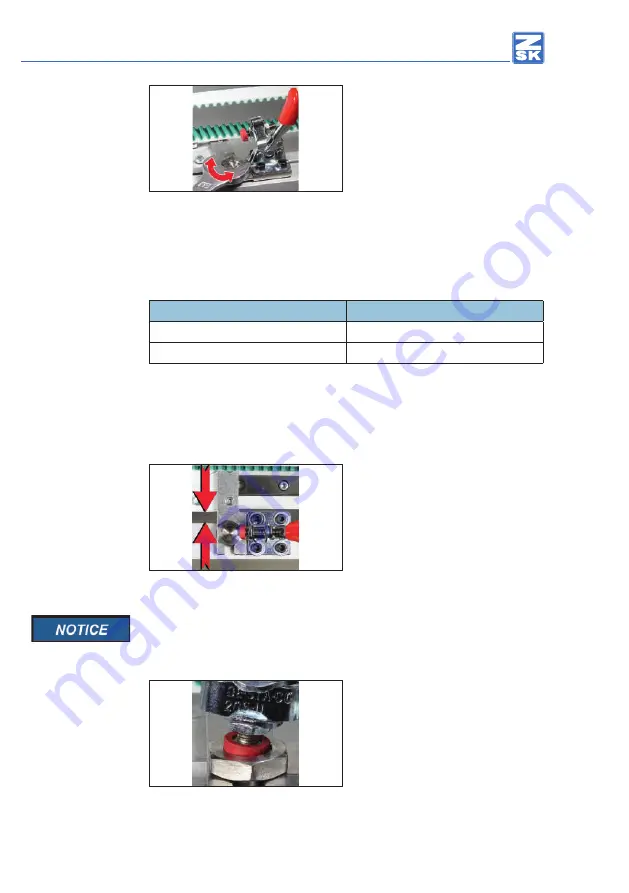
12
Quick change system for SPRINT Series
Using a suitable spanner set the
absorving energy of the system with
which the tubular frame has to be
pushed in the guides on the centring
devices.
Fig. 20: Centring device, force setting
Check the setting by moving back and forth the cylinder arm frame holder
Change and check the settings of the absorving energy until you find the
appropriate setting.
Centring device
Impact
Setting tighter
higher effort
Setting looser
smaller effort
The setting is right if the cylinder arm frame holder slides into both clevises
evenly under slight pressure.
Slide the cylinder arm frame holder
with the centring devices in the guides
of the two clevises.
Set a
parallel
distance of 6,0 mm
±0,3 between the carriages of the
pantograph drive and the cylinder arm
frame holder.
Fig. 21: Distance setting
To facilitate the setting of the 6 mm distance a correspondingly thick
gauge can be applied. This can be a metal strip, 2 screws or similar
material of the appropriate strength.
Place the clamping screws of the two
horizontal clamping fixtures centered
in the recording of centering devices.
Fig. 22: Clamping screw in the centring device
Содержание SPRINT Series
Страница 1: ...Quick change system SPRINT installation guide Made in Germany ZSK Stickmaschinen Made in Germany...
Страница 2: ......
Страница 22: ...22 Quick change system for SPRINT Series...
Страница 23: ...23 Quick change system for SPRINT Series...