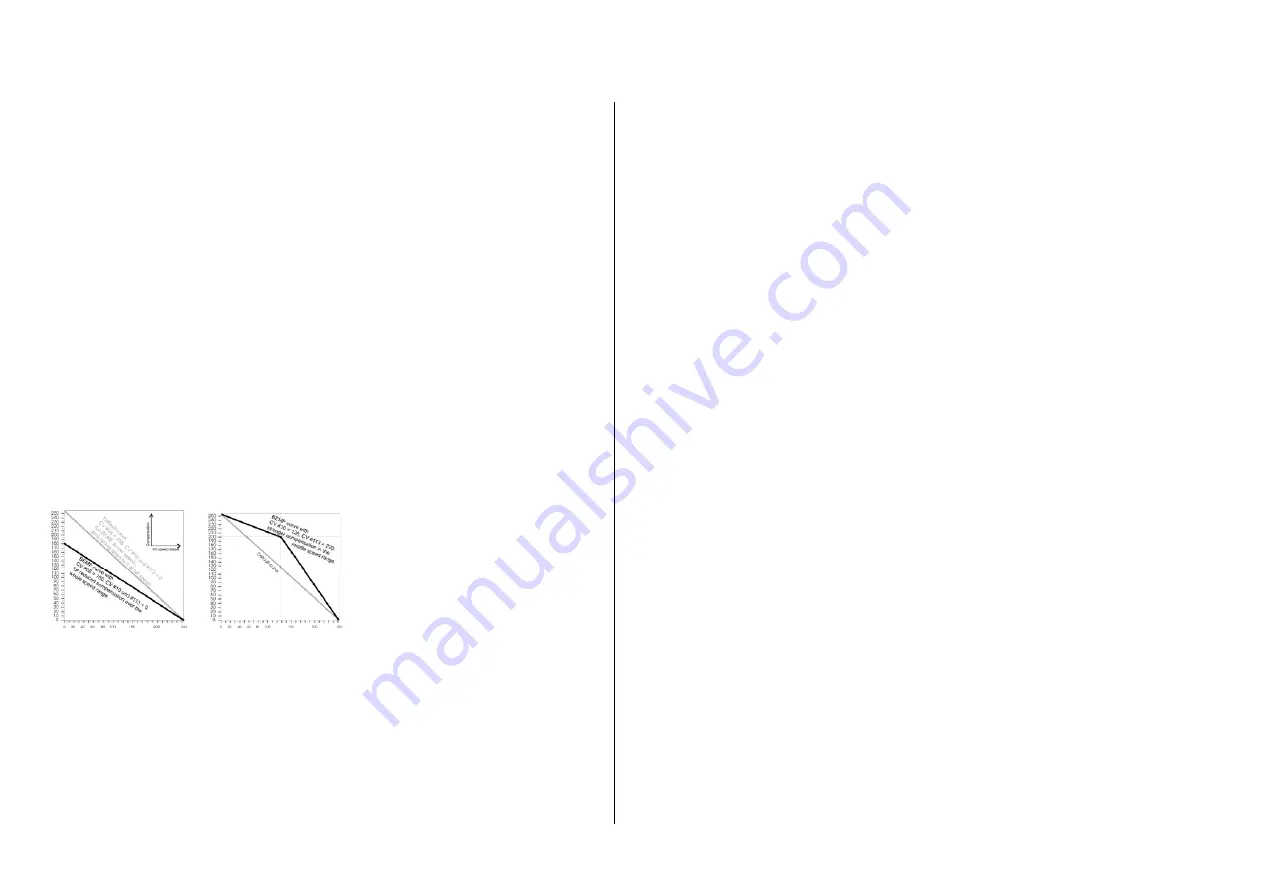
Page 16 H0 Sound Decoder MX640
The "absolute reference" is to be preferred to the "relative reference" when using other vendors'
systems (particularly those that don’t keep the track voltage stabilized)!
Relative Reference:
The speed range is automatically adjusted to the available track voltage, if a 0
is entered to CV #57 (default). Therefore, the higher this voltage is set at the command station (ad-
justable between 12V and 24V) the faster the train will be over its entire speed range.
The relative reference is suitable as long as a constant voltage is present (which is the case with all
Zimo systems but not all competitor systems) and the resistance along the track is kept to a mini-
mum.
The driving characteristic of an engine can further be optimized by adjusting the
intensity of load
compensation with CV #58.
The goal of load compensation, at least in theory, is to keep the
speed constant in all circumstances (only limited by available power). In reality though, a certain re-
duction in compensation is quite often preferred.
100% load compensation is useful within the low speed range to successfully prevent engines from
stalling or picking up speed under load. BEMF should rather be reduced as speed increases, so
that at full speed the motor receives full power with little BEMF. A slight grade dependent speed
change is often considered more prototypical. Consists also should never be operated with 100%
BEMF because it causes the locomotives to fight each other by compensating too hard and too fast,
which could lead to derailments.
The degree of load compensation can be defined
with
Configuration Variable #58
from no com-
pensation (value 0) to full compensation (value 255). This, in effect, is the amount of compensation
applied to the lowest speed step. Typical and proven values are in the range of 100 to 200.
If an even more precise load compensation is required (though hardly ever necessary),
configura-
tion variable #10 and #113
presents a solution. CV #10 defines a speed step at which the
load
compensation is reduced to the level defined in CV #113.
Both CV’s have to have a value other
than 0. If either CV #10 or #113 is set to 0, BEMF is again solely based on CV #58.
Regarding
configurations variable #56
–
also see CV table and the following chapter on
“Step by step…..”)!
Acceleration and deceleration characteristics (momentum)
:
Configuration Variables #3 and #4
provide a way of setting a
basic linear acceleration and de-
celeration rate
according to NMRA rules and regulations. That is, the speed is changed in equal
time intervals from one speed step to the next.
To simply achieve smooth transitions during speed changes, a value between 1 and 3 is recom-
mended. The true slow starts and stops begin with a value of about 5. Programming a value higher
than 30 is seldom practical!
The momentum can be modified with
Configuration Variables #121 and #122
to an
exponential
acceleration and deceleration
rate, independent from each other. This in effect expands the mo-
mentum in the lower speed range. The area of this expansion (percentage of speed range) and its
curvature can be defined.
A typical and practical value is “25” (as starting point for further trials).
The
adaptive acceleration and deceleration
procedure
defined by
configuration variable #123
will not allow a change in speed until the previous target speed step of an acceleration/deceleration
event is nearly reached.
Most often applied values are “22 or “11”, which can noticeably reduce a start-up jolt (the effect in-
creases with smaller figures).
Step by step CV adjustment procedure to optimize engine
performance:
It is recommended to systematically program a decoder since setting the CV’s for load compensa-
tion and momentum can result in a certain interaction with each other:
*
To begin, select the highest possible number of
speed steps
the system can operate in, that
would be
128
for Zimo (selected at the cab for the decoder address in question). All Zimo decoders
are set by default to 28/128 speed steps (both variants will be evaluated). If used with systems that
are restricted to 14 steps, set Bit 1 in CV #29 to 0.
*
Next set the engine to the lowest step, recognizable on the Zimo cab’s when the bottom LED next
to the speed slider changes color from red to green and/or the speed step 1 is displayed on the
screen of the MX21/MX31 cabs (first, change the cab to 128 speed steps for this address, if not
done so or if it isn’t already the default setting!).
If the engine now at the lowest speed step is running to slow or not at all, increase the value in CV
#2 (default 2), if it runs too fast decrease the value. If the individual speed table is used (CV #67 -
94, active if bit 4 of CV #29 is set), set the lowest speed step with CV #67 instead and adjust the
rest of the speed table CV’s accordingly.
*
The EMF sampling process (see previous page) is critical for smooth even low speed behavior
and quiet motor performance which can be modified with CV #9 (but also with CV #56!). This CV is
also used to set the decoder to low frequency motor control, which is used only rarely with older AC
motors.
By default, CV #9 is set to high frequency at 20 kHz (can be raised to 40 kHz with Bit 5 of CV #112)
and automatically adapts the EMF sample rate to the loco speed. If drivability is not flawless or too
much motor noise is audible, fine-tuning is possible:
CV #9 = 0 (default setting) has the same effect as CV #9 = 55, which is a mean value for the ones
as well as the tens digit. The value of the tens digit in CV #9 determines the EMF sampling rate and
the value of the ones digit the EMF sampling time, which is the time the motor is not powered.
In general: High-efficient motors such as
Faulhaber, Maxxon, Escap
etc (coreless motors) can
manage with short measuring times; the ones digit in CV #9 can therefore be set to a small value
such as “2”. The ideal EMF sampling rate depends on the locomotive type and weight: small light-
weight engines require a rather high setting, i.e. “5”, while heavy engines such as O-gauge or large
HO engines a rather small value, i.e. “2”. Thus for a typical HO engine with a coreless motor the
setting of
CV #9 = 52
is usually good; for O-gauge engines:
CV #9 = 22
. Further improvements in
terms of smooth low speed performance and reduced motor noise may be achieved by trial and er-
ror using different tens digit values in CV #9; and of course by means of CV #56 (see below).