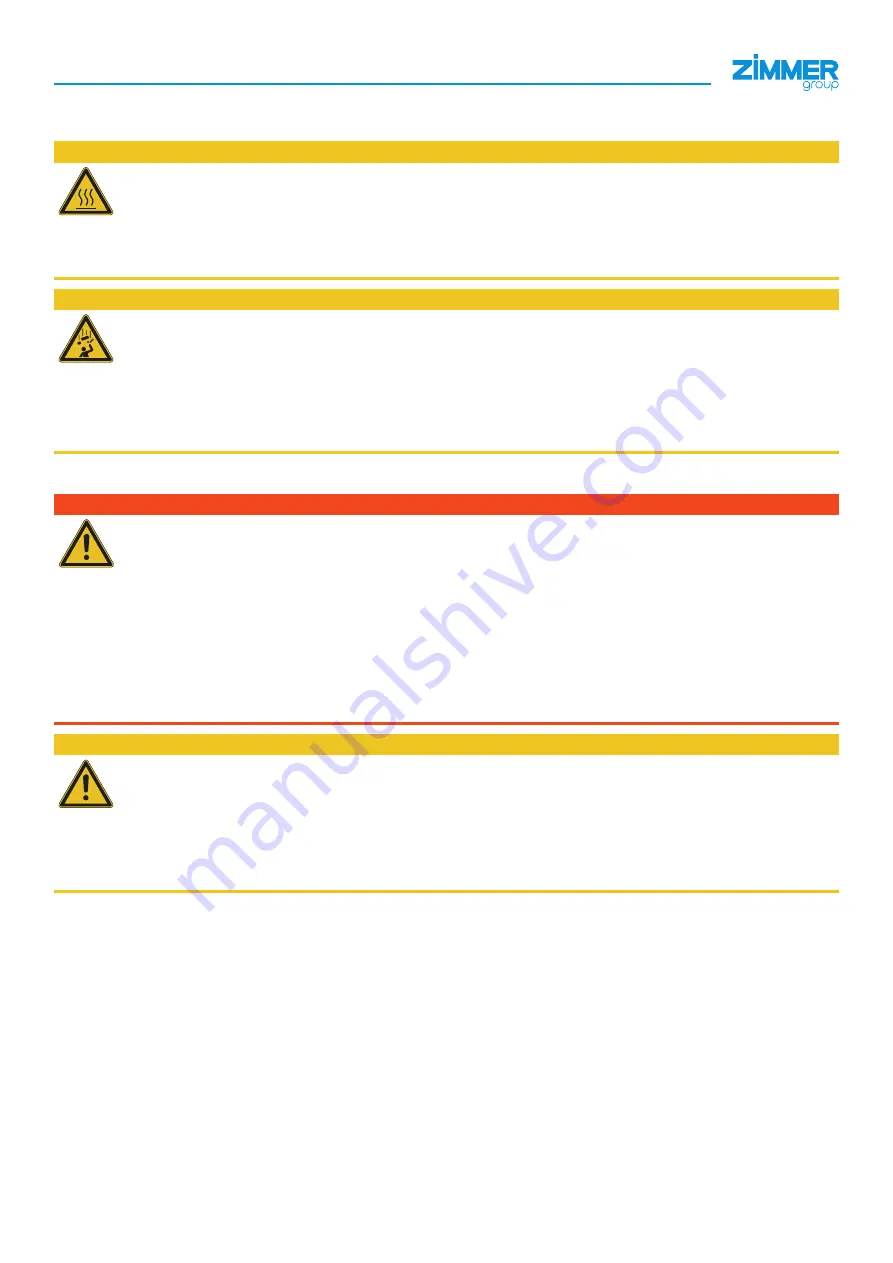
17
11 Commissioning
CAUTION
Risk of burns from hot surfaces
During operation and commissioning, the surfaces of the product may become hot.
►
Keep temperature-sensitive parts away from hot surfaces.
►
Do not install any temperature-sensitive parts to a product with hot surfaces.
►
Only touch the product while wearing appropriate personal protective equipment.
CAUTION
Risk of injury caused by falling parts
Operating pressure that is too high or short-term pressure peaks over the maximum permitted operating pressure
can lead to a fault or the destruction of the product.
The holding torque can decrease.
►
Maintain the maximum permitted operating pressure.
►
Use a pressure relief valve.
11.1 Checking operational readiness
WARNING
Risk of injury due to uncontrolled movements
An emergency stop of the complete machine and the accompanying emergency braking of the product can lead
to a decrease of the holding torque. The malfunction resulting from this can lead to injuries.
►
After an emergency stop, check the operational readiness of the product.
►
Depressurize the product.
►
Initiate a torque that corresponds to the maximum holding torque of the product.
►
Make sure that the shaft does not warp in this status.
Ö
The clamping surfaces of the product are worn if it is discovered that the shaft is warped.
►
Do not put the product into operation again until the operational readiness has been checked successfully.
CAUTION
Risk of injury due to uncontrolled movements
Contact with lubricants can lead to a decrease in the holding torque. The malfunctions resulting from this can
lead to injuries.
►
Check the product regularly for lubricants in the clamping area.
►
Clean the clamping area if the product comes into contact with lubricants.
►
Check the operational readiness of the product if the product comes into contact with lubricants.
►
Check all mounting screws for the prescribed tightening torque.
►
Check all connections for leaks.
►
Check the clamping process by attempting to move the product when power is connected.
►
Check that the product moves easily in a deenergized state by moving it manually.
INSTALLATION AND OPERATING INSTRUCTIONS:
DKPS1000
DDOC01621 / a
EN / 2022-10-04
Zimmer GmbH • Im Salmenkopf 5 •
77866 Rheinau, Germany •
+49 7844 9138 0 • www.zimmer-group.com
Содержание DKPS1000 Series
Страница 2: ......