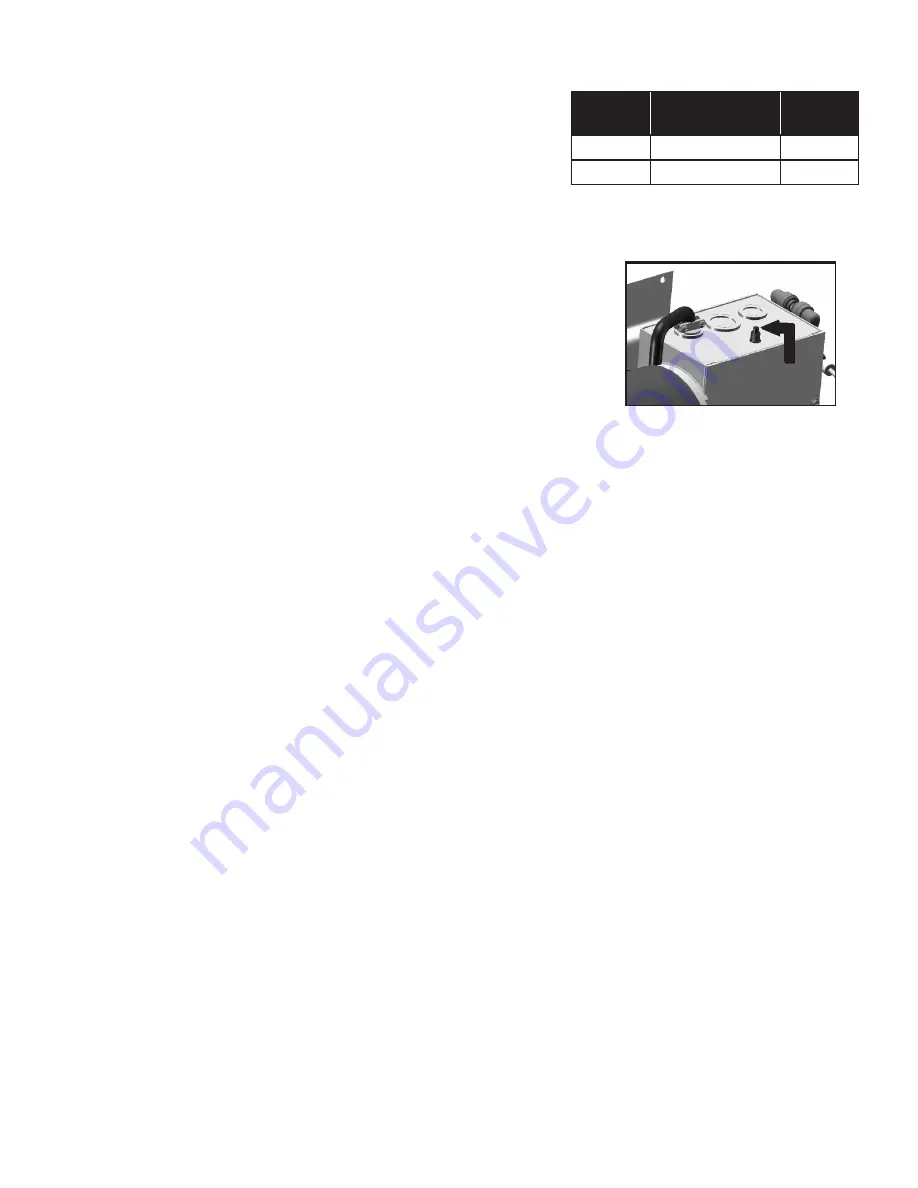
10
Start Up Test Checklist
Close the tank shut off valve, open the tank line sample valve.
• Pump turns on
√
• Water will flow thru the tank line sample valve and drain line
√
Keep the tank shut off valve closed and close the tank line sample valve.
• Pump turns off
√
• Water will stop flowing from the drain line.
√
• The operating pressure gauge will read 0 psi (0 kPa) at this point.
√
• Tank pressure gauge will read 60 psi (414 kPa, 4.14 bar) for 110-120 VAC systems and 70 psi (483 kPa, 4.83 bar) for 220-240 VAC systems
√
Open the tank line sample valve.
• Pump will turn on.
√
• Tank pressure gauge will read 0 psi (0 kPa).
√
• Permeate being rinsed for first 25 seconds
√
• After 30 seconds of operation, check production rate.
√
• After 30 seconds of operation, check operating pressure. The operating pressure gauge should read 110-120 psi.
√
• After 30 seconds of operation, check TDS reductions.
√
Close the tank line sample valve and open the tank shut off valve. Allow storage tank to fill.
• Verify the tank pressure gauge increases to 60 psi (414 kPa, 4.14 bar) for 110-120 VAC systems and 70 psi (483 kPa, 4.83 bar) for 220-240 VAC
systems
√
• Verify the pump turns off and the drain line flow stops.
√
System Start Up
1. Turn on the feedwater supply.
2. Open unit inlet shutoff valve.
3. Power the unit by plugging into electrical outlet.
4. Open Pre-Filter flush valve to vent air from system and flush for
10 gallons (approximately 5 minutes).
5. Close Pre-Filter flush valve. The unit operating pressure gauge (left gauge) should
read between 110-120 psi. (See Operating Pressure instructions to adjust)
6. Complete blending valve adjustment procedure below. (See instructions below)
7. Close the blend line shut off valve. (Figure 5, #1)
8. Allow storage tank to fill until the RO system turns OFF on full tank (See chart). Tank operating
pressure for the 110-120VAC version is ON at 40 psi (276 kPa, 2.76 bar) and OFF at 60 psi (414
kPa, 4.14 bar) (right gauge). Tank operating pressure for the 220-240VAC is ON at 50 psi (345
kPa, 3.45 bar) and OFF at 70 psi (483 kPa, 4.83 bar).
9. Flush membrane by opening tank line sample valve and empty storage tank to drain. Operate the
system for at least 24 hours to flush the RO membrane. Discharge all water generated during the
flushing procedure to drain. Close the tank line sample valve after flushing is complete.
10. Sanitize the storage tank and RO system according to the storage tank and RO system
sanitizing instructions on page 11.
11. Open the blend line shut off valve (if product water blending is desired). Allow storage tank to
refill. System is now ready for use.
Part Number
Pressure Volume
Approximate
Time to Fill
5598408
20 gallons (76 liters)
0.6 hours
5598409
40 gallons (151 liters)
1.2 hours
Required (Sold Separately)
Figure 4 (Reset Button)
Summary of Contents for 5629101
Page 19: ...19 Notes ...