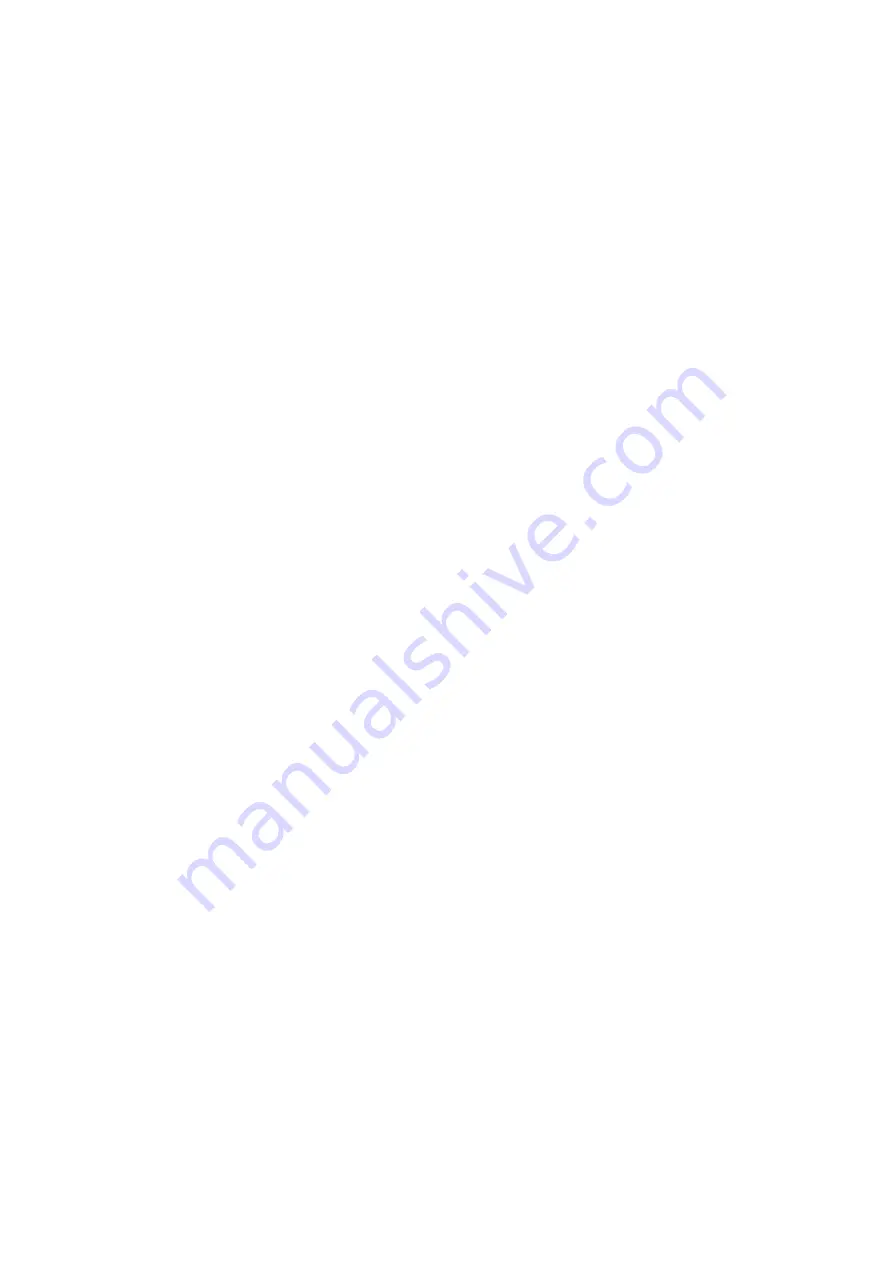
10. Instructions for service technicians cont.
Leak detection fluids are suitable for use with most refrigerants, but avoid using detergents that contain chlorine, which can react with the refrigerant to corrode
copper pipes.
If a leak is suspected, remove/extinguish all naked flames. If brazing is required when a leak is detected, completely recover the refrigerant from the system or isolate
(using shut-off valves) the part of the system away from the leak. For units containing flammable refrigerants, purge the system with oxygen-free nitrogen (OFN)
before and during the brazing process.
15. Removing and emptying
Standard procedures should be followed when opening the refrigerant circuit for repair or any other purpose. In the case of flammable refrigerants, it is important to
take special care due to the risk of ignition. Follow the procedure below:
• remove the refrigerant;
• purge the system with inert gas;
• empty;
• purge with inert gas again;
• open the system by cutting or brazing.
The refrigerant must be recovered in suitable cylinders. To ensure equipment safety, flush the system with OFN (Oxygen Free Nitrogen). The procedure needs to be
repeated several times. Do not use compressed air or oxygen for this purpose.
Purge should be carried out by breaking the vacuum in the system with OFN (oxygen-free nitrogen) and continue filling until working pressure is reached, venting to
atmosphere and finally lowering to vacuum. The process must be repeated until the system is completely empty of refrigerant.
After the last dose of OFN (oxygen-free nitrogen) has been applied, the system must be purged to atmospheric pressure to allow work to be done. This step is
essential if you will be brazing the tubing.
Make sure that the outlet of the vacuum pump is away from sources of ignition and that the environment is adequately ventilated.
16. Refrigerant charge procedures
In addition to standard filling procedures, the following requirements must be followed.
• Ensure that there is no contamination with various refrigerants when using the filling equipment. Keep hoses and lines as short as possible to minimize the amount
of refrigerant they contain.
• Keep the cylinder in an upright position.
• Before charging the system with refrigerant, make sure that the refrigeration system is grounded.
• Label the installation after filling (if not already done).
• Be careful not to overcharge the system with refrigerant.
• Pressure test with oxygen-free nitrogen before refilling the system. The system should be checked for leaks after filling is complete but before commissioning.
Perform the sealing procedure again before leaving the installation site.
17. Decommissioning
Before performing this procedure, make sure that the technician is thoroughly familiar with the device and all its details. Safe recovery of the refrigerant is
recommended. An oil and refrigerant sample should be taken prior to the task in case analysis is required before reusing the reclaimed refrigerant. Make sure that
electrical power is available before carrying out the task.
a. Familiarize yourself with the device and how to use it.
b. Electrically isolate the system.
c. Before performing the procedure, ensure that:
- Mechanical refrigerant cylinder handling equipment is available;
- Personal protective equipment is available and properly used;
- The recovery process is constantly supervised by a competent person;
- The equipment and the recovery cylinder comply with the relevant standards.
d. Drain the refrigeration system if possible.
e. If a vacuum cannot be achieved, a manifold must be made to allow the refrigerant to be drained from various parts of the system.
f. Make sure the cylinder is on the scale before starting recovery.
g. Operate and operate the recovery equipment in accordance with the manufacturer's instructions.
h. Do not overfill the cylinder. (Do not fill over 80% of the fill volume).
i. Do not exceed the cylinder's maximum working pressure, even temporarily.
j. After the cylinders are properly filled and the procedure is complete, ensure that the cylinders and equipment are immediately removed from the work area and all
shut-off valves on the equipment are closed.
k. Reclaimed refrigerant may only be charged to another system after it has been cleaned and inspected.
18. Labeling
Equipment must be labeled that it has been decommissioned and emptied of refrigerant. The label must be dated and signed. Make sure there is a label on the unit
that there is flammable refrigerant inside.
19. Recovery
• When removing refrigerant from the system for service or decommissioning, good practice is recommended to ensure that all refrigerant is safely recovered.
• When transferring refrigerant to cylinders, ensure that only appropriate cylinders are used. Make sure there are enough of them available to recover refrigerant from
the entire system. All cylinders used should be dedicated to reclaimed refrigerant and properly marked (special refrigerant recovery cylinders). Cylinders should be
complete with safety valve and shut-off valves in good technical condition.
• Empty recovery cylinders are vented and, if possible, cooled before recovery begins.
• Recovery equipment should be in good working order, complete with instructions and designed to recover all relevant refrigerants, including flammable refrigerants
where applicable. In addition, an available set of operational, properly calibrated scales is required.
• Hoses should be in good technical condition and equipped with tight joints. Before using recovery equipment, ensure that it is in good working order and has been
well maintained and that all associated components are insulated to prevent ignition in the event of a refrigerant leak. If in doubt, consult the manufacturer.
• The recovered refrigerant must be returned to the supplier in the appropriate cylinder with the appropriate waste transfer document. Do not mix different refrigerants
in recovery equipment, especially in cylinders.
• If it is necessary to remove the compressor or its oil, ensure that they have been drained to an acceptable level to ensure that refrigerant residues are not in the
lubricant.
The draining procedure must be performed before the compressor is delivered to the supplier. The process can be accelerated by heating the compressor body.
Remove the oil from the system safely.