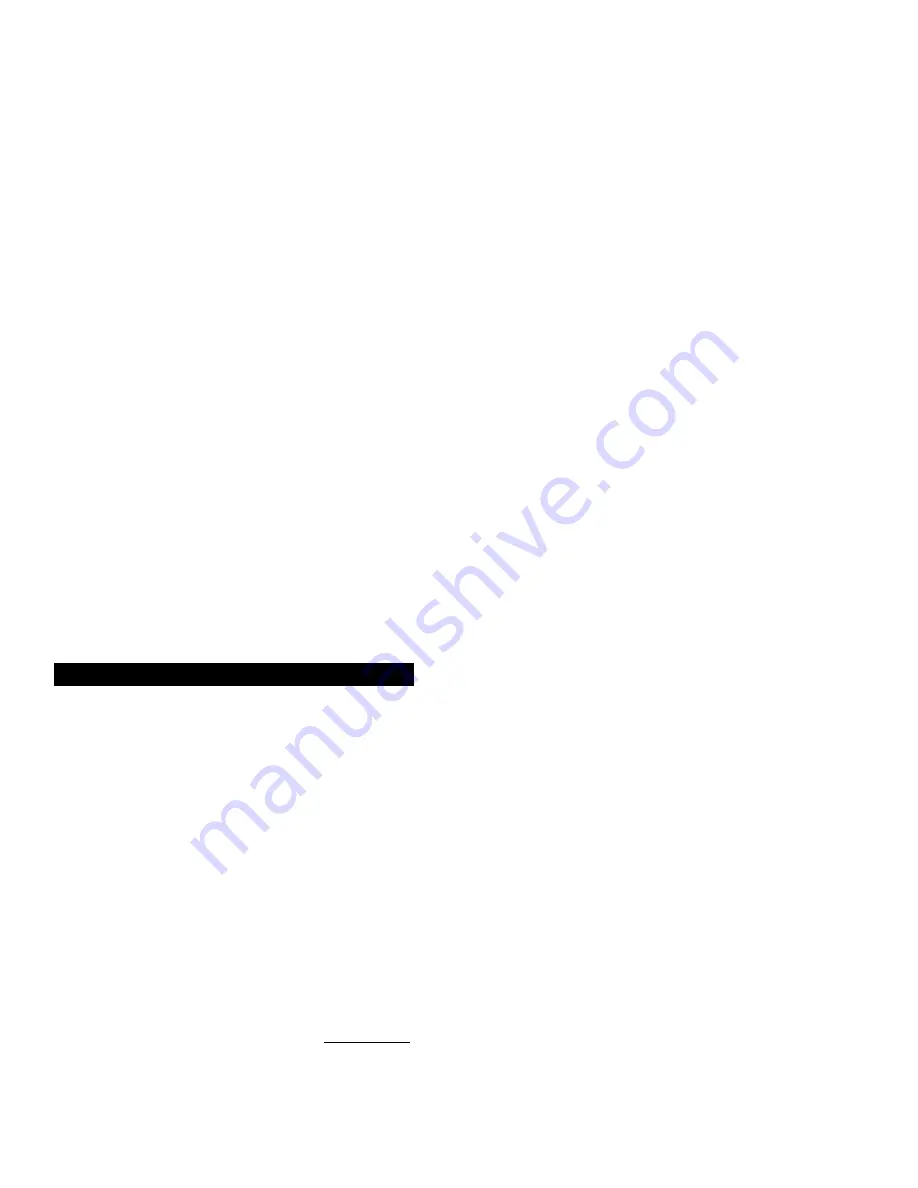
52
YORK INTERNATIONAL
3. Compressor coastdown for 150 seconds with com-
pressor oil pump running.
4. Engine control panel (ECP) post-lubes gear box for
one (1) minute.
CHILLER OPERATION
After the compressor reaches its operating speed, the
Prerotation Vanes will begin to open under the control of
the Microprocessor board which senses the leaving chilled
liquid temperature. The unit capacity will vary to maintain
the leaving chilled liquid temperature setpoint. The
Prerotation Vanes are modulated by an actuator under
the control of the Microprocessor board. The vane control
routine employs proportional plus derivative (rate) control
action. A drop in chilled liquid temperature will cause the
actuator to close the Prerotation Vanes to decrease chiller
capacity. When the chilled liquid temperature rises, the
actuator will open the Prerotation Vanes to increase the
capacity of the unit.
However, the loading of the engine cannot exceed the set-
ting of the
% ENGINE LOAD LIMIT
at any time during
the operation, since the MicroComputer Control Center 50
to 100% engine load limit software function will override
the temperature control function and prevent the prerotation
vanes from opening beyond the % engine load setting.
If the load continues to decrease, after the Prerotation
Vanes are entirely closed, the chiller will be shut down
by the Low Water Temperature control (LWT) function
which is displayed on the Control Center as:
MON 10:30 AM – LOW WATER TEMPERATURE – AUTOSTART
This occurs when the leaving chilled water temperature
falls to 4°F below setpoint or 36°F, whichever is higher.
The LWT shutdown logic is part of the Micro Board.
NOTE: If the temperature setpoint has been pro-
grammed within the last 10 minutes, the LWT
cutout is 36°F for 10 minutes.
Condenser Water Temperature Control
The YORK Millennium chiller is designed to use less
power by taking advantage of lower than design tem-
peratures that are naturally produced by cooling towers
throughout the operating year. Exact control of condenser
water such as a cooling tower bypass, is not necessary
for most installations. The chiller requires only that the
minimum condenser water temperature be no lower than
the value determined by referring to the formula below:
Min. ECWT = LCHWT - C RANGE + 5 + (15 x %LOAD)
100
where: ECWT = entering condensing water temperature
LCHWT = leaving chilled water temperature
C RANGE = condensing water temperature range
At start-up the entering condenser water temperature may
be as much as 25°F colder than the standby return chilled
water temperature. Cooling tower fan cycling will normally
provide adequate control of the entering condenser water
temperature on most installations.
CHECKING OPERATION
During operation, the following conditions should be peri-
odically checked:
1. On starting, the prerotation vanes should remain
closed until the compressor is up to speed, then the
vane motor should cause the vanes to modulate with
load requirements.
2. Be sure the oil pump is operating while unit is run-
ning.
3. Check Oil Pressure display. A gradual decrease in
bearing oil pressure of 5 to 10 PSI (with constant
suction and discharge pressures) may be an indica-
tion of a dirty filter. The filter should be replaced when
pressure loss is 30% or more of the original pres-
sure. The actual bearing oil pressure will vary with
compressor suction and discharge pressures. When
a new system is first operated under normal full load
conditions, the bearing oil pressure should be re-
corded as a reference point with which to compare
subsequent readings.
OPERATING LOG SHEET
A permanent daily record of system operating conditions
(temperatures and pressures) recorded at regular intervals
throughout each 24 hour operating period should be kept.
Automatic data logging is possible by connecting the
optional printer and programming the DATA LOGGER func-
tion; Ref. Form 160.60-N2.
An accurate record of readings serves as a valuable ref-
erence for operating the system. Readings taken when a
system is newly installed will establish normal condi-
tions with which to compare later readings.
For example, dirty condenser tubes may be identified by
higher than normal temperature differences between leav-
ing condenser water and condenser saturation tempera-
ture.
OPERATING INSPECTIONS (See Section 2)
By following a regular inspection using the display read-
ings of the MicroComputer Control Center, and mainte-
nance procedure, the operator will avoid serious operat-
ing difficulty. The following list of inspections and proce-
dures should be used as a guide.