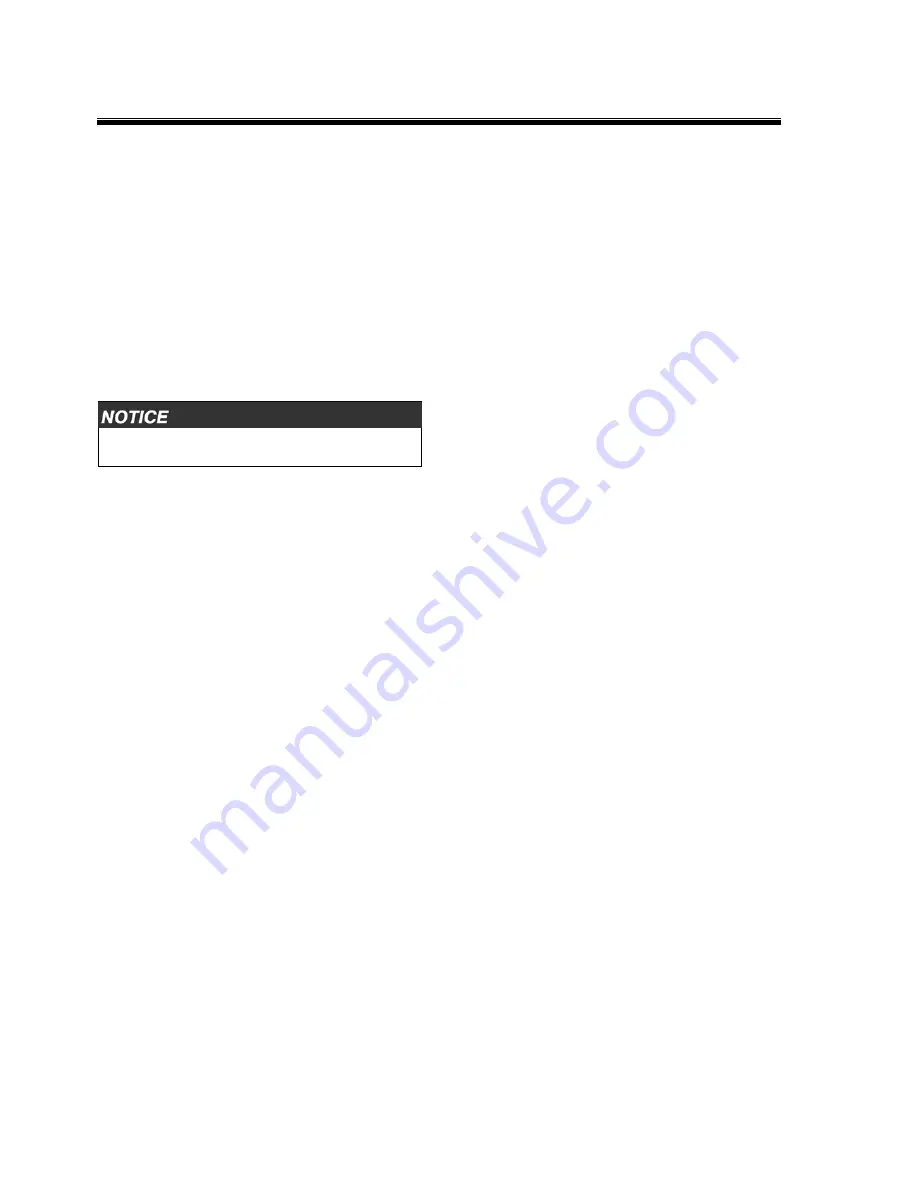
Initial Installation
24
EN 4161.758.101m – 2018-09
4.4
Output
4.4.1
Version with belt output
The belt pulley must be centered on the outer
diameter of the output flange (tolerance K6),
fastened with the bolts so that it is frictionally
engaged and secured. Comply with the specified
tightening torques.
The belt pulley is to be balanced to quality 6.3 as
per VDI Directive 2060 in order to ensure low-
vibration operation.
Possible damage due to bearing overload.
Note maximum tensioning strength of belts.
Note the maximum specified tensioning force
when tightening the belts in order to prevent
bearing overload.
The average belt force must be between the
bearings. When assembling, it must be possible to
easily slide the belt pulley onto the output shaft.
Heat the belt pulley if necessary.
4.4.2
Version with coaxial output
In the case of the version with coaxial output
(shaft stub), also note the balancing type for the
output (see chap. 4.2). The gearbox is delivered
with full-key balancing.
Refer to the installation drawing for the fitted key
dimensions. Always fix the fitted key in place using
a threaded pin.
4.4.3
Version with TSC
The version with TSC (Through Spindle Coolant) is
used for carrying cooling lubricant, hydraulic oils or
air/oil mixtures
1)
through the gearbox to the
spindle. A rotary transmission lead through is
necessary to ensure that the fluid can be conveyed
in a ratio operating at differential speed. This lead
through is subject to wear depending on the load
and the status of the medium. System conditions
can cause leakage drips to occur when switching
on and off and the relative design measures must
be implemented in the coolant circuit to retrieve
them. A transparent coolant return enables an
evaluation using the status of the rotary feed.
The warranty for the rotary transmission lead is
limited to 12 months.
Information about the product, function, operation
and installation of the rotary transmission lead
through can be found in the operating instructions
4161.758.030 (German)
4161.758.130 (English)
1)
No abrasive or solvent additives are permitted
in the fluids.
4.5
Electrical connection, gear change
The gearbox is electrically connected using the
supplied 8-pole Harting connector (HAN 8 U). The
plug-in connection is located on the shift unit.
4.5.1
Shift unit
Technical data:
Power consumption
84 W
Supply voltage
24 V DC ±10%
Max. pickup current
5 A
Nominal current:
3.5 A
Index of protection
IP64
The required cable lead diameter is 1.5 mm².
The 24 V DC connection voltage and 5 A power
consumption must be assured on the shift unit
connector.
Losses due to cable length and transition resistors
must be taken into account.
Scope of supply:
Sleeve housing, screw connection, socket insert
and 8 jacks, type Harting AWG16. The shift unit
can only be obtained as a complete part.