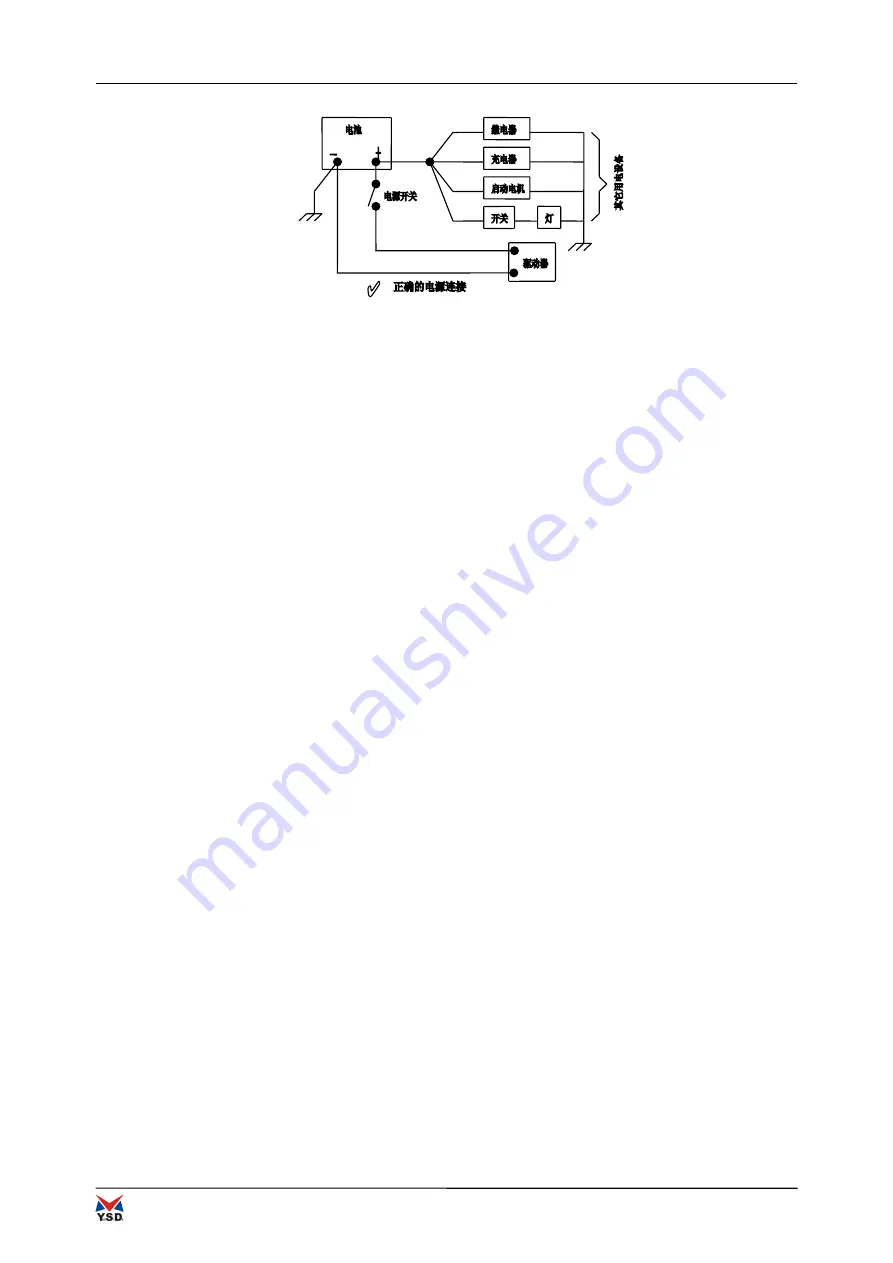
OT2115
Driver
8
Figure 3-1 power line connection method
4.2 Drive installation
The temperature range of the drive is 40 DEG C 70. The driver is installed in a position that
is easy to adjust and connection, and should be installed as close as possible to the actuator
and the power supply battery so as to meet the requirement of the cable length. Do not expose
the drive to radiation heat sources such as exhaust pipes or turbocharger.
The driver will generate some heat, so the surface should be in full contact with the air
environment. The driver is fixed on the heat conductive plate with a thickness of no less than
3 and a minimum area of 0.4.
General drive can be directly installed in the control cabinet. Do not install the drive
directly on the engine. Drive installation position should be far away from high voltage or
strong current device and the device that produces electromagnetic interference. After the
initial adjustment is completed, the engine is in normal operation state, and the manual
operation is not needed.
4.3 Actuator installation
The actuator is mounted on the engine, and the actuator itself generates heat,
especially in the case of blocking or other requirements for maximum torque output.
Therefore, the maximum operating temperature of the actuator should not exceed
100.
The installation personnel should consider the thermal conductivity of the installation and
the installation position of the engine body temperature, if the installation position of the
engine body temperature is too high, should take appropriate measures to heat insulation. Under
the general conditions, the high thermal conductivity of aluminum and low carbon steel
materials should be used as a mounting bracket. Air free flow through the upper end of the
heat sink will be conducive to heat. Therefore, the heat sink should be kept clean so as to
improve the heat transfer. Do not spray paint or other materials on the heat sink, as this
will reduce the efficiency of heat transfer.