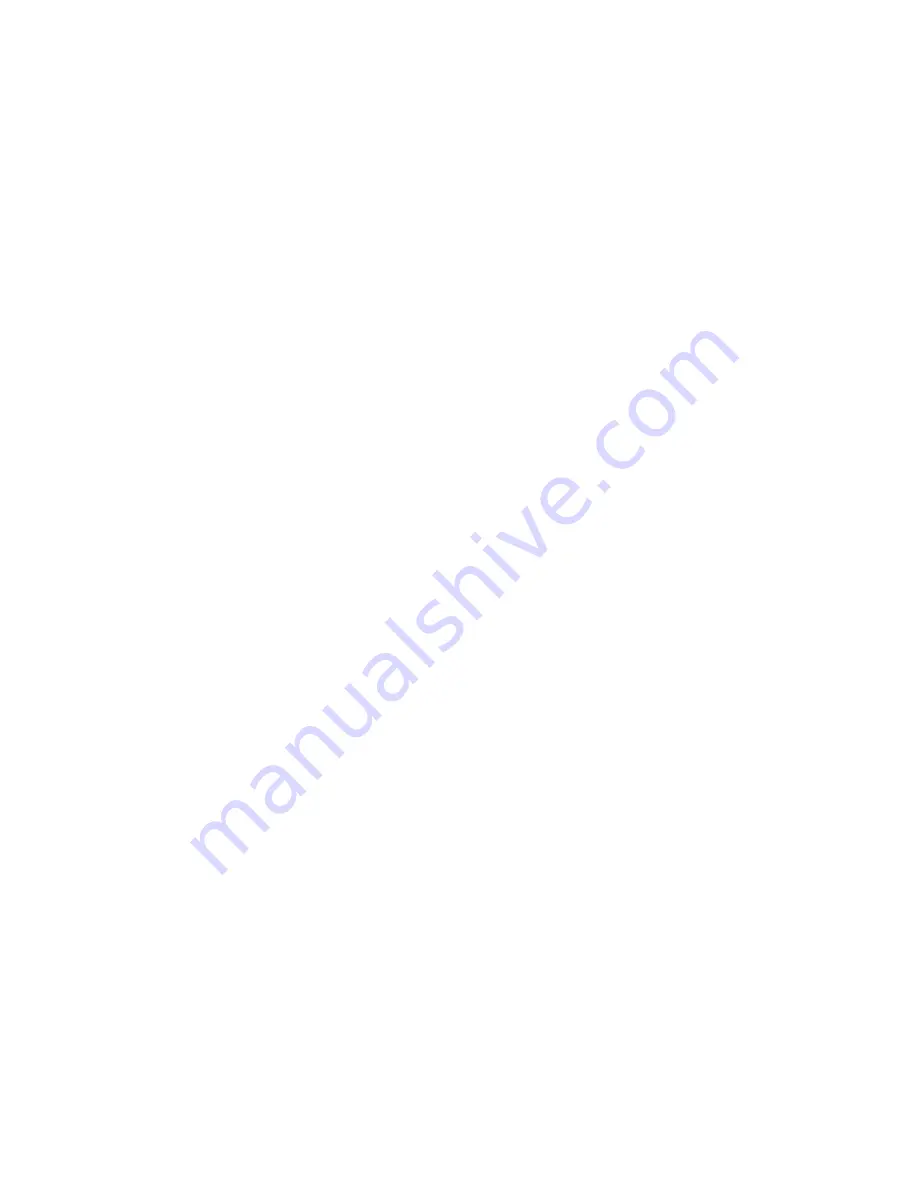
FORM 201.23-CL1 (309)
2
JOHNSON CONTROLS
Isolation / Protection
Verify all sources of electrical supply to the unit
are taken from a single point of isolation. Check
that the maximum recommended fuse sizes given
in the Technical Data Section of IOM has not been
exceeded.
Control Panel
Check the panel to see that it is free of foreign materials
(wire, metal chips, etc.) and clean out if required.
Power Connections
Check that the customer power cables are connected
correctly to the terminal blocks or optional circuit
breaker. Ensure that connections of power cables within
the panels to the circuit breaker or terminal blocks are
tight.
grounding
Verify that the unit’s protective ground terminal(s)
are properly connected to a suitable grounding point.
Ensure that all unit internal ground connections are
tight.
Water System
Verify the chilled liquid system has been installed
correctly, and has been commissioned with the correct
direction of water flow through the cooler. The inlet
should be at the refrigerant piping connection end of
the cooler. Purge air from the top of the cooler using
the plugged air vent mounted on the top of the cooler
body.
Flow rates and pressure drops must be within the limits
provided in the IOM. Operation outside of these limits
is undesirable and could cause damage.
If mains power must be switched OFF for extended
maintenance or an extended shutdown period, the
compressor suction, discharge and economizer service
stop valves should be closed (clockwise). If there is
a possibility of liquid freezing due to low ambient
temperatures, the coolers should be drained or power
should be applied to the chiller. This will allow the
cooler heater to protect the cooler from freezing down
to –20°F. Before placing the unit back in service,
valves should be opened and power must be switched
on (if power is removed for more than 8 hours) for at
least 8 hours (24 hours if ambient temperature is below
86°F [30°C]) before the unit is restarted.
Flow Switch
Verify a chilled water flow switch is correctly fitted in
the customer’s piping on the cooler outlet, and wired
into the control panel correctly using shielded cable.
There should be a straight run of at least 5 pipe
diameters on either side of the flow switch. The flow
switch should be connected to terminals 2 and 13 in
the panel.
temperature Sensor(s)
Ensure the leaving liquid temperature sensor is coated
with heat conductive compound (Part No. 013-00890-
000) and is inserted to the bottom of the water outlet
sensor well in the cooler. This sensor also provides some
freeze protection and must always be fully inserted in
the water outlet sensor well.
Programmed Options
Verify that the options factory-programmed into the
Micro Panel are in accordance with the customer’s
order requirements by pressing the OPTIONS Key on
the keypad and reading the settings from the display.
Programmed Settings
Ensure the system cutout and operational settings
are in accordance with the operating requirements by
pressing the PROGRAM key.
Date and time
Program the date and time by first ensuring that the
CLK jumper JP2 on the chiller control board is in the
ON position. Then press the DATE/TIME key and set
the date and time.
Start/Stop Schedule
Program the daily and holiday start/stop by pressing
the SCHEDULE key.
Setpoint and Remote Offset
Set the required leaving chilled liquid temperature
setpoint and control range under the SETPOINTS Key.
The chilled liquid temperature control settings need to
be set according to the required operating conditions.
If remote temperature reset (offset) is to be used, the
maximum reset required must be programmed by
pressing the SETPOINTS Key.
Содержание YCIV 0157-0397 60Hz
Страница 11: ...FORM 201 23 CL1 309 JOHNSON CONTROLS 11 notes ...