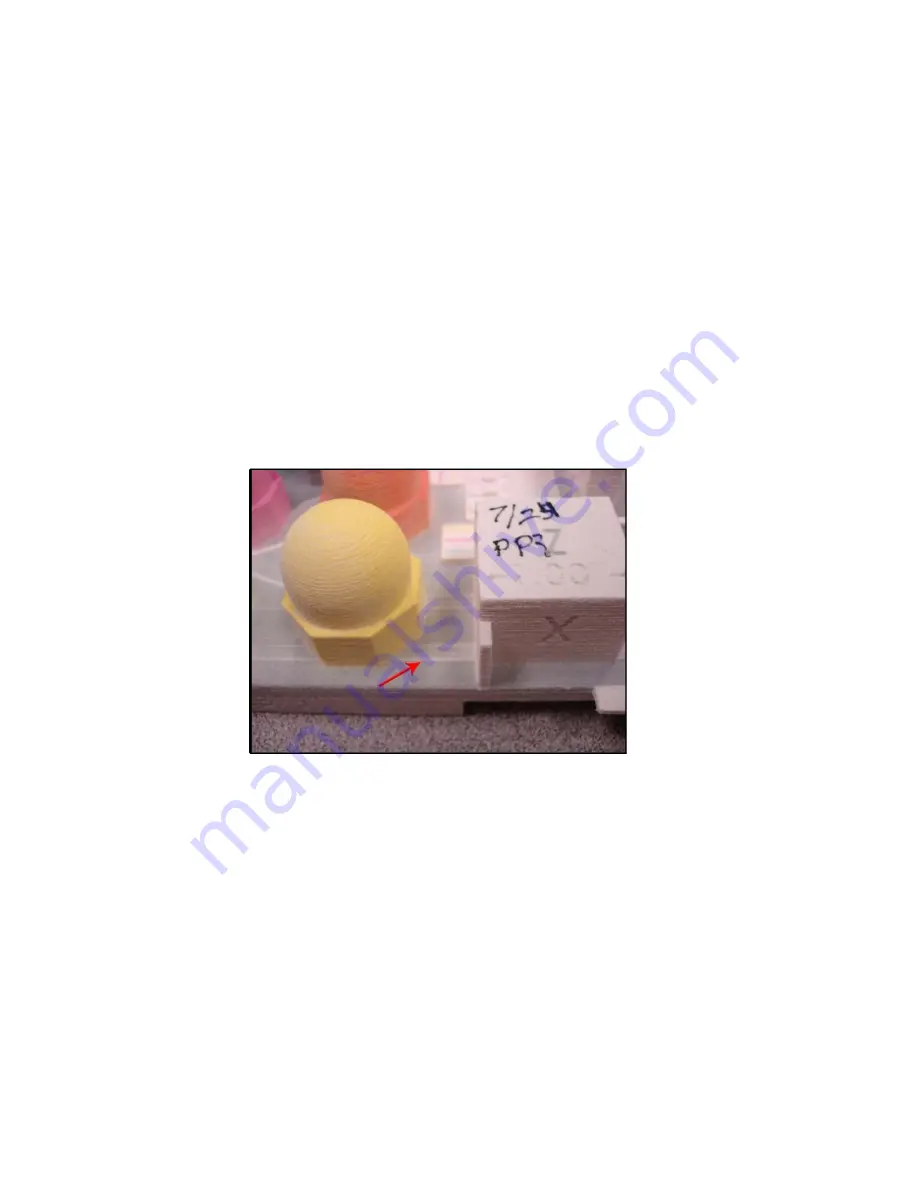
ProJet
®
860
Pro
User Manual
Troubleshooting the ProJet x60Pro
3dscentral.3dsystems.com
74
All Rights Reserved
5/12/13
7.10 Part Quality Issues - Streaky or Striped Parts, Delamination
Explanation:
Streaky or striped parts are caused either by Core buildup on the print head, a failed print
head, or an electrical issue within the printer. Delamination (layers splitting apart) may be due to a print
head that is caked with Core, or a pause in network communications.
Solution - Both:
•
Clean the service station. See
Section 3.5, ’Clean The Service Station’
.
•
Clean the parking caps. See
Section 3.3, ’Clean The Parking Caps’
.
•
Ensure the printer has cleaning solution.
•
Realign the print heads to ensure proper alignment.
•
Clean the Fast Axis Rails of any debris and reboot the printer. See
Section 3.4, ’Clean The Fast
Axis Rails and Carriage’
.
If the problem persists,
•
Clean the pogo pins and the print head contacts.
•
Realign the heads. If the pattern shows striping or streaking, one or more print heads may have
failed. Change the print head and realign the heads. See
Section 7.4, ’Alignment Errors’
.
Additional Solution - Delamination
Check your PC settings. The printer may be pausing as it waits for additional data from the PC. While
pausing, the printed part begins to dry and as a result the next layer does not stick to the last layer printed.
Your PC should be dedicated to 3D Print. Your PC Power Management software should be completely
shut off.