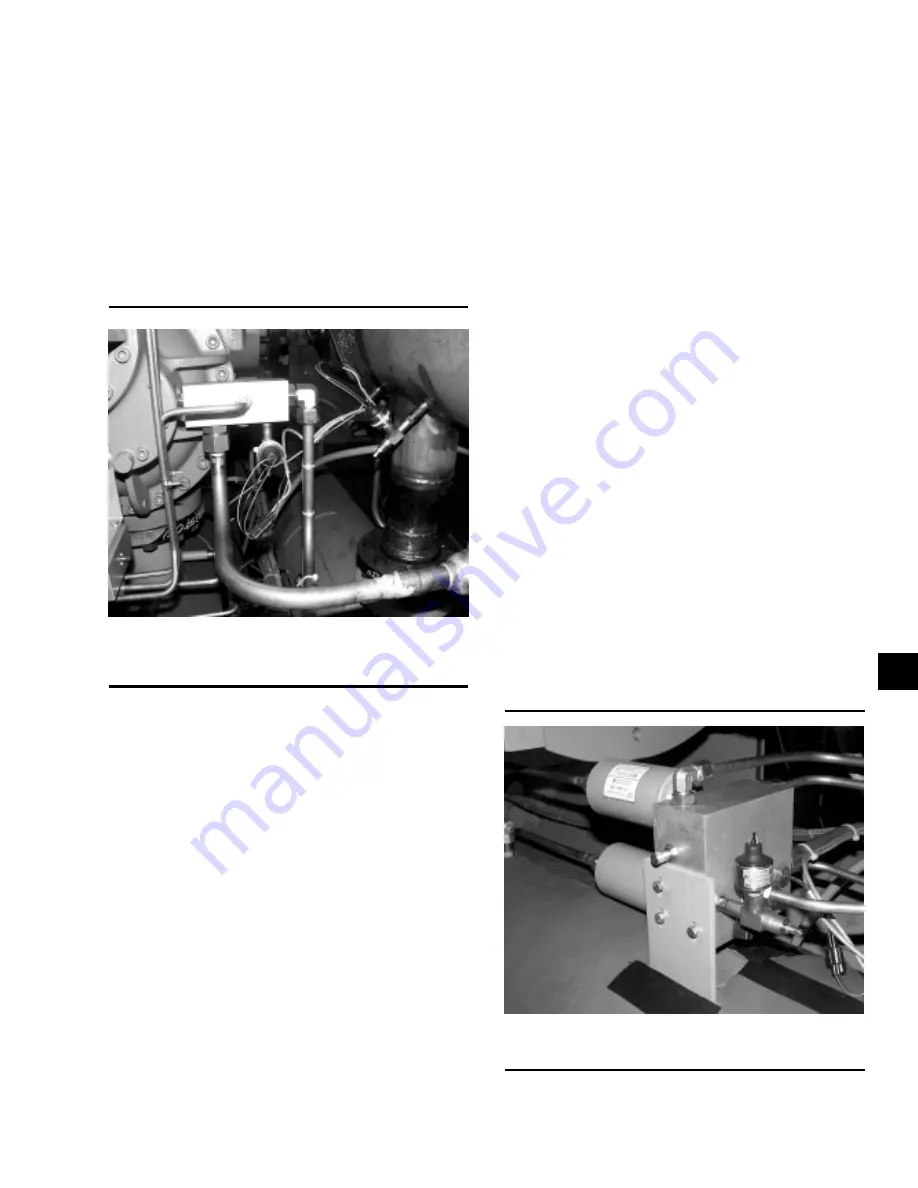
31
FORM 160.47-NOM3
YORK INTERNATIONAL
OIL SYSTEM (CONT’D)
The oil pressure transducer is located at the SB-2 mani-
fold. The differential pressure is measured as the dif-
ference between the Oil Pressure Transducer at SB-2
and the Filter Pressure Transducer located in the oil
separator. This value is compared to the limits in the
control panel logic. If the oil filter differential reaches
20 psid, a warning message is displayed by the control
panel display. If the oil filter reaches 25 psid, a safety
shutdown is initiated. See Figure 18.
An oil supply line from the manifold at SB-2 is piped to
the capacity control directional valve at Port P. The 4-
way capacity control solenoid (directional) valve directs
oil pressure against one side or the other of the slide
valve piston. The opposite side of the slide valve is re-
lieved to suction pressure at compressor port SC-11.
The differential pressure between the P port and the
suction pressure at Compressor Port SC-11 is what pro-
vides the force to load or unload the slide valve and
provide capacity control. Refer to the Capacity Control
Schematic Diagram.
Oil flows from the oil manifold at SB-2 to the brazed
plate, refrigerant cooled oil cooler. Cool oil leaving the
brazed plate heat exchanger flows to the eductor block
manifold. A new oil circuit has been incorporated into
the oil eductor block in Design Level “D”. The oil cir-
cuit is separate from the eductor oil management sys-
tem. See Figure 19.
The eductor block manifold oil circuit contains the Seal
Oil Pressure Transducer and a High Oil Temperature
00091VIP
FIG. 18 – OIL PRESSURE TRANSDUCER
LOCATION
00092VIP
FIG. 19 – EDUCTOR BLOCK
Safety sensor. The Seal Oil Pressure is monitored by
the control panel. The differential pressure between the
Seal Oil Pressure and the Evaporator Pressure Trans-
ducer is calculated and compared to the control panel
logic. If the differential reaches the set point (30 psid
for R-22 and 20 psid for R-134a, the control panel will
initiate a safety shutdown. A high oil temperature safety
shutdown will be initiated at 170ºF (77ºC).
The oil leaving the oil eductor manifold block flows into
the compressor at compressor port SB-3 to lubricate
the compressor bearings and shaft seal. All of the oil
that is injected into the compressor mixes with refriger-
ant gas during compression. The oil and refrigerant gas
is discharged into the oil separator, where it is sepa-
rated and returned to the oil sump. A high discharge
temperature safety is located in the discharge line, be-
tween the compressor and oil separator. This safety will
initiate a safety shutdown at 210ºF (99ºC).
Oil is separated from the refrigerant gas in the oil sepa-
rator. Oil is separated from the refrigerant gas in a three
step process.
In the first stage of oil separation, high velocity oil and
refrigerant gas in the compressor discharge line under
goes a rapid reduction in velocity as it enters the large
diameter oil separator. Most of the oil drops out of the
refrigerant gas stream due to the reduction in velocity.
The oil falls by gravity into the oil reservoir located in
the bottom of the oil separator.
The second stage of oil separation is accomplished by
directing the refrigerant gas through mesh pads that
have an extended surface area. Smaller liquid oil drop-
2