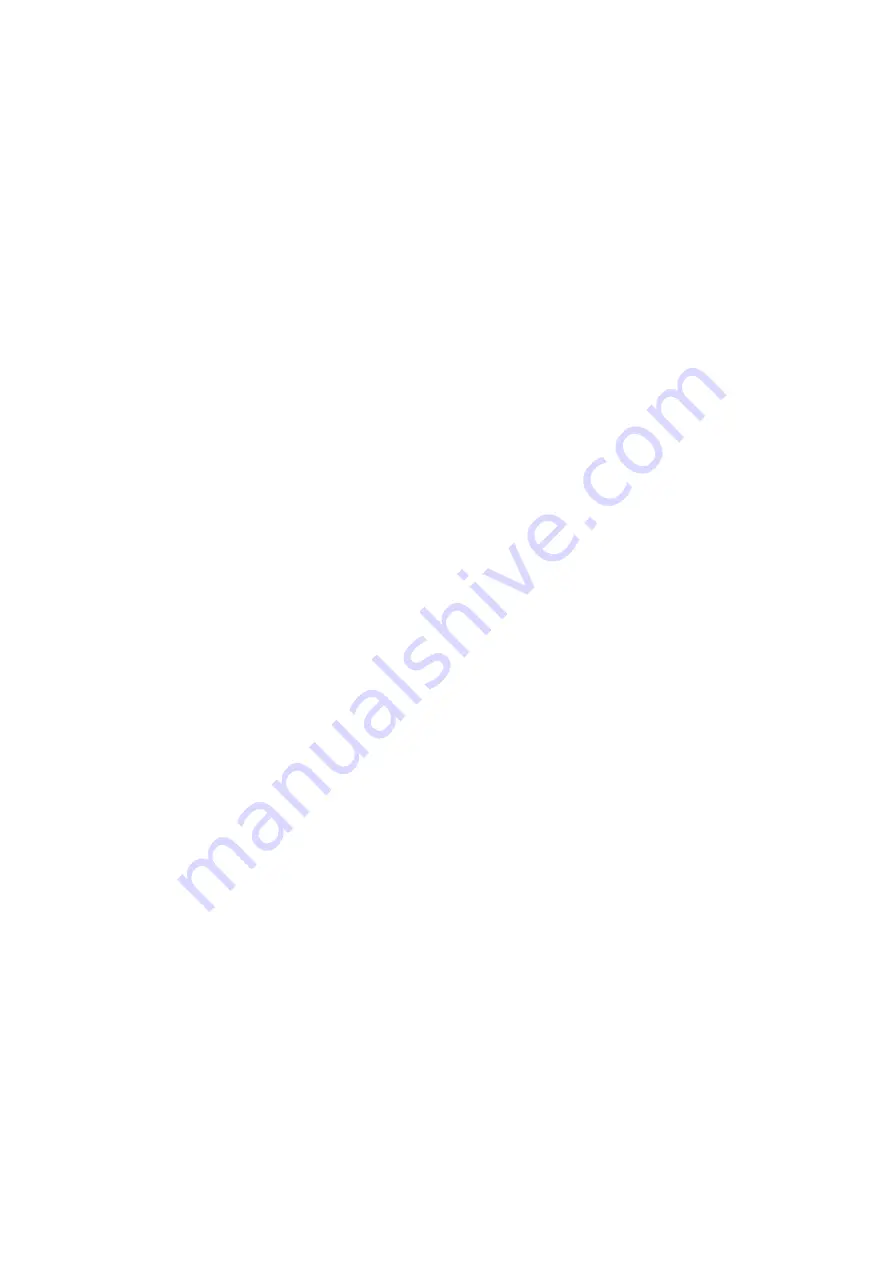
18
G00 X_ Y_ Z_;
G00: G code (group 01) for positioning (rapid traverse)
X_Y_Z_
:
Dimension word for the end point
Explanations
:
A rapid traverse rate is set for each axis by parameter 0904-0906, so no rapid traverse feedrate need be
programmed.
The following overrides can be applied to a rapid traverse rate with the switch on the machine operator’s
panel: F0, 25, 50, 100%.
F0: Allows a fixed feedrate to be set for each axis by parameter 0966-0968.
5.2 Cutting Feed
Feedrate of linear interpolation (G01), circular interpolation (G02, G03),etc. are commanded with numbers
after the F code. F is a modal value, namely the original value remains valid before a new F is given. In cutting
feed, the next block is executed so that the feedrate change from the previous block is minimized. The maximum
value of F is controlled by the user parameters, The maximum allowed feed rate of each axis set by
the
parameter 0895-0897.Cutting feed rate can also be controlled by the feed override switch on the operator panel,
the actual cutting feedrate should be given by the override product of F and override switch.
Two modes of specification are available:
1.
Feed per minute (G94): After F, specify the amount of feed of the tool per minute.
2.
Feed per revolution (G95): After F, specify the amount of feed of the tool per spindle revolution.
5.3 Automatic Deceleration Control
Automatic deceleration control acting on the start and stop process of each axis movement, in order to reduce
the impact and make a smooth starting and stopping process. For the same purpose, automatic deceleration control
also acts on the process of the feed rate transformation. For different feeding modes, NC system uses different
acceleration and deceleration control modes:
Rapid positioning feed: use linear acceleration and deceleration control, acceleration and deceleration time
constant of each axis is controlled by the machine parameters.
Cutting feed: acceleration and deceleration control with exponent, acceleration and deceleration time
constant controlled by the machine parameters.
Manual feed: acceleration and deceleration control with exponent, acceleration and deceleration time
constant of each axis is controlled by the machine parameters0942-0944.controlled by parameters1020-1022 in
hand wheel mode.
6 Tool Function (T Function)
Machine tool library can select tool in any way, namely specifies the tool number by two T code T ××,
without considering which pocket the knife in. T address ranges can be any integer from 1 to 99.Before M06 must
have a T code, if the T command and M06 appear in the same block, then the T code should be written before the
M06.
NOTE:
Be sure to set the correct tool table, if not match with the actual situation, it will seriously damage the
machine and cause unpredictable consequences.
7 Reference Point
7.1 Reference Point
When Machining Center changing tool often makes Z axis as the machine reference point. Machine
reference point is a fixed point on the machine, regardless of the machining program. Usually, the machine