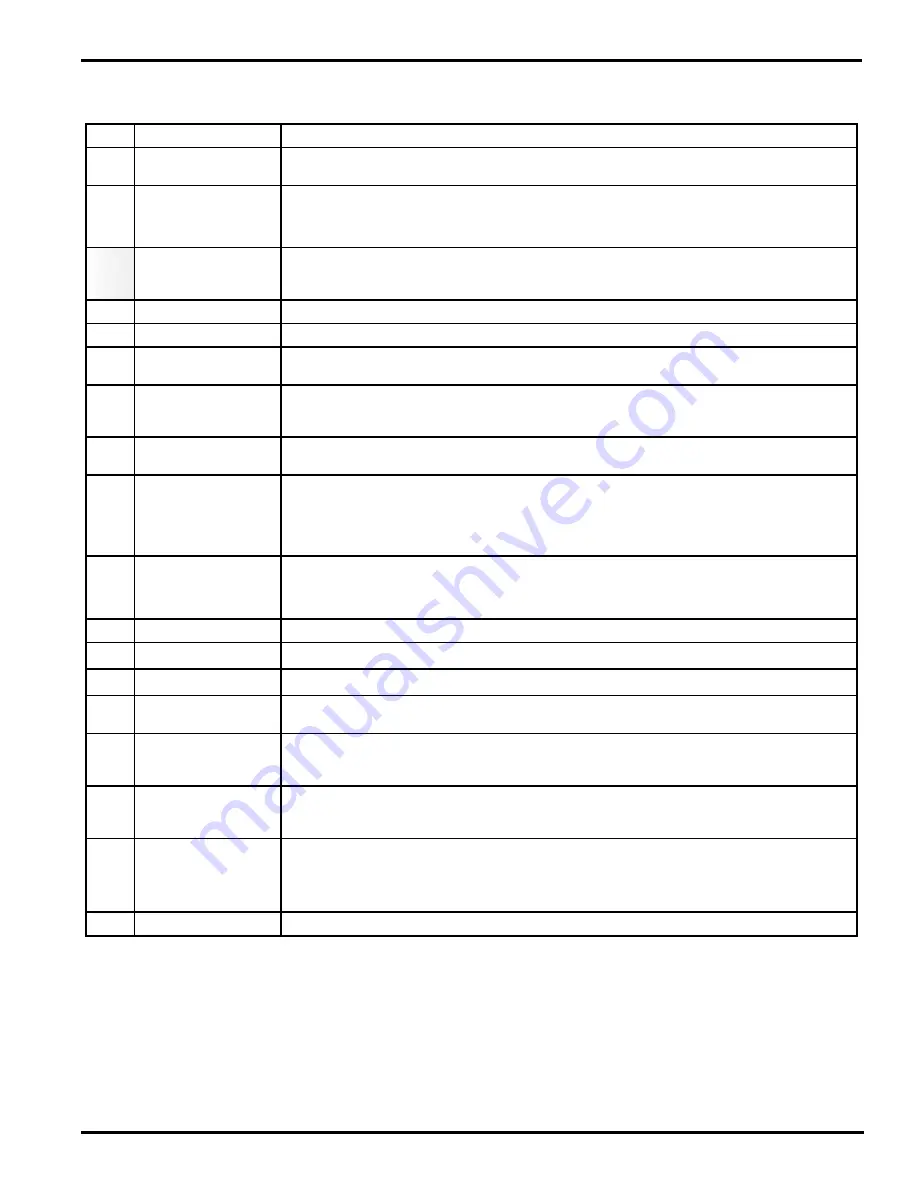
IM 11Y01B02-01E-A 3rd Edition June 19, 2012-00
<1 QUICk START> 1-2
4.2
Leak-check all connections and ensure pressure ratings are not exceeded!
5.0
Power-Up
Make sure the power module door is closed. Do not open this door when the analyzer is powered. Apply
the AC power to the analyzer.
5.1
Open the Control module door. Inside this module use the internal On-Off switch to power-up the ana-
lyzer (located lower right hand side).
5.2
Observe the various LED clusters on the backplane and FPGA boards.
All blue LEDs located lower right side on the back-plane should be on.
5.3
Observe the Green power indicator on the SBC.
5.4
Observe the LEDs on the optional analog I/O board.
6.0
Checking
If there is an installed optional 6.5” Display and Keypad – Observe the Main Menu messages and status
information.
6.1
If there is no installed User Interface, then connect a laptop PC via Ethernet to the SBC mounted on the
backplane. Initiate the supplied UltraVNC software from the laptop to initiate a VNC session with the
‘blind’ analyzer and observe the analyzer Main Menu via the laptop.
6.2
AT this time there may be alarm or warning messages due to low transmission, out of range
parameters or other – final system configuration is still required!
6.3
If the analyzer displays a Warning “Validation Required” then this indicates that there is no target gas
absorption peak found at start-up. Either, shut down the analyzer, introduce some measured gas into the
flow cell and re-start, or perform a validation. This will ensure that the analyzer is correctly tuned to the
measurement gas absorption peak. If this Warning cannot be cleared by either method, please contact
Yokogawa Laser Analysis Division or your local agent for further assistance.
7.0
Configure
BASIC
By way of the appropriate user interface, the correct process parameters and other parameters can now
be entered.
7.1
Enter the Basic Menu and go to Configure.
7.2
Gas Pressure
Enter in the correct process gas pressure (if Active, see Advanced Configure).
7.3
Gas Temperature
Enter in the correct process gas temperature (if Active, see Advanced Configure).
7.4
If any other parameters are required to be set (such as analog I/O ranges, alarms levels, Auto Validation
sequences) then the Advanced Menu needs to be accessed.
Advanced Menu access is Password protected (default 1234, can be changed by user if neces-
sary) and should only be used by skilled and trained persons - Contact Yokogawa Laser Analysis
Division or Local Agent if any doubts!
Go to the Data section under Basic and configure the appropriate ‘Record Result Data’ settings. This will
ensure the analyzer stores important information during operation that may be used to verify operation/
status/diagnostics and other trouble shooting.
8.0
Configure
ADVANCED
Using the correct password (Default 1234), enter in to the Advanced Menu, then the Configure.
8.1
Select the desired measurement units for path length, pressure and temperature.