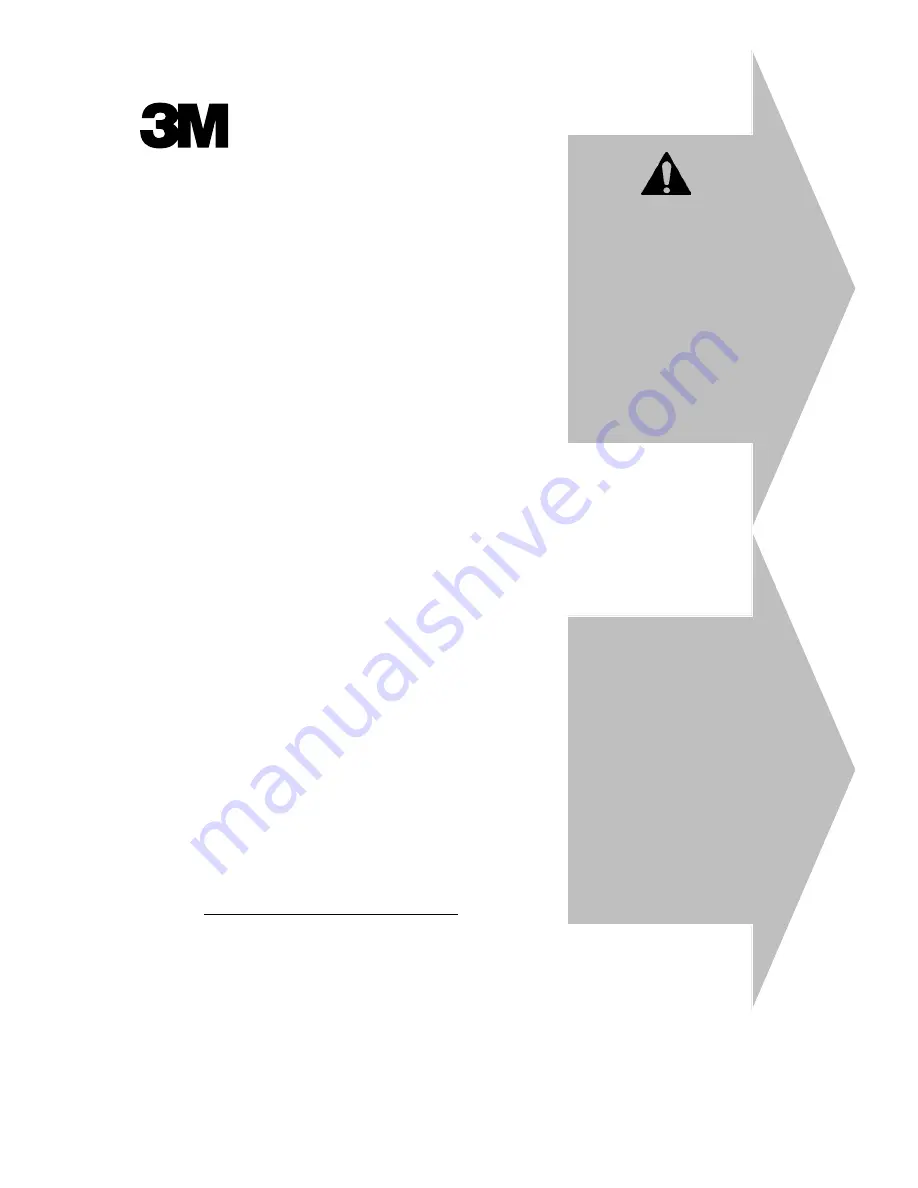
3M Packaging Systems Division
3M Center, Building 220-8W-01
St. Paul, MN 55144-1000
Serial No.
_____________________________________
For reference, record taping head(s) serial number(s) here.
Instructions and Parts List
AccuGlide II
STD 3 Inch
Upper and Lower
Taping Heads
Type 39600
TM
Read "Important Safeguards",
page 2 and also operating
"Warnings", page 7
BEFORE INSTALLING OR
OPERATING THIS
EQUIPMENT.
Important Safety
Information
It is recommended you
immediately order the
spare parts listed on
page 17. These parts are
expected to wear through
normal use, and should
be kept on hand to minimize
production delays.
Spare Parts
AccuGlide
™
is a Trademark of
3M, St. Paul, MN 55144-1000
Litho in U.S.A
© 3M 1998 44-0009-1922-3(C28.0)
Summary of Contents for AccuGlide II STD 3 Inch
Page 9: ...4 Figure 2 1 Dimensional Drawing Specifications Continued ...
Page 19: ...14 THIS PAGE IS BLANK ...
Page 24: ...19 Taping Head Assemblies AccuGlide II STD 3 Inch ...
Page 25: ...20 Figure 2948 Upper Head ...
Page 27: ...22 Figure 2949 Upper and Lower Heads ...
Page 29: ...24 Figure 2950 Upper Head ...
Page 31: ...26 Figure 2951 Upper and Lower Heads ...
Page 33: ...28 Figure 2952 Upper and Lower Heads ...
Page 35: ...30 Figure 2953 Upper and Lower Heads ...
Page 37: ...32 Figure 2954 Lower Head ...
Page 39: ...34 Figure 2955 Lower Head ...