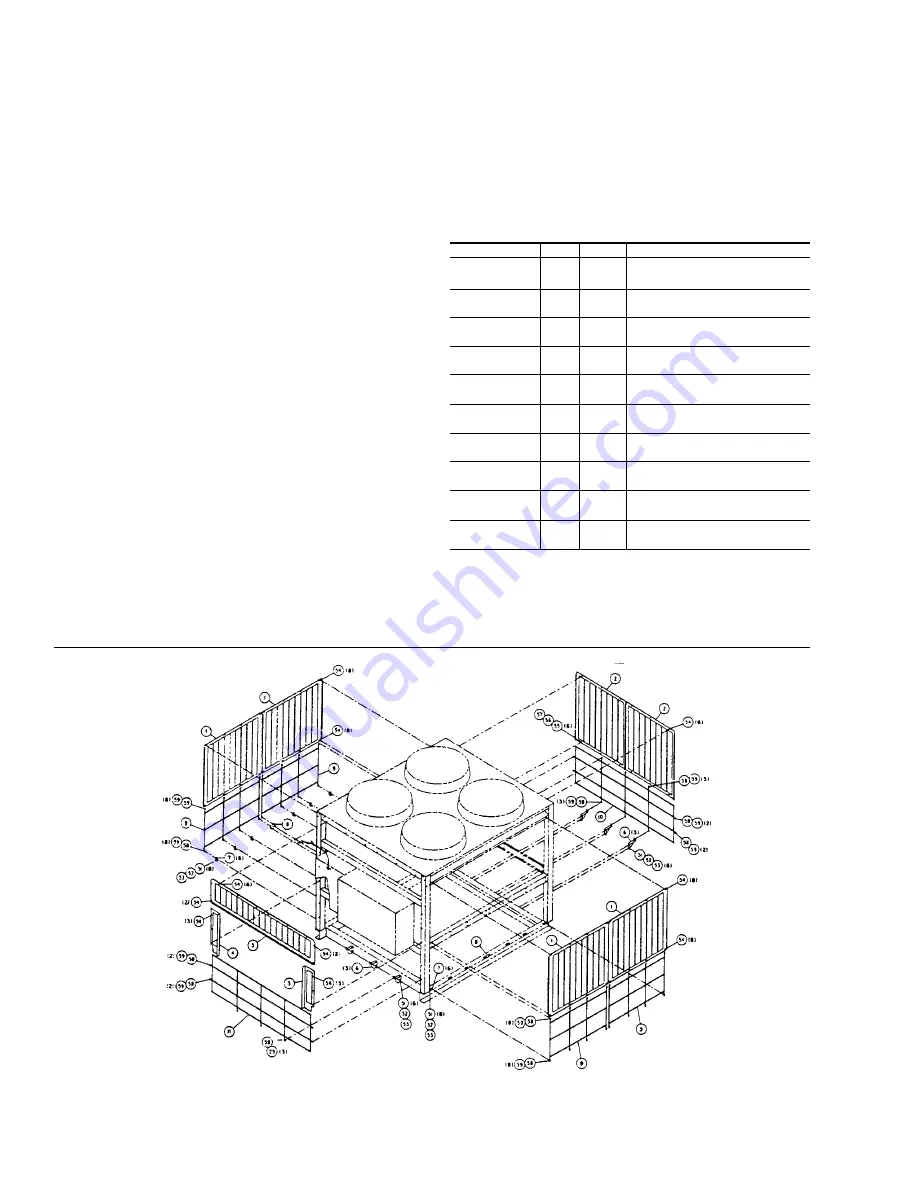
84
YORK INTERNATIONAL
LD02102
OPTIONAL DECORATIVE TAMPERPROOF
ENCLOSURE (LOUVERED & WIRE GRILLE)
General
A combination louvered and wire grille enclosure is avail-
able for the chiller for the prime purpose of deterring un-
authorized access to components of the chiller.
Kit 475-04559-002 is the decorative/tamperproof enclo-
sure which consists of a combination of louvered sheet
metal panels and weather resistant wire grilles along with
mounting hardware. This kit has a further purpose of pre-
senting a pleasing appearance to the chiller when it is
located in a highly visible area.
Installation
1. Refer to Fig. 37 and the associated parts list. Before
starting installation, all of the items in the kit should
be identified by comparing with Fig. 37.
2. All holes for mounting kit parts are provided in both
the chiller frame and the added supports; therefore,
it should be unnecessary to drill holes.
3. Install the louvered panels and wire grilles using the
proper hardware and supports. Refer to Fig. 37 and
the Parts List for placement of the grilles/panels and
the proper hardware required. Discard existing grilles
to attach the louvered panels where necessary.
4. Notch grilles to suit water connection and wiring har-
nesses as needed.
5. If the High Ambient Sunshield Kit or Disconnect Op-
tion is installed, field adaption will be required where
parts of the kits interfere. Touch up exposed metal
parts to prevent rust.
NOTES:
1. Notch grilles to suit water connections and wiring harnesses.
2. Discard existing grilles to attach louver panels where necessary.
FIG. 37
LOUVERED AND WIRE GRILLE INSTALLATION
Parts List
PART #
ITEM QUAN.
DESCRIPTION
075-02563-002
1
4
Panel, Louvers Side Top
075-02563-005
2
2
Panel, Louvers Rear Top
075-02563-015
3
1
Panel, Louvers Front Top R.H.
075-02563-016
4
1
Panel, Louvers Front Top L.H.
075-02563-017
5
1
Panel, Louvers Front Top
075-02501-000
6
5
Bracket
075-02502-000
7
12
Clip, Retainer
075-02503-000
8
2
Clip, Retainer
026-31634-000
9
4
Grille, Side Btm.
026-32206-000
10
1
Grille, Rear Btm.
026-32207-000
11
1
Grille, Front Btm.
021-16205-000
51
28
Screw, Cap Hex 3/8-16 x 1/2
021-16158-000
52
28
Lock Washer Spg. 3/8
021-16139-000
53
28
Nut, Hex 3/8
021-16136-000
54
54
Screw, Tap Cut 1/4 x 1/2
021-16161-000
55
6
Screw, Cap Hex 1/4-20 x 3/4
021-16210-000
56
6
Lock Washer Spg. 1/4
021-16151-000
57
6
Nut, Hex 1/4
021-16203-000
58
49
Screw, Tap Type F 1/4 x 3/4 Lg.
021-16165-000
59
49
Washer, Flat 1/4