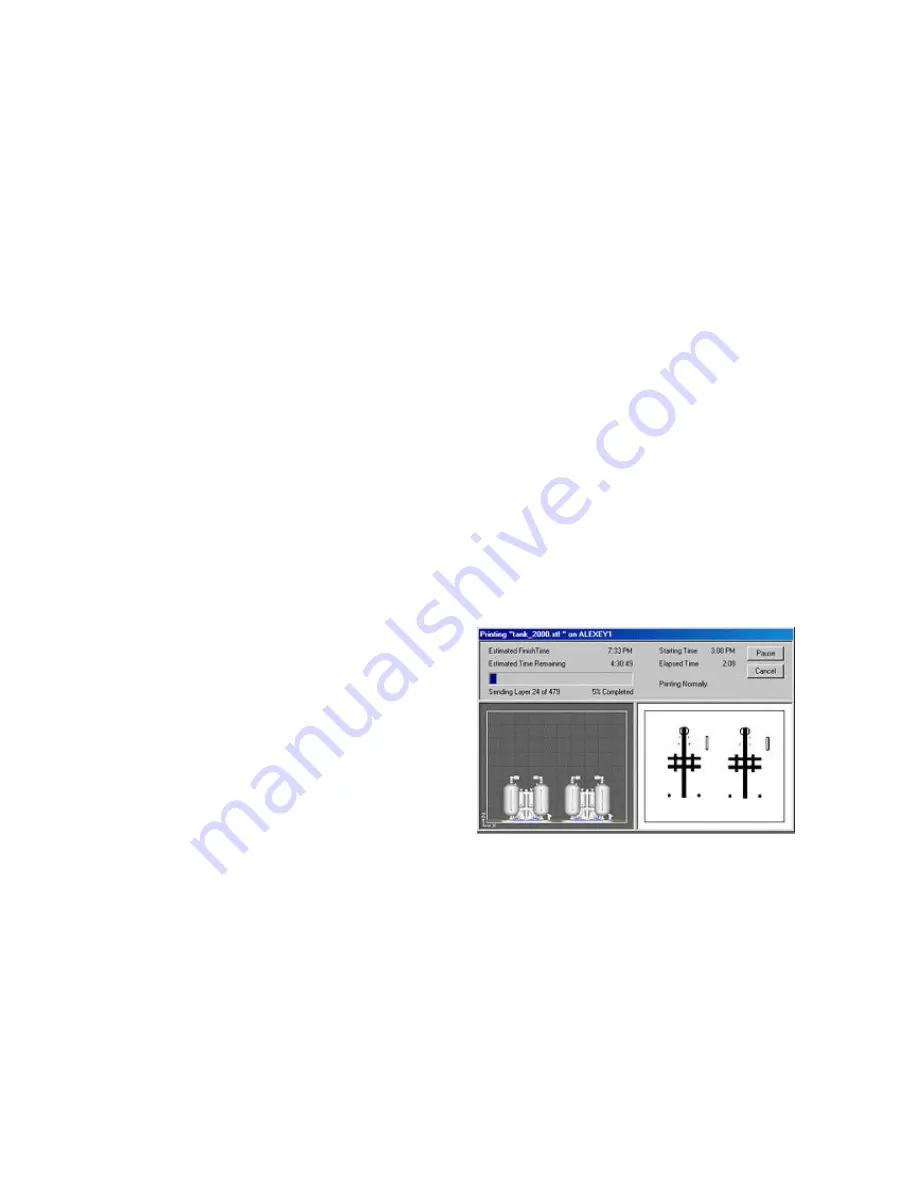
50
S
ATURATION
V
ALUES
The saturation values determine how much binder is placed on the powder to print the part. The part is made up
of two areas, the shell and the core, as described in Chapter 1,
Overview
. Thus, there are two saturation values,
one each for the shell and core. In general, the shell saturation is higher than the core saturation. The ZPrint
Software will display the recommended values for each powder type.
1.
Plaster Material System
The shell and core saturation values for the plaster material system are generally constant values, meaning that
there is only one value for all geometry types.
2.
Starch Material System
The shell and core saturation values for the starch material system depend on part geometry. A thick walled part
will have lower shell saturation than a thin walled part. Core saturation is dependent on the wall thickness of the
part. The thinner the wall thickness the higher the core saturation; the thicker the wall thickness the lower the core
saturation. The ZPrint Software will recommend shell and core saturation values based on the part geometry. If
parts come out weak, increase the saturation values by 10%; if parts are difficult to depowder, decrease the
saturation values by 10%.
3.
ZCast Material System
The shell and core saturation values for the ZCast material system are generally constant values, meaning that
there is only one value for all geometry types.
P
RINTING
THE
B
UILD
It is strongly recommended that the build settings be
confirmed before printing. To check build settings, choose
‘3D Print Setup’ under the File menu or click on the icon
located on the taskbar.
After all build settings have been confirmed:
1. Choose ‘3D Print’ under the File menu.
2. A dialog box will appear asking that powder and fluid
levels to be checked.
3. Press ‘OK’ to confirm that these have been checked to
begin the build.
Once the build has begun, a dialog box will appear reporting the status of the build.
Содержание ZPrinter 310
Страница 1: ...ZPRINTERTM 310 USER MANUAL PART NUMBER 09508 REV C SEPTEMBER 2003...
Страница 9: ...9 www zcorp users com SYSTEM COMPONENTS ZD4i Depowdering Station ZPrinter 310 System...
Страница 60: ...60 service zcorp com...
Страница 98: ...Appendix I 09521 ZCastTM Design Guide Rev A ZCastTM Direct Metal Casting DESIGN GUIDE September 2003...
Страница 117: ...Appendix I ZCast Design Guide 20 Accumulated slag on the top of the crucible should be removed prior to pouring...
Страница 127: ...Click below to find more Mipaper at www lcis com tw Mipaper at www lcis com tw...