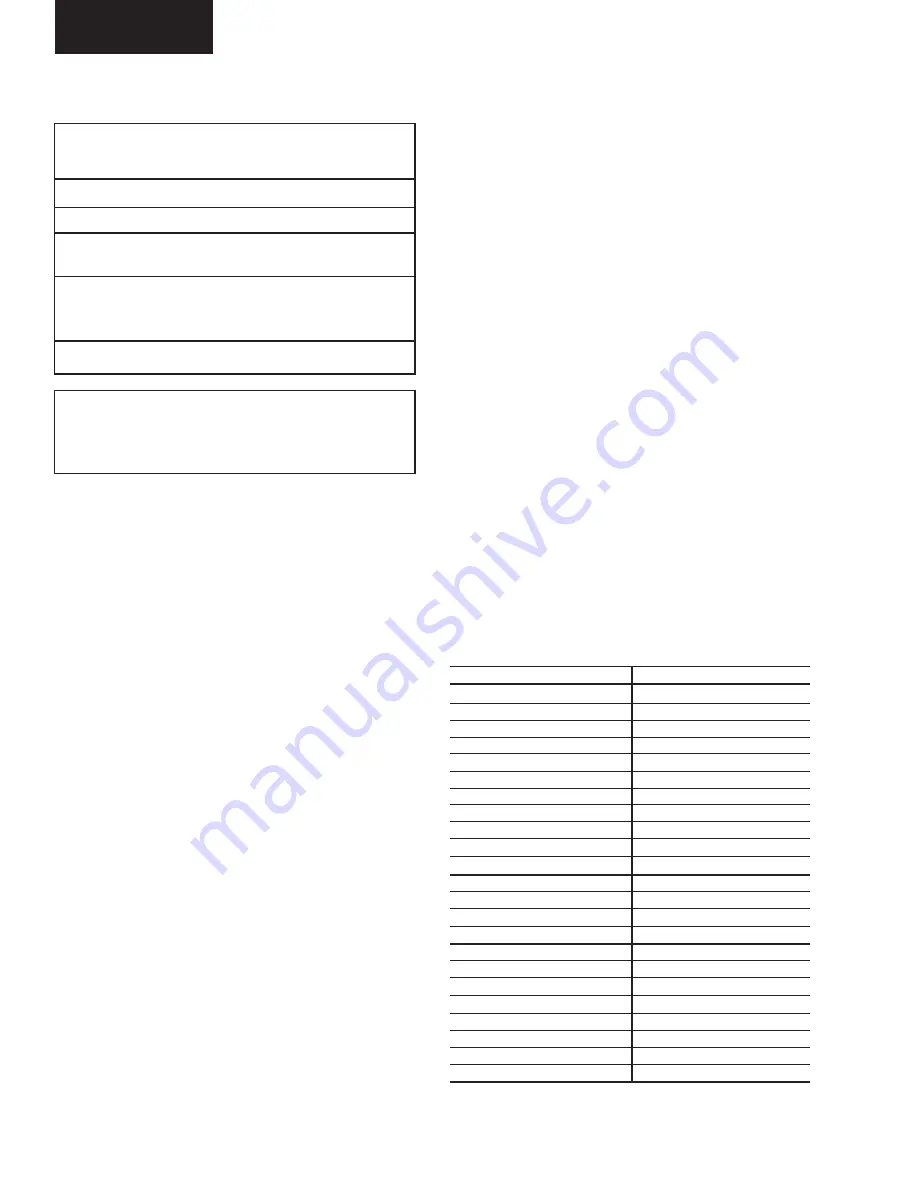
YORK INTERNATIONAL
92
PRE-STARTUP CHECKLIST
G
12. Be certain field wiring for discharge air sensor,
liquid line solenoid valves, and zone thermostats
(if applicable) and air proving switches have been
correctly wired.
PANEL CHECKS
(Power ON – Both Unit Switch OFF)
G
1. Apply 3-phase power and verify its value. Volt-
age imbalance should be no more than 2% of
the average voltage.
G
2. Apply 120VAC and verify its value on the termi-
nal block in the Power Panel. Make the measure-
ment between terminals 5 and 2 of CTB2. The
voltage should be /- 10%.
G
3. Program/verify the Cooling Setpoints, Program
Setpoints, and unit Options. Record the values
below (see sections on Setpoints and Unit keys
for programming instruction).
G
4. Put the unit into Service Mode (as described un-
der the Control Service And Troubleshooting sec-
tion) and cycle each condenser fan to ensure
proper rotation.
JOB NAME: ______________________________
SALES ORDER #: _________________________
LOCATION: _______________________________
SOLD BY: ________________________________
INSTALLING
CONTRACTOR: ___________________________
START-UP
TECHNICIAN/
COMPANY: _______________________________
START-UP DATE : _________________________
UNIT MODEL #:
____________________________
SERIAL #: ________________________________
CHECKING THE SYSTEM
PRIOR TO INITIAL START (No Power)
Unit Checks
G
1. Inspect the unit for shipping or installation
damage.
G
2. Assure that all piping has been completed.
G
3. Visually check for refrigerant piping leaks.
G
4. Open suction line ball valve, discharge line ball
valve, and liquid line valve for each system.
G
5. The compressor oil level should be maintained
so that an oil level is visible in the sight glass.
The oil level can only be tested when the com-
pressor is running in stabilized conditions, guar-
anteeing that there is no liquid refrigerant in the
lower shell of the compressor. In this case, the
oil must be between 1/4 and 3/4 in the sight glass.
At shutdown, the oil level can fall to the bottom
limit of the oil sight glass.
G
6. Verify proper CFM of air across evaporator coil.
Verify air flow switch operation.
G
7. Check the control panel to assure it is free of
foreign material (wires, metal chips, etc.).
G
8. Visually inspect wiring (power and control). Wir-
ing MUST meet N.E.C. and local codes.
G
9. Check tightness of power wiring inside the power
panel on both sides of the motor contactors.
G
10. Check for proper size fuses in main and control
circuits.
G
11. Assure 120VAC Control Power to CTB2 has 15
A minimum capacity.
See Table 7.
OPTIONS
Display Language
Sys 1 Switch
Sys 2 Switch
Unit Type
Ambient Control
Local/ Remote Mode
Control Mode
Display Units
Lead/Lag Control
Fan Control
Manual Override
COOLING SETPOINTS
Cooling Setpoint
Range
EMS-PWM Max. Setpoint
PROGRAM
Discharge Pressure Cutout
Suct. Pressure Cutout
Low Amb. Temp. Cutout
Anti-Recycle Time
Fan Control On-Pressure
Fan Differential Off-Pressure
Total # of Compressors
TABLE 10 – SETPOINT ENTRY LIST
Initial Startup
Содержание MILLENNIUM YCUL0016SC
Страница 35: ...YORK INTERNATIONAL FORM 150 63 NM1 35 This page is intentionally left blank 1 ...
Страница 151: ...YORK INTERNATIONAL FORM 150 63 NM1 151 This page is intentionally left blank 5 ...
Страница 152: ...YORK INTERNATIONAL 152 FIG 17 ELEMENTARY DIAGRAM MODELYCUL0040 ELEMENTARY DIAGRAM YCUL0040 Elementary Diagrams ...
Страница 155: ...YORK INTERNATIONAL FORM 150 63 NM1 155 This page is intentionally left blank 5 ...
Страница 159: ...YORK INTERNATIONAL FORM 150 63 NM1 159 This page is intentionally left blank 5 ...
Страница 163: ...YORK INTERNATIONAL FORM 150 63 NM1 163 This page is intentionally left blank 5 ...
Страница 170: ...YORK INTERNATIONAL 170 ...