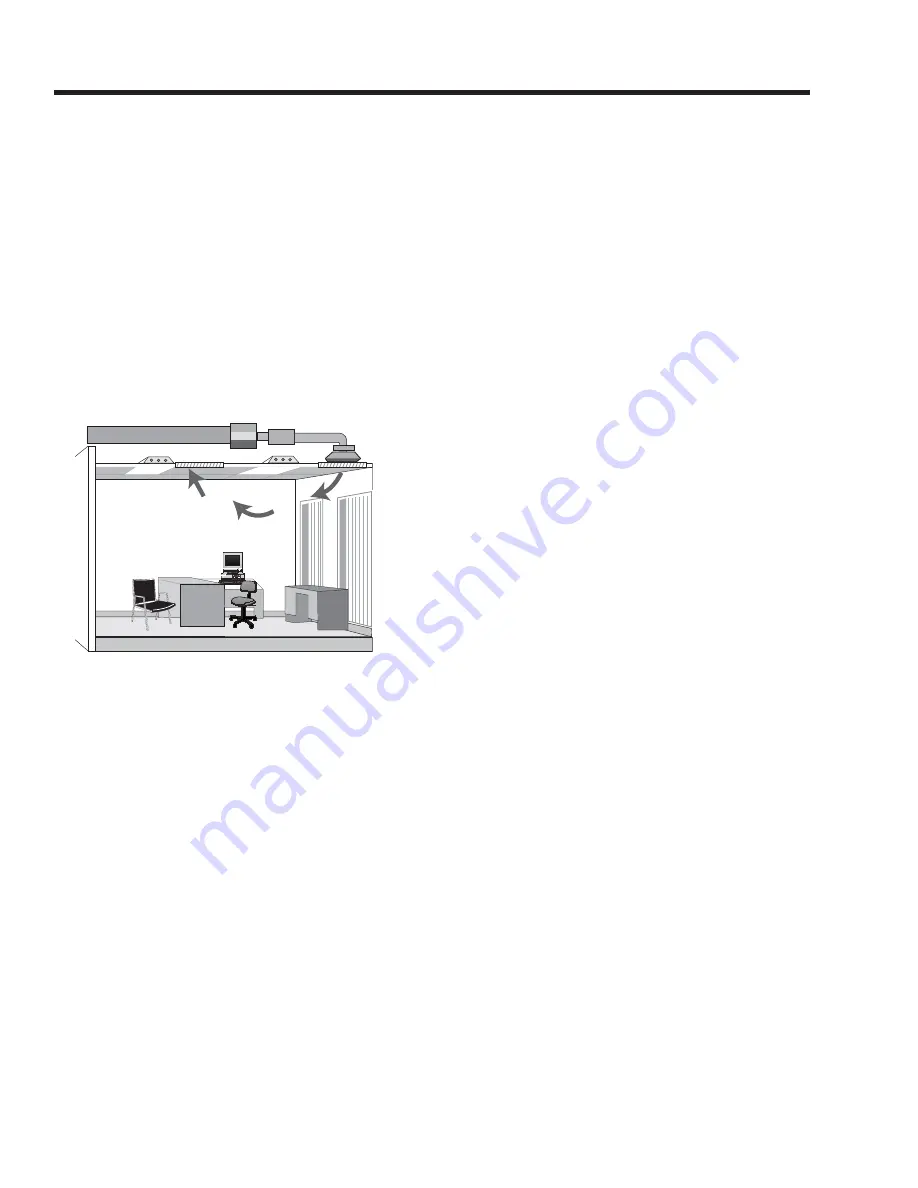
JOHNSON CONTROLS
10
FORM 100.50-EG5 (108)
Application Data
(continued)
VAV SUPPLY AIR PRESSURE CONTROL
Traditional packaged rooftop systems use inlet guide
vanes (IGVs) for duct static pressure control. These
control supply duct pressure by modulating dampers
(introducing losses and ineffi ciencies) on the inlet of the
fan, open and closed. YORK’s variable frequency drives
(VFDs) offer superior fan speed control and quieter,
energy effi cient operation.
For VAV applications, the YORK Eco
2
unit uses a VFD
to modulate fan speed and maintain a constant duct
static pressure. VFDs offer superior control over the
operation of the unit at part load, and offer the additional
benefi ts of quieter and more effi cient operation when
compared to IGV.
HARSH ENVIRONMENTS – CONDENSER AND
EVAPORATOR COIL PROTECTION
For harsh environmental conditions such as seashore
applications, YORK offers three types of coil protection:
copper fi n material, black fi n and Technicoat coatings.
YORK recommends that for corrosive environments that
copper fi ns be used to protect the evaporator and/or
condenser coils. In areas where chemicals that can
corrode copper are present, such as ammonia, YORK
recommends that the black fi n or Technicoat coating be
used for maximum protection.
•
Copper-Fin Evaporator and Condenser Coil
– Copper fi ns can be used instead of aluminum for
additional corrosion protection. However, it is not
suitable for areas that are subject to acid rain or
exposed to ammonia.
•
Pre-Coated Condenser Fins
– Black fi n coating
(yellow fi n for evaporator fi ns) is pre-coated appli-
cation epoxy on aluminum fi n stock to guard from
corrosive agents and insulate against galvanic
potential. It is used for mild seashore or industrial
locations. This can provide corrosion resistance
comparable to copper fi n coils in typical seashore
locations.
•
Post-Coated Condenser Fins
– Technicoat (a
post-coated application of epoxy) can be used for
seashore and other corrosive applications with the
exception of strong alkaloides, oxidizers, wet bro-
mide, chlorine and fl uorine in concentrations greater
than 100 ppm. Any of the above suitable options
should be selected based on the particular project
design parameters and related environmental fac-
tors. The application should be further reviewed and
approved by the consulting engineer or owner based
on their knowledge of the job site conditions.
BUILDING PRESSURE CONTROL SYSTEMS
Building pressure control systems are often neces-
sary when economizers are used to bring in outdoor
air. Without proper building exhaust, the building may
become over pressurized. The pressure control system
maintains the proper building pressure by expelling the
appropriate amount of air from the building.
Exhaust/relief fans
– In this application, a powered
exhaust fan may be suitable, however careful consid-
eration of the fan type is necessary. YORK offers a
centrifugal powered exhaust fan to perform this function.
Some manufacturers use a propeller exhaust fan, which
cannot handle the static pressure requirements.
For systems with moderate to low return static pressure,
an exhaust fan is recommended. The benefi t of the ex-
haust fan is that it does not run all of the time, and may
facilitate compliance with the ASHRAE 90.1 fan motor
horsepower requirement.
The exhaust fan operates in parallel with the supply
fan. In this arrangement, the supply fan handles the full
static pressure requirements of the system. For normal
building pressure control, the exhaust fan operates to
draw air from the return plenum and exhaust it out of
the building.
The exhaust fan confi guration is available in two forms,
modulating and non-modulating. Modulating is the most
common and recommended for the majority of applica-
tions, while non-modulating should be used with in only
certain circumstances.
In the modulating exhaust system, the volume of airfl ow
exhausted from the building is proportional to the enter-
ing volume of outside air. Control is accomplished via
either a discharge damper or a variable-frequencydrive
(VFD). YORK recommends the use of a VFD to reduce
energy consumption, sound levels and improved reli-
ability due to fewer moving parts.
FIG. 1.
TRADITIONAL OVERHEAD VAV AIR
DELIVERY SYSTEM