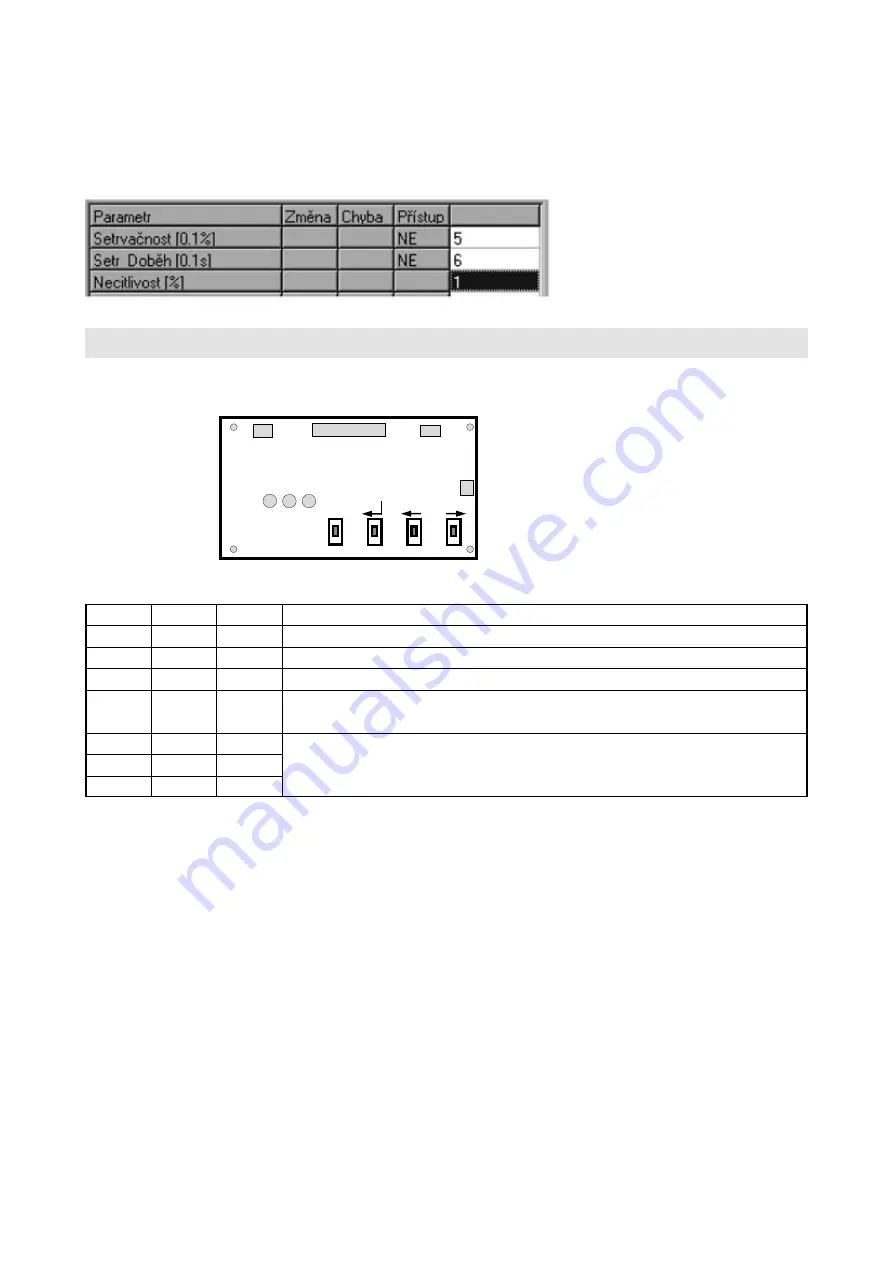
9
Setting program
The setting program is same for communication with the electronics DMS2ED and DMS2. The users' version
can be freely downloaded.
Note:
Inthewindow"Parameters“ofthesettingprogram,column"Access“,theword"NO“designatesparametersthat
cannotbechangedbytheuser(changeoftheseparametersisblocked).
PROCEDURE OF SETTING PARAMETERS BY MEANS OF PUSH-BUTTONS
For simple programming of required operating parameters, the control unit is fitted with four push-buttons:
MENU, P, O, C and three signal lamps.
Yellow
Red
Green
State
-
-
-
System without feeding
-
-
lit on
Everything OK - working regime (remote, local or switched-off control)
-
blinking
lit on
Error or warning – working regime (remote, local or switched-off control)
lit on
-
lit on
Input or output for setting parameters with push-buttons or setting
parameters by means of PC
blinking
-
lit on
blinking
blinking
lit on
Setting parameters with push-buttons
blinking
blinking
lit on
In adjustment, follow the paragraphs “VERIFICATION of APPARATUS FUNCTION And its LOCATION”, “fitting
on VALVE” and “ADJUSTMENT of ACTUATOR with VALVE” of these instructions.
For safety reasons, the system is delivered in the state of induced error of Calibration when the functions are
limited in order to reduce the risk of damage to the actuator by wrong wiring.
Record of position CLOSED, OPEN and AUTOCALIBRATION
– The actuator must be adjusted in such a way that the recorded position would switch off the actuator before it is
switched off by torque. For tight closure, the torque relay for torque Closed is only connected into the control circuit.
The actuator can be shifted either manually or electrically. The actuator in version CONTROL can be started from
menu MOTOR in program DMS2. In this case, the actuator does not react to the set position and can only be stopped
by the torque relay. In controlling from menu MOTOR, no torque may be induced. The torque must be left manually.
If, during adjustment, the torque is reached in the end-limit position, the torque must be left by means of a hand wheel.
– The actuator is set to position Closed and position Closed is stored by long pressing of push-button C
(withoutentering
theMenu).
– The actuator is set to position Open and position Open is stored by long pressing of push-button O.
– The calibration routine is started by means of push-button P
(inremotecontrol)
that, in the three-position regulation,
will measure actual inertial masses of the system and store them into the memory of the control unit. In the twoposition
regulation, pressing of push-button P only cancels the error of Calibration.
– In recording the end-limit positions, signalling relays and the position transducer are also set.
COM
POWER
TORK
AIN
LED1 LED2 LED3
MENU
P
O
C
Colours of diodes:
LED1 – yellow (menu number)
LED2 – red
(parameter value)
LED3 – green
Push-buttonsandsignallampsLEDoncontrolunitDMS2.ED.SandDMS2.ED.S90
Parametr – Parameter
Změna – Change
Chyba – Error
Přístup – Access
Setrvačnost (0,1 %) – Inertia [0.1 %]
Setr. Doběh (0,1 s) – Inertial run-out [0.1 s]
Necitlivost (%) – Insensitivity [%]
NE – NO