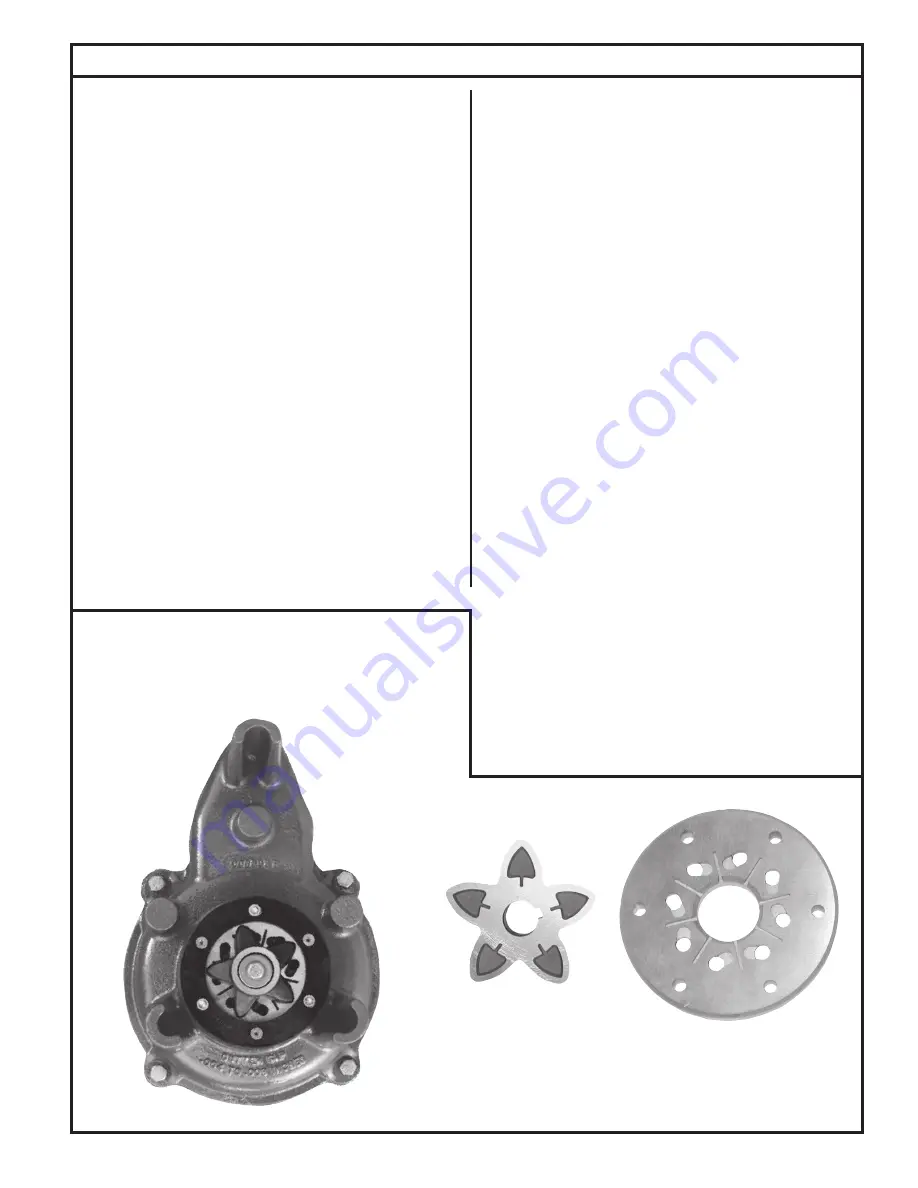
11
© Copyright 2021 Zoeller
®
Co. All rights reserved.
Cutter Maintenance
To remove star cutter: Remove guard ring then heat the center
bolt to 350 °F to loosen Loctite® thread sealant.
Grind the Star Cutter and Disc seen here to a 32 microfinish. Surfaces
must be flat to within 0.001” T.I.R. Gap must be between 0.004” and
0.008” on these parts.
1.
All power circuits must be disconnected and locked out before
any attempts are made at servicing.
The star cutter and disc can
be removed and sharpened by grinding the cutting faces. Both star
cutter and disc must be removed from the pump. Removal of these
parts can be accomplished in the field by removing pump from the
sump and positioning horizontally to access the intake of the pump.
If seals or other repairs are required, the pump must be totally
removed and serviced in a shop by a qualified pump technician or
authorized service center.
2. Remove the three countersunk screws on the plastic guard ring
and remove the ring.
3. Thoroughly clean the star cutter and disc assembly. Tilt pump
back to the vertical position to make certain the end play has
been removed. Check and record the clearance between the star
cutter and disc with a feeler gage. The correct running clearance
is between 0.004" and 0.008".
4. With pump in horizontal position, heat the hex head bolt in the center
of the star cutter with a propane torch. The bolt must be heated to
350 °F to soften the thread lock sealer on the bolt for ease of removal.
Remove the bolt by turning in a counterclockwise rotation. It will
be necessary to use a wood block to prevent the star cutter from
turning while removing the bolt. Pull star cutter from the shaft and
remove the spacer shims located behind the star cutter.
5. Remove the three cap screws holding the disc and remove disc
from the pump.
6. The disc and star cutter can be replaced with new service parts or
resurfaced by grinding. Resurfacing is accomplished by surface
grinding both disc and star cutter to a 32 micro finish. Do not
attempt grinding in the field. Send parts to a qualified machine
shop for repair. The disc, star cutter and shims are a matched set.
Keep parts together. Measure disc before and after resurfacing
with micrometer and record measurements.
7. After resurfacing, the disc and star cutter must be flat within 0.001".
If the disc has been surface ground, it will be necessary to remove
shims to compensate for the material removed from the disc. As a
starting point, remove shims of the same thickness as the amount
machined from the cutter disc (step 6 above). Final running clearance
must be between 0.004” and 0.008”. Be sure pump is in vertical
position and all end play has been removed before measuring.
8. Clean bottom of pump where disc is located and replace disc and
retainer screws. Torque to 63-67 in-lbs. Replace star cutter with
the correct shims. Install washer and torque hex head bolt to
71-75 in.-lbs. apply Loctite 262 thread-lock sealant or equal to bolt
threads prior to insertion. Check running clearance with pump in
vertical position to remove end play. Clearance must be between
0.004" and 0.008" to obtain efficient grinding when pump is put back
in service.
9. Replace plastic guard ring and its three screws.
10. Check the oil in the motor housing before reinstalling. Contact the
factory if the oil has a milky appearance or burnt smell. The level
should be even with the fill plug when pump is in the upright position.
Add oil if required. Use insulating oil supplied by the factory.
FIGURE 7.
(Model 7011 components shown)