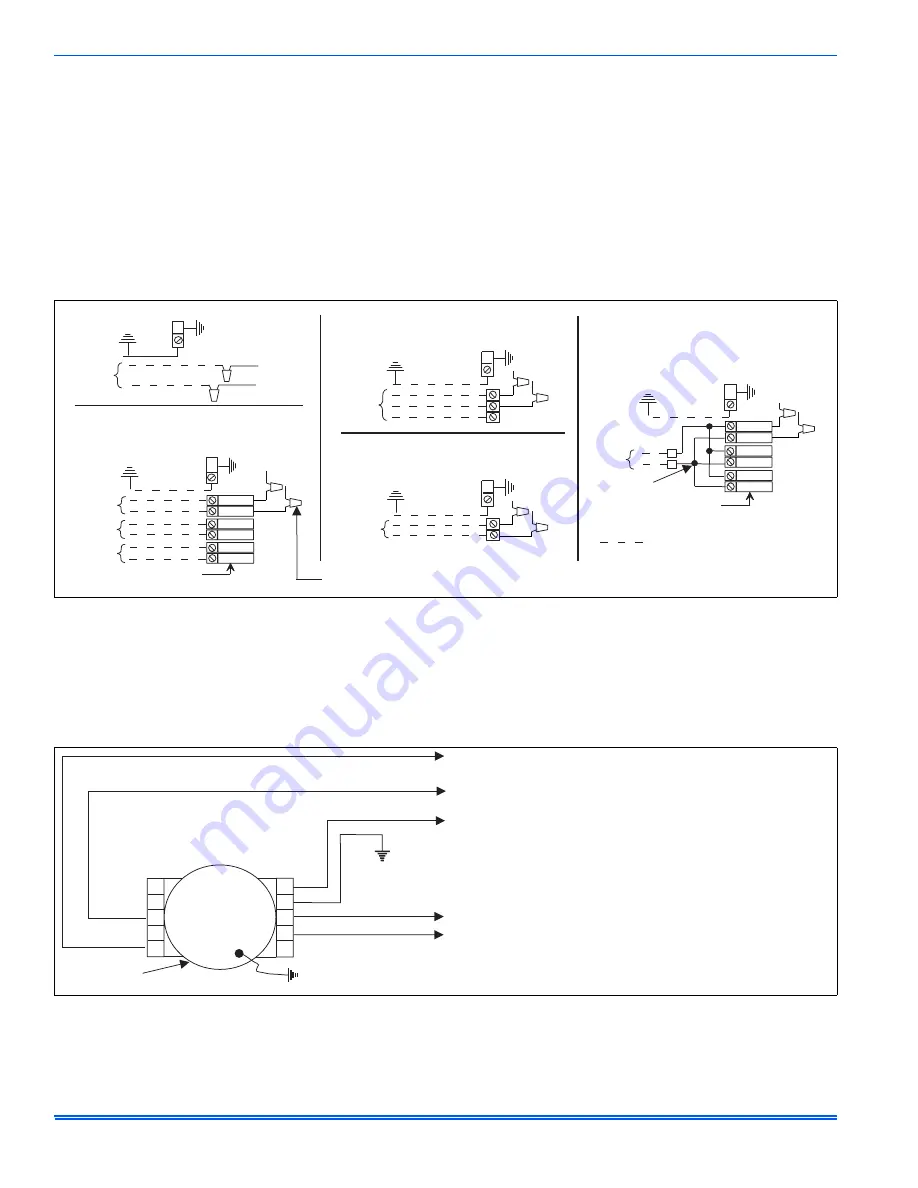
819682-UIM-A-0212
8
Johnson Controls Unitary Products
SECTION VII: LINE POWER
CONNECTIONS
Power may be brought into the unit through the supply air end of the
unit (top when unit is vertical) or the left side panel. Use the hole appro-
priate to the unit’s orientation in each installation to bring conduit from
the disconnect. The power lead conduit should be terminated at the
electrical control box. Refer to Tables 11, 12, 14 and 15 to determine
proper wire sizing. Also see Figure 3. To minimize air leakage, seal the
wiring entry point at the outside of the unit.
All electrical connections to air handlers must be made with copper con-
ductors.
Direct connection of aluminum wiring to air handlers is
not approved.
If aluminum conductors are present, all applicable local and national
codes must be followed when converting from aluminum to copper con-
ductors prior to connection to the air handler.
If wire other than uncoated (non-plated), 75° C ambient, copper wire is
used, consult applicable tables of the National Electic Code (ANSI/
NFPA 70). The chosen condutor and connections all must meet or
exceed the amperage rating of the overcurrent protector (circuit breaker
or fuse) in the circuit.
Additionally, existing aluminum wire within the structure must be sized
correctly for the application according to National Electric Code and
local codes. Caution must be used when sizing aluminum rather than
copper conductors, as aluminum conductors are rated for less current
than copper conductors of the same size.
SECTION VIII: BLOWER SPEED
CONNECTIONS
All air handlers contain a programmed 5 speed high efficiency brush-
less DC motor.
Adjust blower motor speed to provide airflow within the minimum and
maximum limits approved for evaporator coil, electric heat and outdoor
unit. Speed tap adjustments are made at the motor terminal block, See
Figure 12. Airflow data is shown in Tables 16 and 17.
Connect motor wires to motor speed tap receptacle for speed desired.
See unit wiring label for motor wiring details.
FIGURE 8:
Line Power Connections
ELECTRIC HEAT
WITHOUT CIRCUIT BREAKER
SINGLE SOURCE (2.5 - 10 KW)
GND. LUG
POWER
SUPPLY
GND.
LUG
ELECTRIC HEAT
WITHOUT CIRCUIT BREAKER
3 PHASE (10 - 15 KW)
GND. LUG
POWER
SUPPLY
GND.
LUG
1 PHASE ELECTRIC HEAT
WITH CIRCUIT BREAKER
AS SHIPPED FROM FACTORY
SINGLE SOURCE
(2.5 - 25 KW) - 25 KW SHOWN
GND. LUG
POWER
SUPPLY
GND.
LUG
1 PHASE ELECTRIC HEAT
WITH CIRCUIT BREAKER
& BREAKER BAR REMOVED
MULTI-SOURCE (15 - 25 KW) - 25 KW SHOWN
GND. LUG
POWER
SUPPLY 1
GND.
LUG
POWER
SUPPLY 2
POWER
SUPPLY 3
TYPICAL WIRING WITHOUT ELECTRIC HEAT
GND. LUG
POWER
SUPPLY
GND.
LUG
POWER WIRING (208/230-1-60)
TERMINAL
BLOCK
TERMINAL
BLOCK
MAY BE 1, 2, OR 3
CIRCUIT BREAKERS
MAY BE 1, 2, OR 3
CIRCUIT BREAKERS
(JUMPER BAR)
CONNECT TRANSFORMER LEADS WITH
WIRE NUTS (TYPICAL ALL HEAT KITS)
FIGURE 9:
Blower Speed Connections
LOW FAN SPEED, CONNECTED
TO LOW FAN TERMINALS ON
CONTROL BOARD, SEE WIRING DIAGRAM
FOR LOW FAN SPEED BEHAVIOR, SEE “LOW FAN”
UNDER “REQUIRED CONTROL SET-UP” SECTION
TO CONTROL BOARD
24V LOW FAN
TO CONTROL BOARD
24V EAC
TO TRANSFORMER
230V
BLOWER
GRN
C
G
L
N
GRN
BLK
WHT
YEL
PUR
RED*
1
2
3
4
5
208/230V
FAN MOTOR
*