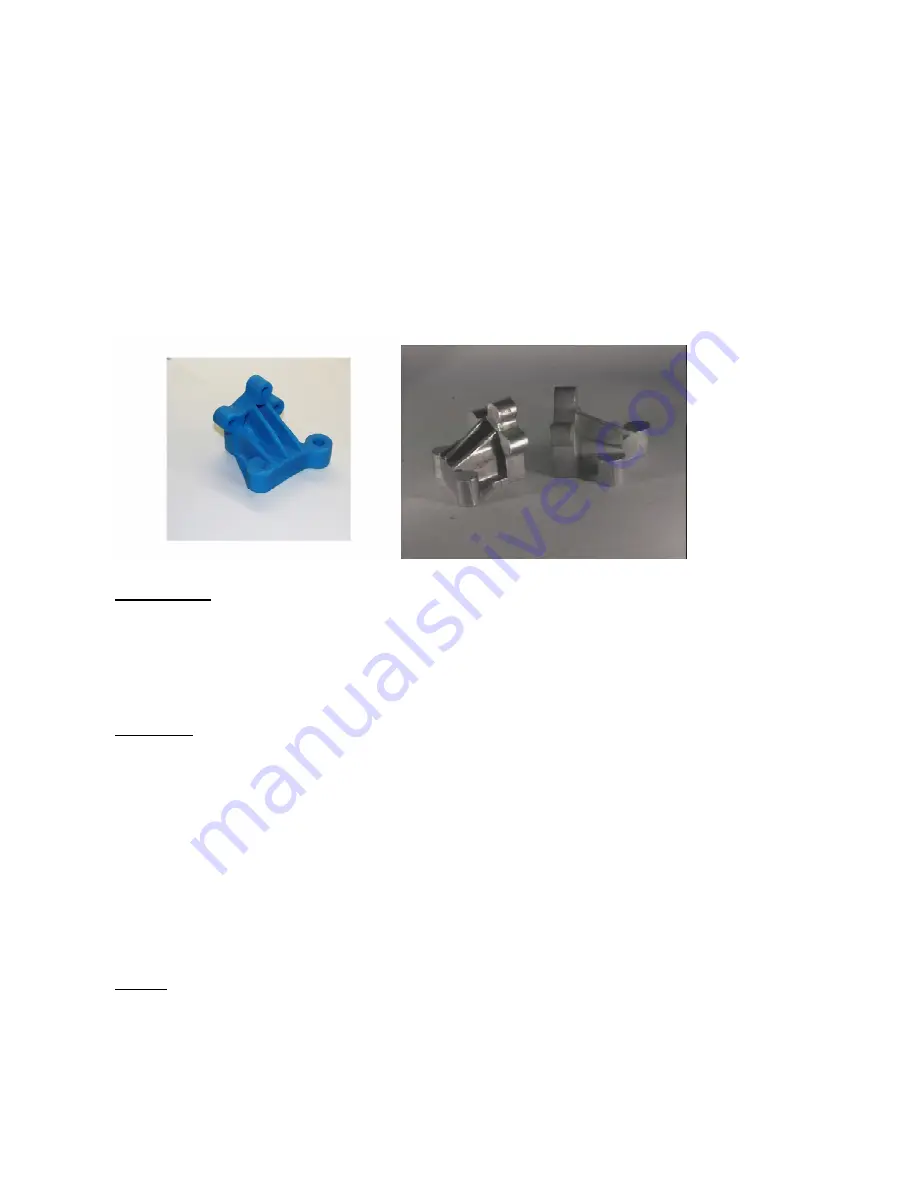
68
I
NVESTMENT
C
ASTING
Z Corp. parts can be used as investment casting patterns to quickly get metal parts. Starch-based parts can be
infiltrated with cyanoacrylate resin or wax and used instead of a standard wax pattern in the investment casting
process. The parts burn out well and do not have any expansion problems that would lead to shell cracking.
Investment casting of Z Corp. parts is a good way to get a final prototype, or a near-net shape part made of the
specific alloy your application requires. It can also be used for short-run production when time is extremely
important. 25% of Z Corp. users have had a part cast at some point in their design process.
General Notes
Consult with experienced foundry personnel to incorporate best practices in casting design when designing your
pattern. They will help the designer or engineer to design their part with the gate, runners and secondary opera-
tions in mind. Operations and equipment vary from foundry to foundry. Success has been achieved consistently
in a variety of situations and locations using the notes below as a guide. Steps that have been varied to achieve
success are noted.
Preparation
1. Starch-based powder parts should be used. Oven-drying the part at 104
o
F (40
o
C) after removal has been
included in the process at some locations, especially where humidity may be an issue with ‘green’ part character-
istics. Additional gate(s) may be incorporated in the set-up of the mold to increase air flow during burn-out of the
casting pattern.
2. Patterns should be infiltrated with either wax or resin. Wax infiltration is an excellent treatment for investment
casting patterns. Wax infiltrated parts will behave similarly to common wax patterns when they expand. The ZW4
or ZW3 Waxer and hand application methods have both been successfully used on Z Corporation parts. Some
users briefly blast their parts with a consumer hairdryer or heat gun to quickly heat and re-cool the wax to improve
surface finish.
Patterns can also be infiltrated with resin for increased strength. Surfaces should be sanded to their desired
finish after this step. Then coat with wax.
Casting
1. Z Corporation patterns can be assembled on standard wax gates and runner systems. They should be coated
with the normal 6-8 shell layers of slurry.
Содержание ZPrinter 310
Страница 1: ...ZPRINTERTM 310 USER MANUAL PART NUMBER 09508 REV C SEPTEMBER 2003...
Страница 9: ...9 www zcorp users com SYSTEM COMPONENTS ZD4i Depowdering Station ZPrinter 310 System...
Страница 60: ...60 service zcorp com...
Страница 98: ...Appendix I 09521 ZCastTM Design Guide Rev A ZCastTM Direct Metal Casting DESIGN GUIDE September 2003...
Страница 117: ...Appendix I ZCast Design Guide 20 Accumulated slag on the top of the crucible should be removed prior to pouring...
Страница 127: ...Click below to find more Mipaper at www lcis com tw Mipaper at www lcis com tw...