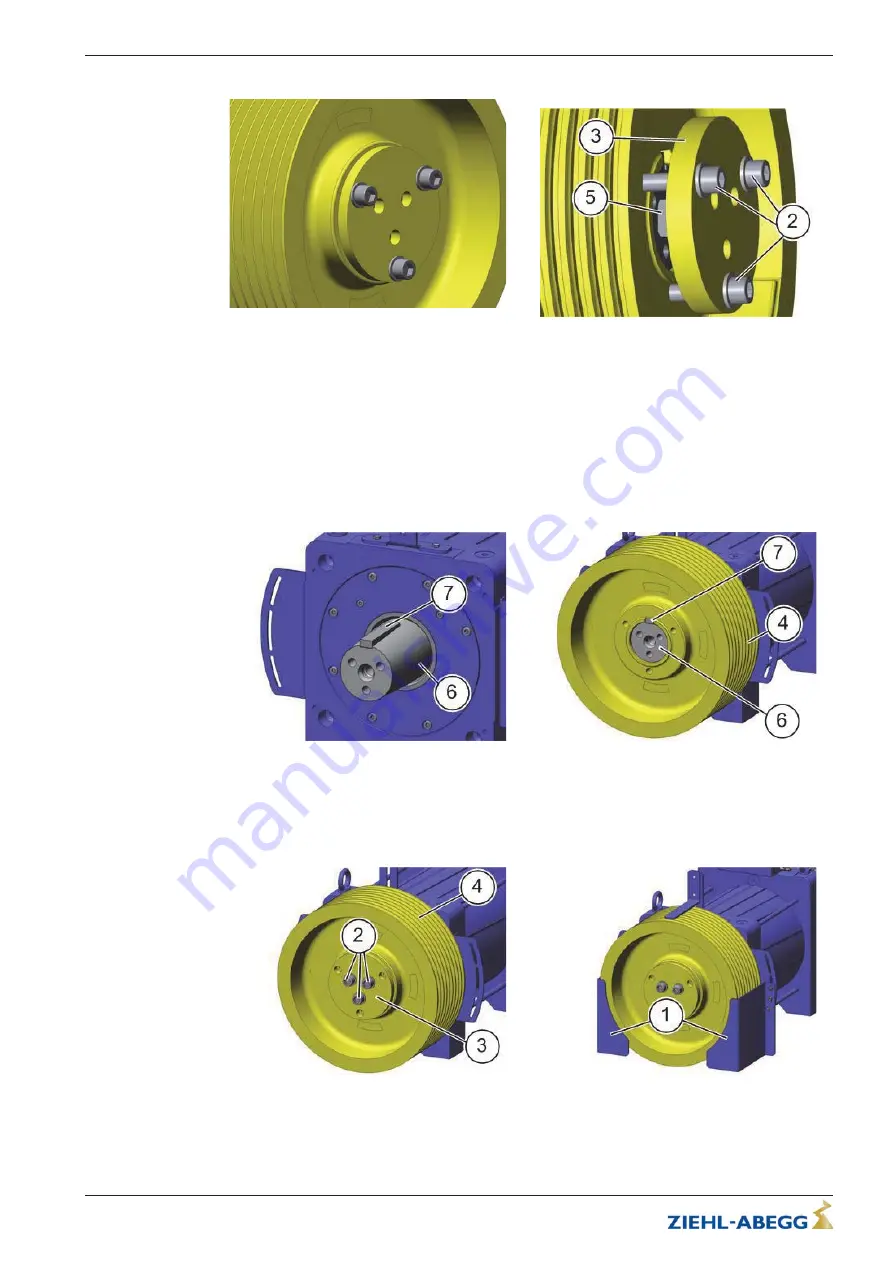
3. Turn the front plate (3) to press off.
4. 5 - 8 mm spacer or hexagon nut (5) must be placed between shaft end and front plate (3).
5. Screw4front plate( ) to the traction sheave (4) at the outer circle of holes using hex socket screws
M16 x 50 (2).
6. Tighten the screws M16 x 50 (2) uniformly with an allen wrench SW 14 By tightening the screws
the tractions sheave (4) will be pulled from the drive shaft.
8.3.3.3
Mounting the traction sheave
The mounting kit (article 70029992) can be used to mounting the traction sheave. This is optionally
available.
1. Clean the traction sheave (4) and drive shaft (6) with a micro-active cloth and quick cleaner. Both
parts must be free of dirt, grease and rust.
2. The parallel key (7) has to be available.
3. Put traction sheave (4) on drive shaft (6). The bores for screws M16 must point outwards.
Observe the position of the groove for the parallel key.
4. Screw the front plate (3) onto the drive shaft (6) at the inner hole circle using the three hex socket
screws M16 x 50 (2). Apply screw threadockerLoctite 243 or a similar product to the
fi
screws.
Do not forget spring washers!
Translation of the original operating instructions
ZAtop
–
model series SM210.60B/SM210.70B
Service and maintenance
$7%$B*%
,QGH[
Part.-No. 01013389-GB (EU-BD 1014)
39/88