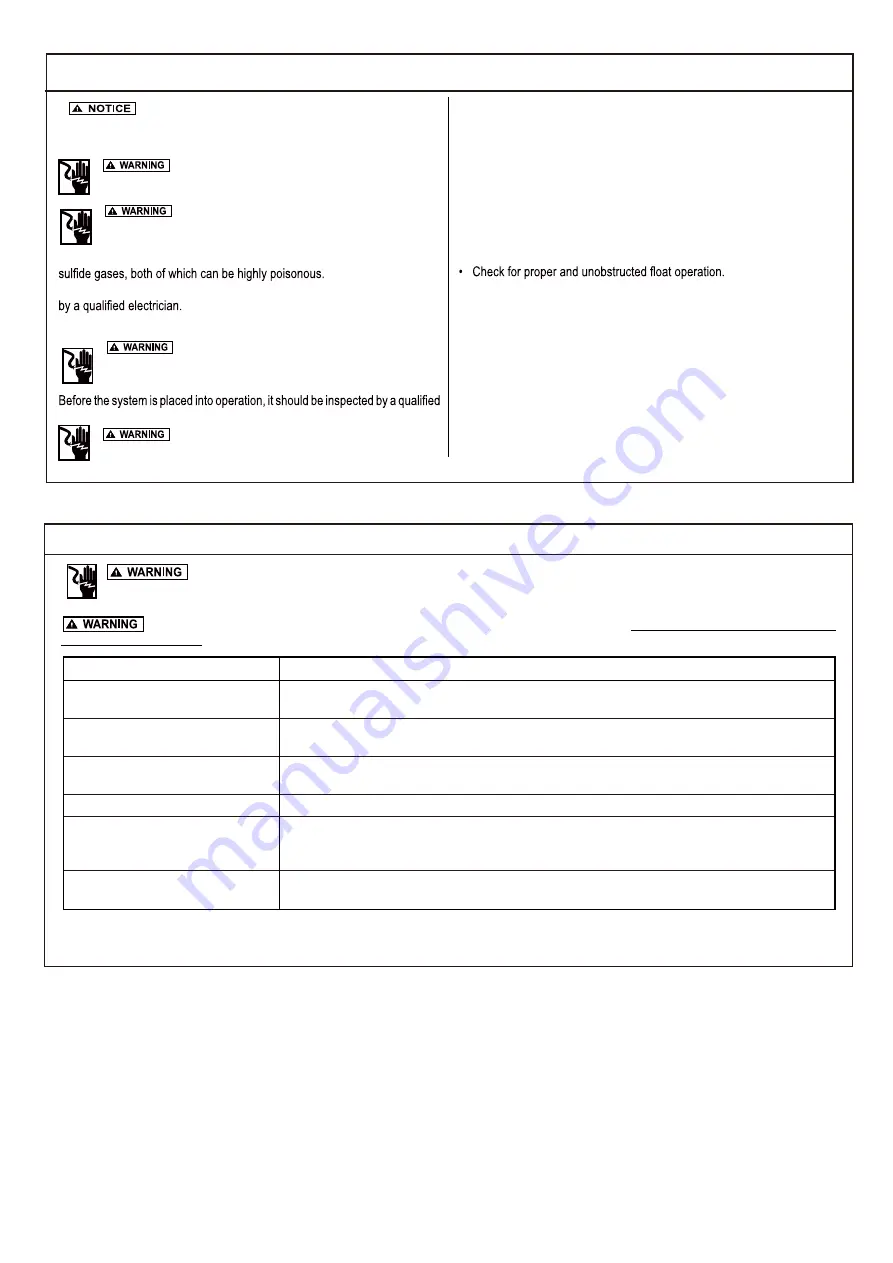
- 3 -
© Copyright 2018 Zoeller Co. All rights reserved.
®
Allow 2-1/2 hours after disconnecting
If the above checklist does not reveal the problem, consult the factory. Do not attempt to service or otherwise disassemble pump. Service
must be performed by an authorized Zoeller Company representative.
CONDITION
COMMON CAUSES
A. Pump will not start or run.
Check fuse, low voltage, overload open, open or incorrect wiring, open switch, impeller or seal bound mechanically, motor
or wiring shorted. Float assembly held down. Switch damaged or out of adjustment.
B. Motor overheats and trips overload
or blows fuse.
Incorrect voltage, negative head (discharge open lower than normal) impeller or seal bound mechanically, motor shorted.
C. Pump starts and stops too often.
Float switch tether length too short, check valve stuck open, or none installed in long distance line, overload open, bidding,
sump pit too small.
D. Pump will not shut off.
E. Pump operates but delivers little or
no water.
Check inlet, strainer housing, discharge pipe, and vent holes for obstructions. Discharge head exceeds pump capacity.
Low or incorrect voltage. Incoming water containing air or causing air to enter pumping chamber. Incorrect motor rotation.
(3 phase pumps only.)
F. Drop in head and/or capacity after
a period of use.
Increased pipe friction, clogged line or check valve. Abrasive material and adverse chemicals could possibly deteriorate
impeller and pump housing. Check line. Remove base and inspect.
Debris under float assembly, float or float rod bound by pit sides or other, switch defective, damaged or out of adjustment.
SERVICE CHECKLIST
ELECTRICAL PRECAUTIONS-
Before servicing a pump, always shut off the main power breaker and then unplug the pump. “Make
Submersible pumps contain oils which become pressurized and hot under operating conditions.
sure you are wearing insulated protective sole shoes and not standing in water.” Under flooded conditions, contact your local electric company or
a qualified licensed electrician for disconnecting electrical service to the pump prior to removal.
before attempting service.
General Maintenance
Repair and service should be performed by a Zoeller Pump
Company Authorized Service Station only.
SAFETY PROCEDURES
For your protection, always disconnect pump and
panel from its power source before handling.
Never enter the basin until it has been properly vented
and tested. Any person entering a basin should be wearing a harness
with safety rope extending to the surface so that they can be pulled out
in case of asphyxiation. Sewage water gives off methane and hydrogen
Installation and checking of electrical circuits and hardware should be performed
Pump is never to be lifted by power cord.
Unit must be cleaned and disinfected, inside the
pumping chamber and all exterior surfaces, prior to servicing.
GENERAL SYSTEM INSPECTION
technician.
Wiring and grounding must be in accordance with the
National Electrical Code and all applicable local codes and ordinances.
LUBRICATION PROCEDURES
No lubrication is required.
If pumps are to be stored for more than six months, refer to short-term storage
procedure in the Operation section.
PREVENTIVE MAINTENANCE
Preventive maintenance is recommended to ensure a long service life from the
product. Provided is a suggested maintenance schedule.
Every six months:
• Inspect and test system for proper operation.
• Listen for proper check valve operation.
Every 5 years or 10,000 hours of operation:
• Remove pump, inspect and service using a Zoeller rebuild kit.
• Flush and clean basin.
DOUBLE SEAL PUMPS
Double seal pumps offer extra protection when these pumps are supplied with
optional moisture sensors, check the control panel's seal failure light for a
warning. Whenever the seal leak light is activated, it's indicating that moisture
is present, and the pump should be removed and serviced in order to avoid
damage to the motor.