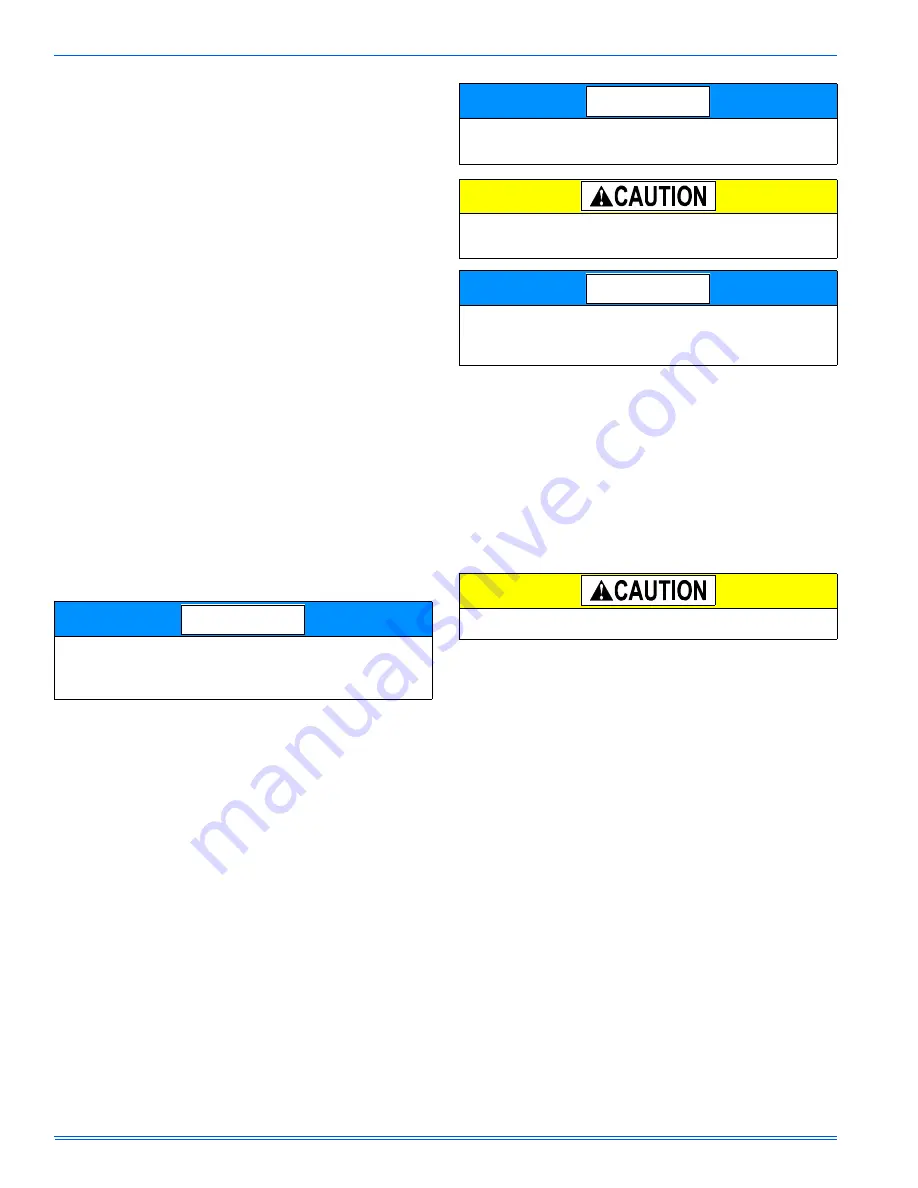
987158-UIM-B-1013
24
Johnson Controls Unitary Products
SETUP TEST MODE
During normal operation, the furnace input rate can vary between 50%
and 100% of full nameplate input, making it difficult to check for proper
operation. To help with the furnace startup process, the control has a
TEST MODE available that allows the furnace input rate to stay at a
constant input rate. To access this TEST MODE perform the following
sequence:
1. With power to the board on and with no thermostat calls (no call for
heating, cooling or continuous fan), push and hold the TEST button
on the board for one second. The LED on the board will glow red.
2. Release the TEST button. The LED on the board will flash a rapid
green signal, indicating that TEST MODE is activated.
3. Turn the thermostat to call for heat (R & W signal).
4. The furnace will light and operate at high (100%) firing rate. The fur-
nace firing rate should be checked at this level to confirm that the
furnace is not overfired or underfired.
5. To run the furnace at minimum rate (50%), press the ERROR button
once. The LED will flash one green flash to confirm.
6. To run the furnace at a middle rate (70%), press the ERROR button
twice within a five-second period. The LED will flash green two times
to confirm.
7. To again operate the furnace at maximum (100%) rate, press the
ERROR button three times within a five-second period. The LED will
flash green three times to confirm.
8. If the thermostat call for heat is removed, the LED will flash a rapid
green signal, indicating that the furnace is still in TEST MODE.
9. When startup tests are completed, turning off power to the board will
take the furnace out of TEST MODE and will restore normal opera-
tion. The furnace will automatically return to normal operation after
150 minutes if power is not cycled.
CALCULATING THE FURNACE INPUT
(NATURAL GAS)
Verify natural gas input rate by clocking meter.
1. Turn off all other gas appliances and pilots.
2. Run furnace for a minimum of 3 minutes in heating operation.
3. Measure time (in sec) for gas meter to complete 1 revolution and
note reading. The 2 cubic feet dial provides a more accurate mea-
surement of gas flow.
4. Refer to Table 10 for cubic feet of gas per hour.
5. Multiply cubic feet per hour by heating valve (BTU/cu ft) to obtain
input.
If clocked rate does not match the input rate from the unit nameplate.
follow steps in next section to adjust the manifold pressure. Repeat
steps 2 - 5 until correct input is achieved.
HIGH ALTITUDE NATURAL GAS ORIFICE
CONVERSION
The National Fuel Gas Code requires that gas appliances installed
above 2,000 feet elevation have their inputs de-rated by 4% per 1,000
feet above sea level. The modulating furnaces automatically de-rate for
altitude by measuring the inducer blower pressure and using that to
determine if there is adequate air to support good combustion. If there
is not enough combustion air to properly support 100% of the furnace
nameplate input rate, the control will reduce the input to the point that
there will be good combustion.
Burner orifices are sized to provide proper input rate using natural
gas with a heating value of 1030 BTU/Ft
3
(38.4 MJ/m
3
). If the heating
value of your gas is significantly different, it may be necessary to
replace the orifices.
NOTICE
DO NOT set manifold pressure less than 3.2 in wc or more than 3.8 in
wc for natural gas at sea level. If manifold pressure is outside this
range, change main burner orifices.
DO NOT bottom out gas valve regulator adjusting screw. This can
result in unregulated manifold pressure and result in excess overfire
and heat exchanger failures.
If orifice hole appears damaged or it is suspected to have been
redrilled, check orifice hole with a numbered drill bit of correct size.
Never redrill an orifice. A burr-free and squarely aligned orifice hole is
essential for proper flame characteristics.
Be sure to relight any gas appliances that were turned off at the start
of this input check.
NOTICE
NOTICE