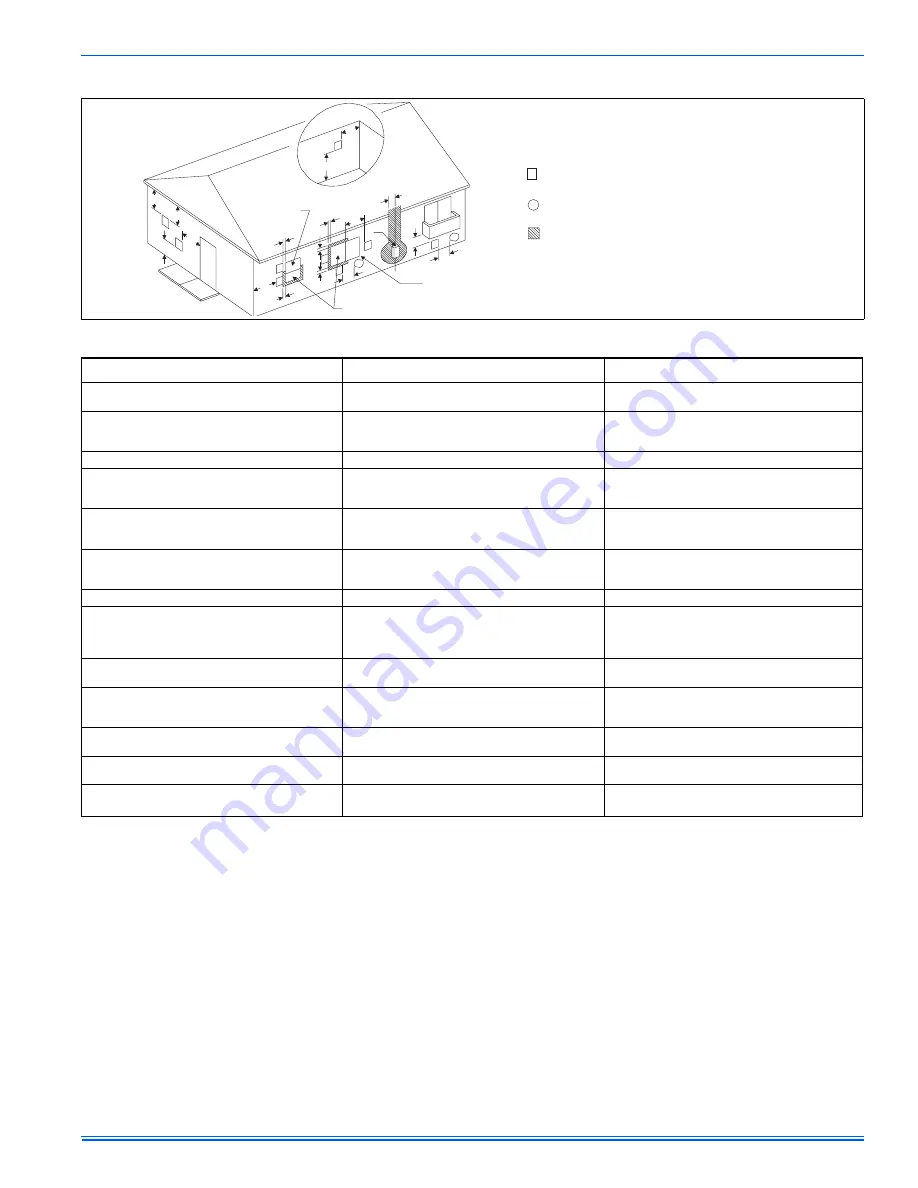
268890-UIM-B-0607
Unitary Products Group
17
VENT CLEARANCES
†
A vent shall not terminate directly above a sidewalk or paved driveway that is located between two single family dwellings and serves both dwellings.
††
12 inches (30 cm) up from the bottom edge of the structure for Two-pipe (direct vent) applications per ANSI Z223.1 / NFPA 54, National Gas Code.
‡
Permitted only if veranda, porch, deck, or balcony is fully open on a minimum of two sides beneath the floor and the distance between the top of the vent termina-
tion and the underside of the veranda, porch, or deck is greater than 1 foot (30 cm) as specified in CSA B149.1-00.
A vent shall not terminate less than 1 foot (30 cm) above a grade level.
Any fresh air or make up inlet for dryer or furnace area is considered to be forced air inlet.
Avoid areas where condensate drippage may cause problems such as above planters, patios, or adjacent to windows where steam may cause fogging.
A terminus of a vent shall be fitted with a cap in accordance with the vent manufacturer’s installation instructions, or in accordance with the installation instructions for a
special venting system.
IMPORTANT: Consideration must be given for degradation of building materials by flue gases. Sidewall termination may require sealing or shielding of building surfaces
with a corrosion resistant material to protect against combustion product corrosion. Consideration must be given to wind direction in order to prevent flue products and/or
condensate from being blown against the building surfaces. If a metal shield is used it must be a stainless steel material at a minimum dimension of 20 inches. It is rec-
ommended that a retaining type collar be used that is attached to the building surface to prevent movement of the vent pipe.
Responsibility for the provision of proper adequate venting and air supply for application shall rest with the installer.
Vent shall extend high enough above building, or a neighboring obstruction, so that wind from any direction will not create a positive pressure in the vicinity of the vent.
FIGURE 17:
Home Layout
L
E
D
B
V
V
V
X
V
B
V
J
X
B
B
B
V
V
F
V
C
B
X
V
I
V
G
H
A
M
K
OPERABLE
FIXED
CLOSED
VENT TERMINAL
AIR SUPPLY
AREA WHERE TERMINAL IS NOT PERMITTED
FIXED
CLOSED
Direct Vent Terminal Clearances
Canadian Installations
1,3
US Installation
2,3
A. Clearance above grade, veranda, porch, deck, or
balcony
12 inches (30 cm)
12 inches (30 cm)
B. Clearance to window or door that may be opened
12 inches (30 cm) for models
≤
100,000 BTUH (30 kW),
36 inches (91 cm) for models >100,000 BTUH (30 kW)
Two-pipe (direct vent) applications: 9 inches (23 cm)
for models
≤
50,000 BTUH (15 kW), 12 inches (30 cm)
for models >50,000 BTUH (15 kW). ††
C. Clearance to permanently closed window
12 inches (30 cm)
12 inches (30 cm)
D. Vertical clearance to ventilated soffit located
above the terminal within a horizontal distance
of 2 feet (61 cm) from the center line of the terminal
12 inches (30 cm) or in accordance with local
installation codes and the requirements of the gas
supplier.
12 inches (30 cm) or in accordance with local
installation codes and the requirements of the gas sup-
plier
E. Clearance to unventilated soffit
12 inches (30 cm) or in accordance with local
installation codes and the requirements of the gas
supplier
12 inches (30 cm) or in accordance with local
installation codes and the requirements of the gas
supplier
F. Clearance to outside corner
12 inches (30 cm) or in accordance with local
installation codes and the requirements of the gas
supplier
12 inches (30 cm) or in accordance with local
installation codes and the requirements of the gas
supplier
G. Clearance to inside corner
3 feet (91 cm)
3 feet (91 cm)
H. Clearance to each side of center line
extended above meter/regulator assembly
Above a meter/regulator assembly within 3 feet (91 cm)
horizontally of the vertical center-line of the regulator
vent outlet to a maximum vertical distance of 15 feet
(4.5 cm) above the meter/regulator assembly.
Above a meter/regulator assembly within 3 feet (91
cm) horizontally of the vertical center-line of the regula-
tor vent outlet to a maximum vertical distance of 15
feet (4.5 cm) above the meter/regulator assembly.
I.
Clearance to service regulator vent outlet
3 feet (91 cm)
3 feet (91 cm) or in accordance with local installation
codes and the requirements of the gas supplier.
J. Clearance to nonmechanical air supply inlet to
building or the combustion air inlet to any other
appliance
12 inches (30 cm) for models
≤
100,000 BTUH (30 kW),
36 inches (91 cm) for models >100,000 BTUH (30 kW)
Two-pipe (direct vent) applications: 9 inches (23 cm)
for models
≤
50,000 BTUH (15 kW), 12 inches (30 cm)
for models >50,000 BTUH (15 kW).
K. Clearance to a mechanical supply inlet
6 feet (1.83 m)
3 feet (91 cm) above if within 10 feet (3 cm)
horizontally
L. Clearance above paved sidewalk or paved
driveway located on public property
7 feet (2.13 m)†
7 feet (2.13 m) or in accordance with local installation
codes and the requirements of the gas supplier.
M. Clearance under veranda, porch, deck, or balcony
12 inches (30 cm)‡
12 inches (30 cm) or in accordance with local installa-
tion codes and the requirements of the gas supplier
.
1.
In accordance with the current CSA B149.1-00, Natural Gas and Propane Installation Code.
2.
In accordance with the current ANSI Z223.1 / NFPA 54, National Gas Code.
3.
In accordance with the current ANSI Z21.47 * CSA 2.3 American National Standard.