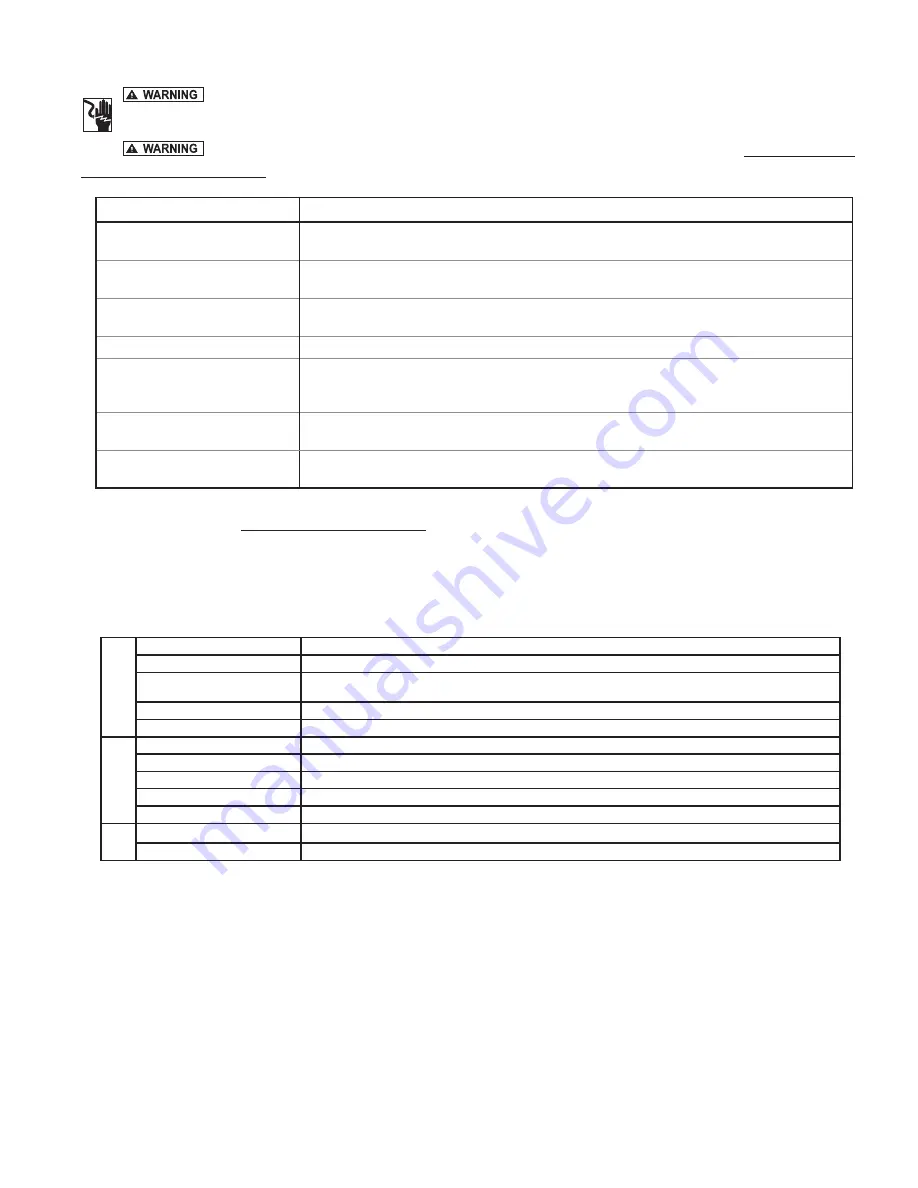
3
© Copyright 2020 Zoeller
®
Co. All rights reserved.
ELECTRICAL PRECAUTIONS-
Before servicing a pump, always shut off the main power breaker and then unplug the pump
- making sure you are wearing insulated protective sole shoes and not standing in water. Under flooded conditions, contact your local
electric company or a qualified licensed electrician for disconnecting electrical service prior to pump removal.
Submersible pumps contain oils which becomes pressurized and hot under operating condition.
Allow 2-1/2 hours after
disconnecting before attempting service.
If the above checklist does not uncover the problem, consult the factory - do not attempt to service or otherwise disassemble pump. Service must be performed by Zoeller
Authorized Service Centers. Go to www.zoellerpumps.com/service stations to find the Authorized Service Centers in your area.
SERVICE CHECKLIST
CONDITION
COMMON CAUSES
A. Pump will not start or run.
Check fuse, low voltage, overload open, open or incorrect wiring, open switch, impeller or seal bound mechanically.
Motor or wiring shorted. Float assembly held down. Switch, damaged or out of adjustment.
B. Motor overheats and trips
overload or blows fuse.
Incorrect voltage, negative head (discharge open lower than normal) impeller or seal bound mechanically, motor
shorted.
C. Pump starts and stops too
often.
Float switch tether length too short, check valve stuck open, or none installed in long distance line, overload open,
bidding, sump pit too small.
D. Pump will not shut off.
Debris under float assembly, float bound by basin sides or other, switch damaged or out of adjustment.
E. Pump operates but delivers
little or no water.
Check inlet, strainer housing, discharge pipe, and vent holes for obstructions. Discharge head exceeds pump
capacity. Low or incorrect voltage. Incoming water containing air or causing air to enter pumping chamber.
Incorrect motor rotation. (DC pump only)
F. Drop in head and/or capacity
after a period of use.
Increased pipe friction, clogged line or check valve. Abrasive material and adverse chemicals could possibly
deteriorate impeller and pump housing. Check line. Remove base and inspect.
G.
If tank or fittings leak.
Carefully tighten pipe joints (use pipe dope) and screws. Check gasket location, tighten lid evenly. Do not over
tighten fittings or screws.
This system is a backup to your primary sump pump. It is designed to provide flood prevention during power outages or primary pump failure. This
system is unique in that it has self-testing.
DESCRIPTION
Pump
Construction
Non-corrodible plastic, premium seals
Performance
35 GPM at 10' (113 LPM at 3 m) at 12.7 volts
Continuous Running Time with 100
AH battery
5 hours
Duty Cycle of 10%
2 days
Connection
9' (2.7 m) wire with 2 position connector
Controller
Construction
ABS plastic
Power Requirement
115 V 15 amp circuit
Consumption
Up to 3 amps at 115 V
Charger Output
7 amp multi-stage
Connections
8' (2.4 m) AC power cord, 6' (1.8 m) DC charging cable, connections for pump, operation switch, high water switch
Battery
Box
Construction
Non-corrodible plastic
Safety
Snap tight lid, keeps battery safe and clean