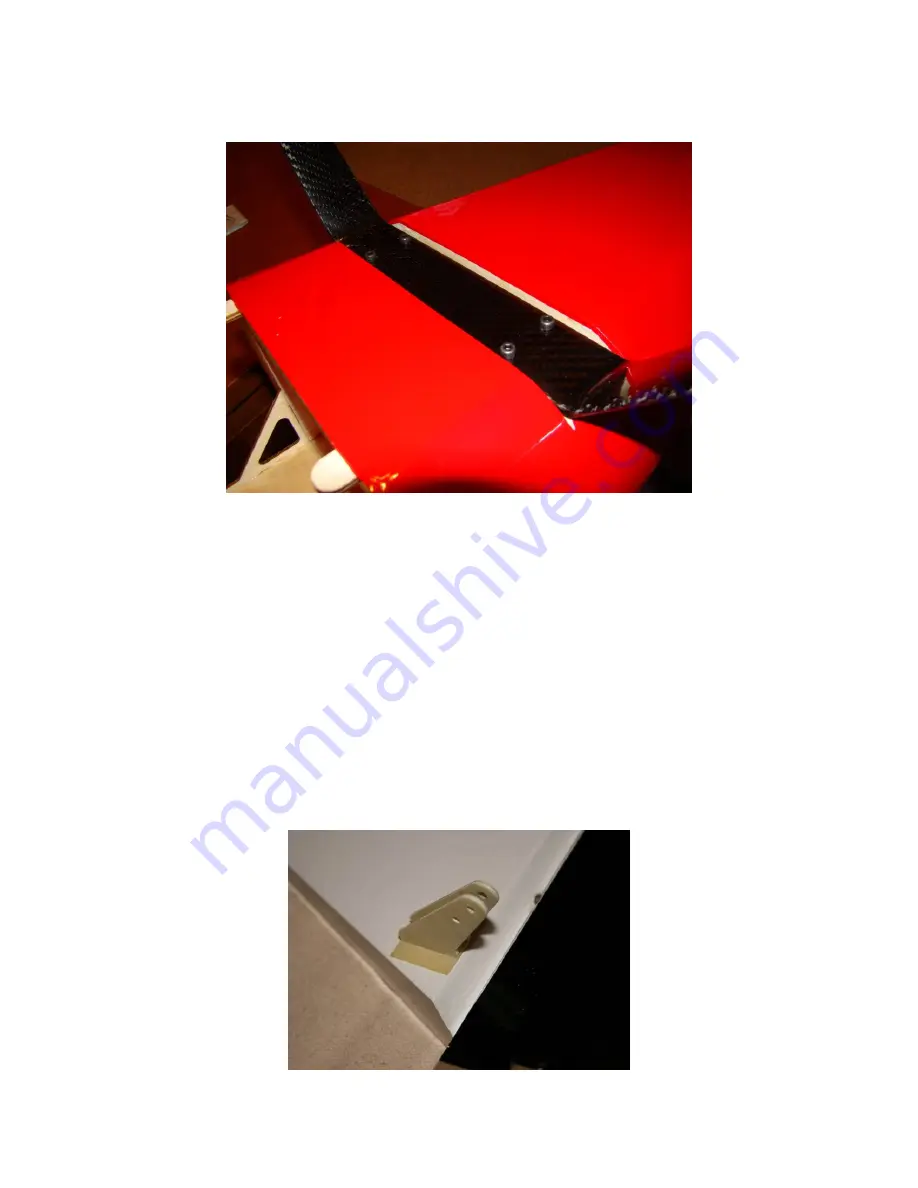
Attach the main gear to the fuselage using 4 x 4mm screws, washers, and locknuts.
Attach the cover plate over the landing gear screws using epoxy glue or silicone adhesive.
Elevator and Aileron Control Horns
Your Slick features phenolic control horns. The slots for the horns are pre-cut into all of the control
surfaces.
You will need to remove the covering over each of these locations. The best way to trim covering on this
aircraft is with a hot pencil-tip soldering iron. This method gives a clean cut and also seals the edges of
the covering at the cut line. You can also use a hobby knife if you cannot use a soldering iron for this job,
but the iron is recommended.
1. First, locate the control horn location in each control surface.
2. Cut away the covering over the two slots.
3. Assemble the control horns as shown, and temporarily push the horn into the slots in the control
surface (do not use glue at this time).