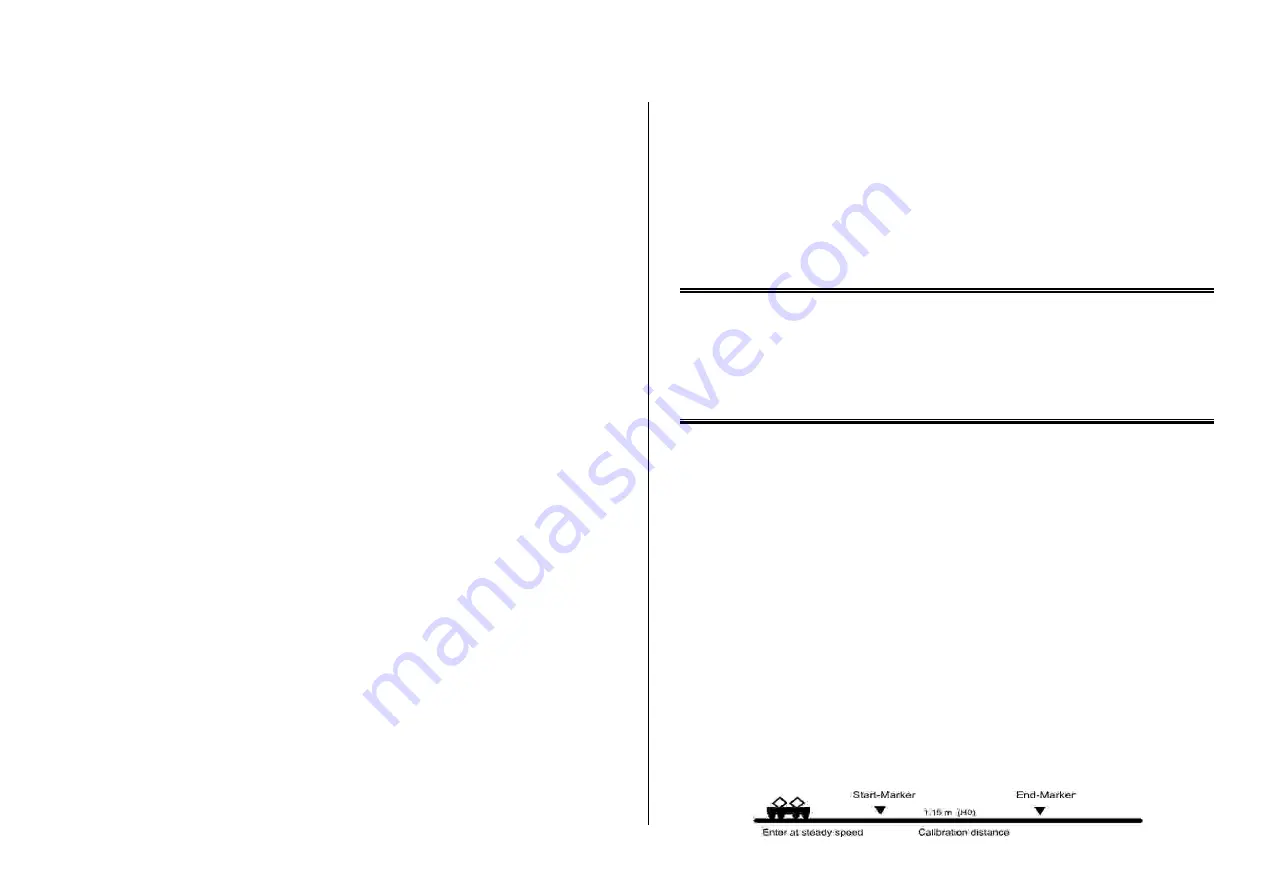
H0 Sound Decoder MX640 Page 17
If an engine with an
older motor design
runs rough at low speeds, the sample frequency (tens
digit in CV #9) is usually the one that needs to be set to a larger value (>5), which often requires the
sample time (ones digit) to be set to a higher value as well (>5); i.e. CV #9 = 88.
*
If, after setting CV #9, the engine still doesn’t run smoothly enough at the lowest speed step,
changing the values of the ones and tens digit in CV #56 will often improve it. Here also, the default
value of “0” is equal to the center setting of 55. The tens and ones values define the proportional
and integral portion of the PID control. By default (CV #56 = 0), the proportional value adjusts itself
automatically and the integral value is set to mid-value. Depending on the type of motor, other val-
ues than the default value can be used to combat rough running, such as 77, 88 or 99 for older
locos that run rough or 33, 22, or 11 for newer locos with more efficient motors (Faulhaber,
MAXXON etc).
A possible overcompensation can be reduced with the help of the integral value (ones digit of CV
#56).
For engines with
Maxxon, Faulhaber
(coreless motors) the setting
CV #56 = 100
should be tried
first (instead of the default “0” for normal DC motors). This setting is equal to CV #56 = 155, where
the hundreds digit “1” is an adjustment to the center setting for highly efficient motors. If necessary,
further improvements may be achieved by different values of the tens and ones digit.
*
After improving low speed performance (by increasing the value of CV #56 described above),
check that the engine is not running jerkily at mid-speed level that could be caused by high CV #56
values (77, 88…). This effect can be compensated for by reducing the total amount of load com-
pensation in
CV #58
(default “250”) down to “200” or “150” or use CV #10 and #113 to cut the load
compensation at a speed just below the start of the jerky motion (the compensation is reduced to
the level defined with CV #113 at the speed step defined with CV #10).
*
If after the above adjustments the engine’s speed is still fluctuating, use
CV #57
for further fine-
tuning. With a default value of 0, load compensation is based on the measured track voltage. If this
voltage fluctuates, the speed will also fluctuate. The cause is usually a DCC system that can’t com-
pensate for voltage drops (other than Zimo systems) or dirty wheels or track. To prevent such fluc-
tuations a value representing the selected track voltage x10 is entered to CV #57 (not idle track
voltage, rather voltage under load). For example, if an engine needs 14 V (measured under load) a
value of 140 should be entered. Sometimes it’s even better to keep this value about 20% to 50%
lower to compensate for a slight internal voltage drop in the decoder.
*
Next, we check to see whether the loco’s initial start is smooth or abrupt. This can be seen well
with some momentum added. Temporarily, set some momentum with CV #3 and #4. Start with a
value of 5.
There are basically two different kinds of start up jolts: the jolt that happens every time an engine
starts up and the one that only shows up after the engine changes direction (i.e. after the engine
stopped, changed direction and starts up again). The “direction-change jolt” is due to gearbox back-
lash; see further down.
The adaptive acceleration procedure can now be used to eliminate abrupt starts by changing the
value in
CV #123.
Start with a value of 20. The lower the value, the stronger the effect will be (e.g.
10 results in the strongest effect for acceleration, 90 the weakest).
A possible jolt when stopping can also be reduced with the help of the ones digit. The tens digit is
for defining the adaptive acceleration and the ones digit for the adaptive deceleration. CV #123 = 22
improves the start-up as well as the stop jolt. It may be of advantage to reduce the adaptive decel-
eration, i.e. CV #123 = 24 in order to improve repeatable stop points in automated operations
(routes, block control etc.).
Beginning with software version 5 a start-up jolt during a change in direction can also be eliminated
with CV #146. Typical values for CV #146 are 50 or 100 (See description in the CV table).
*
After changing the values in CV #123 the basic momentum may need to be readjusted to your
preferences; first with
CV’s #3 and #4
(basic momentum). Usually higher than default values
should be used, at least CV #3 = 5 and CV #4 = 3. This improves the engine’s performance consid-
erably. Much higher values are suitable for engines equipped with sound in order to match the
sound to the engine’s movement (with sound decoders as well as external sound modules via
SUSI).
*
Additionally the “exponential acceleration and deceleration” may be applied with
CV #121
and
#122.
This allows for prototypical non-linear momentum coupled with extremely soft starts and
stops without compromising the maneuverability in the upper speed range. This stretches the time
the locomotive will spend in the lower speed range. Often used values for these CV’s are between
25 and 55, which means that 20% to 50% (according to the tens digit) of the total speed range will
be included in the exponential acceleration curve, with a medium curvature (ones digit at ‘5’).
Notes on acceleration behavior versus speed steps:
An acceleration or deceleration sequence according to CV #3 and 4 that is the timely succession of speed steps is
always based on the internal 252 steps which are spaced identical from 0 to full speed. Neither speed table (three
steps or individual speed table) has any effect on the acceleration or deceleration behavior. The speed tables only
define the target speed for a particular speed dialed-in by the cab.
This means that the acceleration or deceleration behavior cannot be improved by a bent speed curve as defined
by CV #2, #5, #6 or the individual speed table CV’s #67 - 94. The exception to this could only be a cab or com-
puter controlled acceleration or deceleration event. A desired curve in a decoder controlled acceleration or decel-
eration event however is possible with the “exponential acceleration/deceleration” using CV #121 and #122..
-
If applicable see section “Settings for the signal controlled speed influence“!
-
If applicable see section “Setting for stopping with ...“!
-
If applicable see section “Distance controlled stopping” (constant stopping distance)!
Km/h – Speed regulation -
CALIBRATION and operation
The km/h speed regulation is a new, alternative method of
driving with prototypical speeds
in all
operating situations: the cab’s speed steps (1 to 126 in the so-called “128 speed step mode”) will be
directly interpreted as km/h. Preferably, all engines of a layout should be set to the same method.
Engines equipped with non-ZIMO decoders can be set up similarly through the programmable
speed table (although with more effort and less precise because there is no readjustment taking
place by the decoder).
The ZIMO readjustment:
the decoder is not limited to converting the speed steps to a km/h scale
but rather ensures that the desired speed is held, by recalculating the already traveled distance and
automatically readjusts itself.
A CALIBRATION RUN; should be performed with each loco:
First, we need to determine the
calibration track:
a section of track that measures 100 scale me-
ters (plus the necessary length before and after, for acceleration and deceleration), of course with-
out inclines, tight radii and other obstacles; for example, for HO (1:87) 115cm; for G-scale (1:22.5)
4.5m. Start and end points of the calibration distance need to be marked.