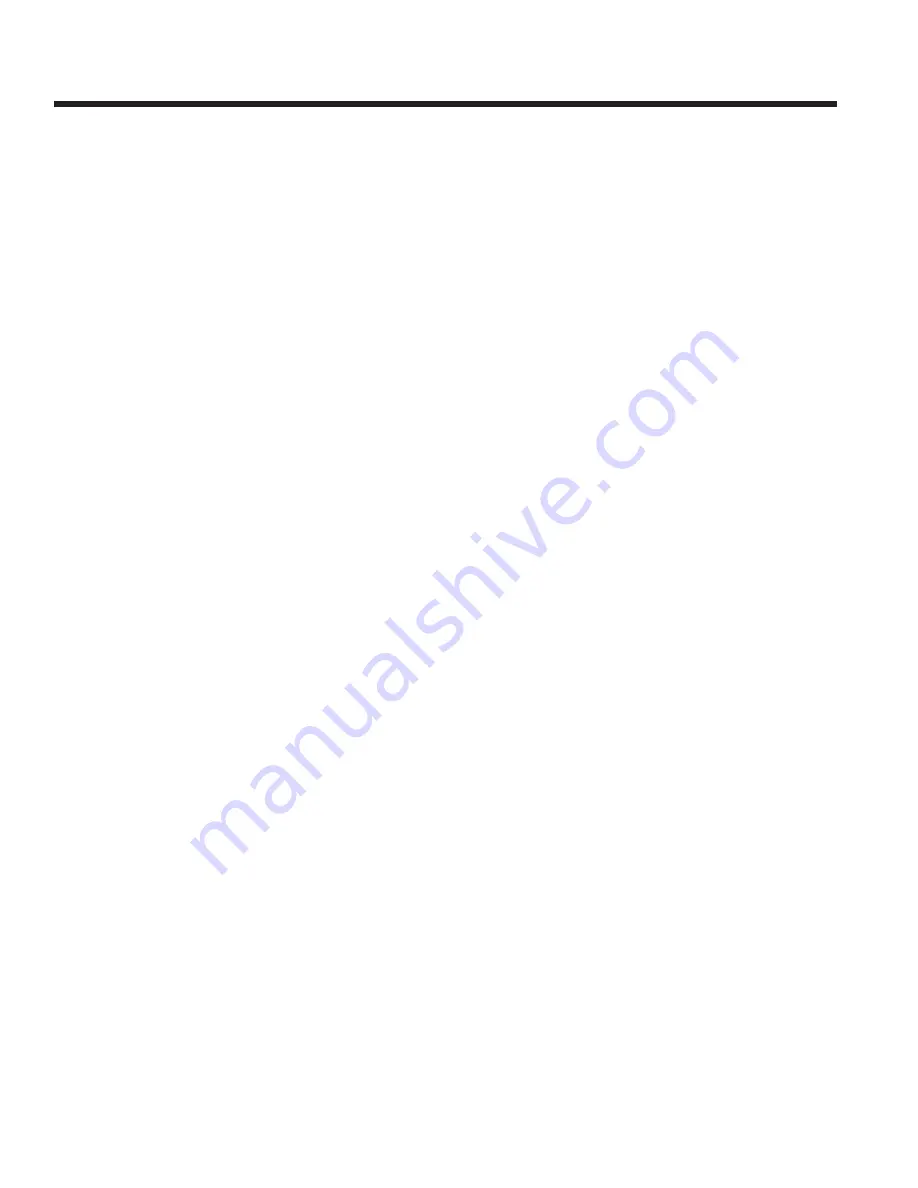
JOHNSON CONTROLS
6
FORM 201.23-EG1 (1013)
• Display Data: Chiller liquid return and leaving tempera-
tures, ambient, lead compressor identification, clock
and schedule, (variable) out of range, remote input
indication, chilled liquid reset setpoint, and history
data for last ten shutdown faults. Also provided are
messages for compressor suction, discharge, and oil
pressures and temperatures, suction and discharge
superheats, percent of full-load, operating hours,
starts, and anti-recycle timer status. Status Messages
for manual override, unit switch off, compressor run,
run permissive, remote controlled shut down, no cool
-
ing load, daily/holiday shut down, anti-recycle timer.
• During extreme or unusual conditions (i.e. blocked
condenser coils, ambient above scheduled maximum,
etc.) the chiller control system will avoid safety shut
-
down by varying the chiller controls and cooling load
output to stay online and avoid safety limits being
reached. This allows maximum possible cooling ca
-
pacity until the unusual condition is cleared and avoids
costly shutdowns. The system monitors the following
parameters and maintains the maximum cooling output
possible without shutdown of the equipment: motor
current, suction pressure and discharge pressure.
• System Safeties are provided for individual compres-
sor systems to perform auto-reset shut down (manual
reset required after the third trip in 90 minutes). Safe
-
ties include: high discharge pressure or temperature,
low suction pressure, high/low motor current, high
motor temperature, high pressure switch, high/low
differential oil pressure, high oil temperature, low suc
-
tion superheat, critical sensor malfunction, low or high
current, phase loss/single phase power, overload of
motor windings, and low voltage.
• Unit Safeties are provided for the chiller to perform
auto-reset shut down for the following conditions: high
or low ambient, low leaving chilled liquid temperature,
under voltage, and flow switch operation.
COMPLETE FACTORY PACKAGE
• These air-cooled chillers are shipped as a complete
factory package. Each unit is completely assembled
with all interconnecting refrigerant piping and internal
wiring, ready for field installation:
• Each compressor is installed on its own independent
refrigerant circuit, which is factory pressure tested,
evacuated, then fully charged with HFC-134a refriger
-
ant and oil.
• After assembly, an operational test is performed with
water flowing through the cooler to ensure each circuit
operates correctly.
• Unit panels, structural elements, control boxes and
heavy gauge structural base shall be constructed
of galvanized steel. Unit panels, control boxes and
structural base are finished with a baked on powder
paint. All painted surfaces shall be coated with baked
on powder paint which, when subject to ASTMB117,
1,000 hour, 5% salt spray test, yields minimum ASTM
1654 rating of “6”.
• Design is IAW applicable sections of ASME Pressure
Vessel Code, NFPA 70 (National Electrical Code), U.L.
and cU.L. standards and ASHRAE/ANSI-15 Safety
Code for Mechanical Refrigeration.
• Units are rated (all) and certified (140 - 200 tons) IAW
AHRI Standard 550/590.
• Design is IAW ASHRAE 90.1 Energy Standard for
Building except Low-Rise Residential Buildings and
AHRI 70 Sound Rating of Large Outdoor Refrigeration
and Air Conditioning Equipment.
• YCIV chillers are designed within EN ISO 9001 and
built within an EN ISO 9002 accredited manufacturing
organization.
• All exposed power wiring routed through liquid-tight,
UV-stabilized, non-metallic conduit.
• When required, chillers (50 Hz only) have the option
available to conform to the following European Direc
-
tives:
• Machinery directive (2006/42/EC)
• Low Voltage Directive (2006/95/EC)
• EMC Directive (2004/108/EC)
• Pressure Equipment Directive (97/23/EC)
• Safety Code for Mechanical Refrigeration (EN378-2
(2008)
Unit Overview - continued
Содержание YCIV0157E/V
Страница 57: ...JOHNSON CONTROLS FORM 201 23 EG1 1013 57...
Страница 59: ...JOHNSON CONTROLS FORM 201 23 EG1 1013 59...
Страница 61: ...JOHNSON CONTROLS FORM 201 23 EG1 1013 61...
Страница 63: ...JOHNSON CONTROLS FORM 201 23 EG1 1013 63...
Страница 65: ...JOHNSON CONTROLS FORM 201 23 EG1 1013 65...
Страница 67: ...JOHNSON CONTROLS FORM 201 23 EG1 1013 67...
Страница 69: ...JOHNSON CONTROLS FORM 201 23 EG1 1013 69...
Страница 71: ...JOHNSON CONTROLS FORM 201 23 EG1 1013 71...
Страница 73: ...JOHNSON CONTROLS FORM 201 23 EG1 1013 73...
Страница 75: ...JOHNSON CONTROLS FORM 201 23 EG1 1013 75...
Страница 77: ...JOHNSON CONTROLS FORM 201 23 EG1 1013 77...
Страница 89: ...JOHNSON CONTROLS FORM 201 23 EG1 1013 89 INTENTIONALLY LEFT BLANK...
Страница 102: ...JOHNSON CONTROLS 102 FORM 201 23 EG1 1013 Typical Control Wiring Two Compressor...
Страница 104: ...JOHNSON CONTROLS 104 FORM 201 23 EG1 1013 Typical Control Wiring Three Compressor...
Страница 106: ...JOHNSON CONTROLS 106 FORM 201 23 EG1 1013 Typical Control Wiring Four Compressor...
Страница 107: ...JOHNSON CONTROLS FORM 201 23 EG1 1013 107...
Страница 114: ...Form 201 23 EG1 1013 Supersedes 201 23 EG1 713...