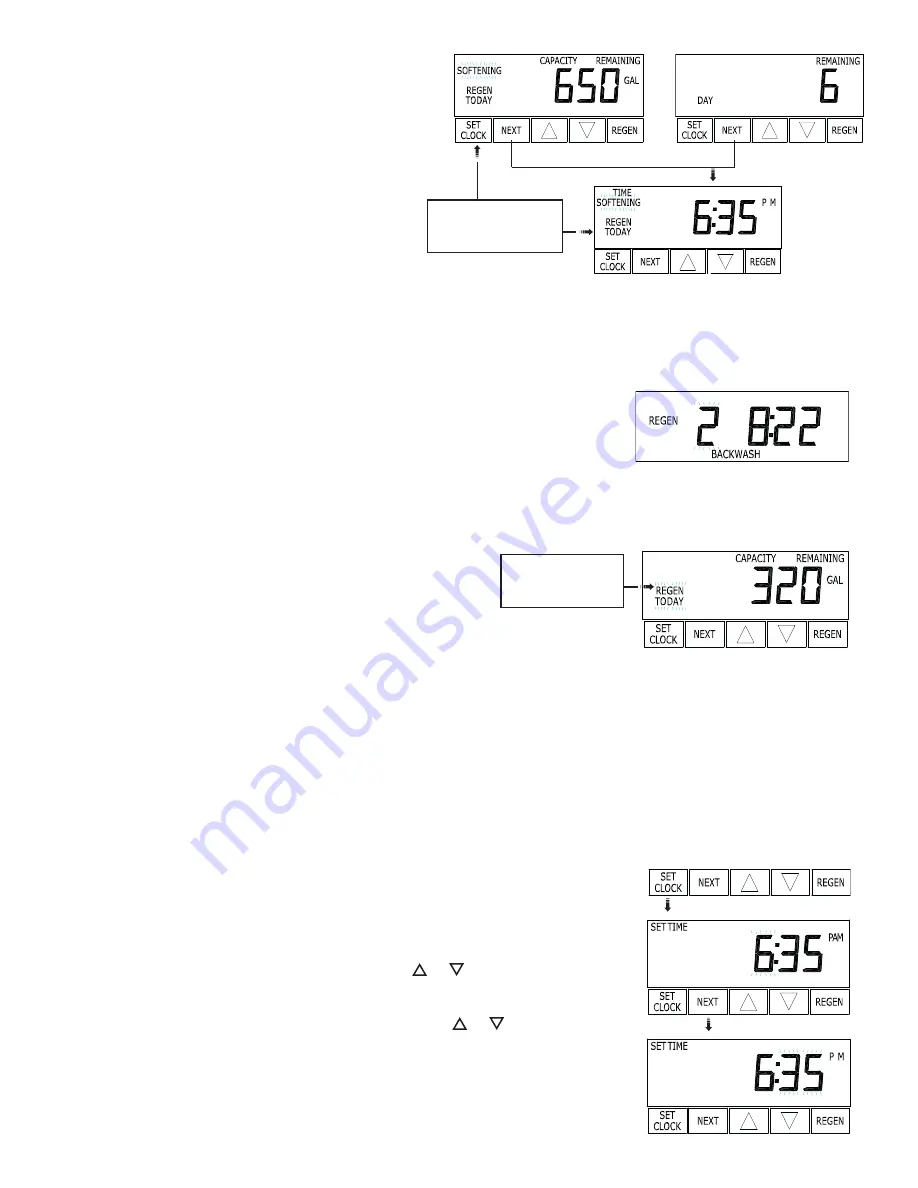
User Display Settings
General Operation
When the system is operating, one of two displays will be
shown. Pressing NEXT will alternate between the displays.
One of the displays is always the current time of day. The sec-
ond display is one of the following: days remaining or capacity
remaining. Days remaining is the number of days left before
the system goes through a regeneration cycle. Capacity re-
maining is the number of gallons that will be treated before the
system goes through a regeneration cycle. The user can scroll
between the displays as desired.
OR
REGEN TODAY will be
displayed if a regeneration
is expected “Tonight.”
When the system begins to regenerate, the display will change to include information about the step of the regeneration process and the time
remaining for that step to be completed. The system runs through the steps automatically and will reset itself to help provide treated water
when the regeneration has been completed.
Manual Regeneration
Sometimes there is a need to regenerate the system sooner than
when the system calls for it, usually referred to as manual regen-
eration. There may be a period of heavy water usage because of
guests or a heavy laundry day.
To initiate a manual regeneration at the present delayed regeneration time, press and release “REGEN”. The words “REGEN TODAY” will fl ash
on the display to indicate that the system will regenerate at the preset delayed regeneration time.
NOTE: If you pressed the “REGEN” button in error, pressing the button again will cancel the request.
To initiate a manual regeneration immediately, press and hold the “REGEN” button for 3 seconds. The system will begin to regenerate immedi-
ately. The request cannot be cancelled.
NOTE: If brine tank does not contain salt, fi ll with salt and wait at least two hours before regenerating.
Set Time of Day
The user can also set the time of day. Time should only need to be set after extended
power outages or when daylight saving time begins or ends. If an extended power outage occurs,
the time of day will fl ash on and off which indicates the time of day should be reset.
Step 1 - Press SET CLOCK.
Step 2 - Current Time (hour): Set the hour of the day using
or
button. AM/PM
toggles after 12. Press NEXT to go to Step 3.
Step 3 - Current Time (minutes): Set the minutes of the day using
or
buttons.
Press NEXT to exit Set Clock. Press “REGEN” to return to previous step.
If the system has called for a regeneration that will occur at the preset time of regeneration, the words “REGEN TODAY” will appear on the
display.
When water is being treated (i.e. water is fl owing through the system) the word “SOFTENING” fl ashes on the display if a water meter is in-
stalled.
Regeneration Mode
Typically a system is set to regenerate at a time of low water usage. An example of a time with low
water usage is when members of a household are asleep. If there is a demand for water when the
system is regenerating, untreated water will be used.
REGEN TODAY will
Flash if a regeneration
is expected “Tonight.”
3-4
Summary of Contents for CWS Series
Page 2: ......