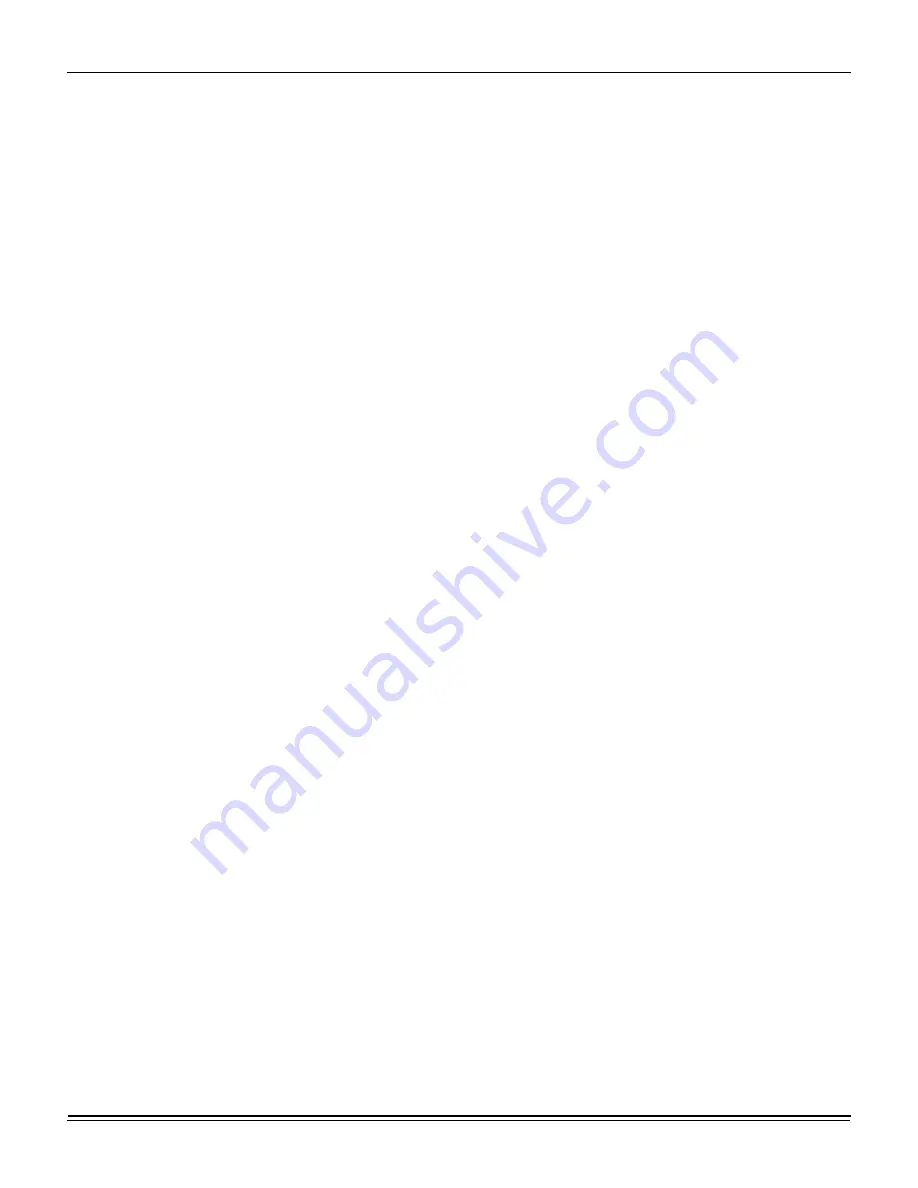
5188236-BIM-A-0316
Johnson Controls Unitary Products
63
wired per the wiring diagram. If there is any indication the unit
has been previously repaired, then the first priority is to verify
that the furnace is wired per the wiring diagram. Miss-wired
units will give false flash codes.
Ignition Control Board
The ICB controls the ignition of the pilot, the opening and
closing of the gas valves and the operation of the draft (inducer)
motor. It also monitors all the furnace safety components.
If the ICB LED is on steady, then verify the wiring of the unit to
the wiring diagram and if OK, then replace the ICB. If the unit
has power and the ICB LED is not flashing, then remove the 3
pin connector (single stage gas heat) or 4 pin connector (2
stage gas heat) from the ICB. Measure the control voltage
between terminals 1 and 2 of the wiring harness connector. The
control voltage must be between 18 and 30 volts. If control
voltage is not present, then check the 3.2A circuit breaker to
verify that the circuit breaker has control voltage on both input
and output terminals. If control voltage is present on the input
and not the output of the circuit breaker, then reset or replace
the circuit breaker as necessary. If control voltage is present on
both sides of the circuit breaker, then check the power and
common wires between the unit control box and the ICB and
repair as necessary. If the control voltage is present, then verify
the cleanliness of the harness and the ICB connector, clean if
necessary and reconnect the wiring harness to the ICB and
observe ICB LED. If it now flashes the heartbeat, then the fault
was a bad connection between the harness connector and the
ICB connector or a broken wire exists in the harness. With the
harness connected to the ICB, gently move the wires in the
harness while observing the ICB LED. If heartbeat is steady,
then verify proper operation of the furnace. If the ICB does not
flash the heartbeat, then gently move the wires in the harness
connector while observing the ICB LED. If you get any flashes
of the ICB LED, then there is still a bad connection or a broken
wire. If no flashes are seen while gently moving the wires with
the harness connected to the ICB, then replace the ICB and
verify proper operation of the furnace.
Centrifugal Switch
The centrifugal switch is an integral part of the draft motor. The
centrifugal switch closes when the motor speed increases to
~2500 rpm and opens when the motor speed descends to
~2000 rpm.
If a flash code indicates the centrifugal switch is causing a fault,
then
1.
If the flash code indicates the switch is open with the draft
(inducer) motor on (flash code 2), then
a. Disconnect power to the unit. Using a screw driver, spin
the draft motor blower wheel. If bound or dragging, then
visually inspect the draft motor blower wheel area for
debris. If debris is present, then clear debris and verify
proper furnace operation. If clear, then replace the draft
motor and verify proper furnace operation.
b. Restore power to unit and induce a call for heat.
Measure the voltage across the two draft motor leads
(white and red on single stage models and white and
black on two stage models). If it is less than 177 volts,
then check and repair the power circuit to the draft
motor. If the voltage is greater than 176 volts and the
draft motor is not turning, then disconnect power and
draft motor power leads. Measure the resistance of the
draft motor windings. If an open circuit exists in the
motor, then replace the draft motor. If the voltage is
greater than 176 volts and the motor is turning, then
check the centrifugal switch wiring between the ICB and
the draft motor. If OK, then disconnect power to the unit
and place the gas valve in the off position. Prepare to
temporarily jumper the wires connected to terminals 3
and 8 of the ICB 9 pin harness connector by
disconnecting the draft motor leads from the 9 pin
harness. Restore the power to the unit and induce a call
for heat. Jumper wires 3 and 8. If the ignition sequence
is started after 15 seconds (audible sparking of the
igniter), then replace the draft motor reconnecting the
centrifugal switch wiring per the wiring diagram. If not,
then replace the ICB, remove the jumper and reconnect
the centrifugal switch wiring per the wiring diagram.
Place the gas valve in the on position and verify proper
furnace operation.
2.
If the flash code indicates the switch is closed with the draft
(inducer) motor off (flash code 3), then disconnect the 9 pin
connector from the ICB and measure the continuity of the
centrifugal switch with a battery powered test light or an
ohm meter between terminals 3 and 8 of the harness
connector. If a closed circuit is indicated, then check the
wiring between the ICB and the draft motor. If the wiring is
not shorted together, then replace the draft motor. If an
open circuit is indicated, then reconnect the 9 pin wiring
harness to the ICB and remove power to the unit for at
least 20 seconds. Restore power to the unit. If the ICB
continues to flash a code 3, then replace the ICB.
Pilot Flame Lockout
The ICB counts the number of flame losses during the same call
for heat. If more than 16 flame losses occur within the same call
for heat, then the control temporarily locks out furnace operation
for 5 minutes (flash code 5). If the call for heat remains after the
5 minutes, then the ICB will retry the ignition sequence. The
flame losses can be due to low inlet pressure, debris around
flame sensor, plugged pilot burner, soot on the surface of the
flame sensor or misadjusted pilot pressure. Remove the power
to the unit for 20 seconds and then restore power to the unit.
Induce a call for heat and observe the pilot flame in the flame
sensor area to determine the best course of action.
1.
If the flame is strong and stable in the flame sensor area,
then verify the position of the flame sensor per the start up
procedures. If ok, then remove the flame sensor and check
the cleanliness of the electrode. If clean, then replace the
flame sensor and adjust pilot per the start up procedures. If
not clean, then clean, reinstall and adjust pilot per the start
up procedures.
2.
If the flame is weak or unstable in the flame sensor area,
then verify the gas inlet pressure. If gas inlet pressure is
above the minimum inlet pressure stated on unit data label,
then adjust the pilot pressure per the start up procedures. If