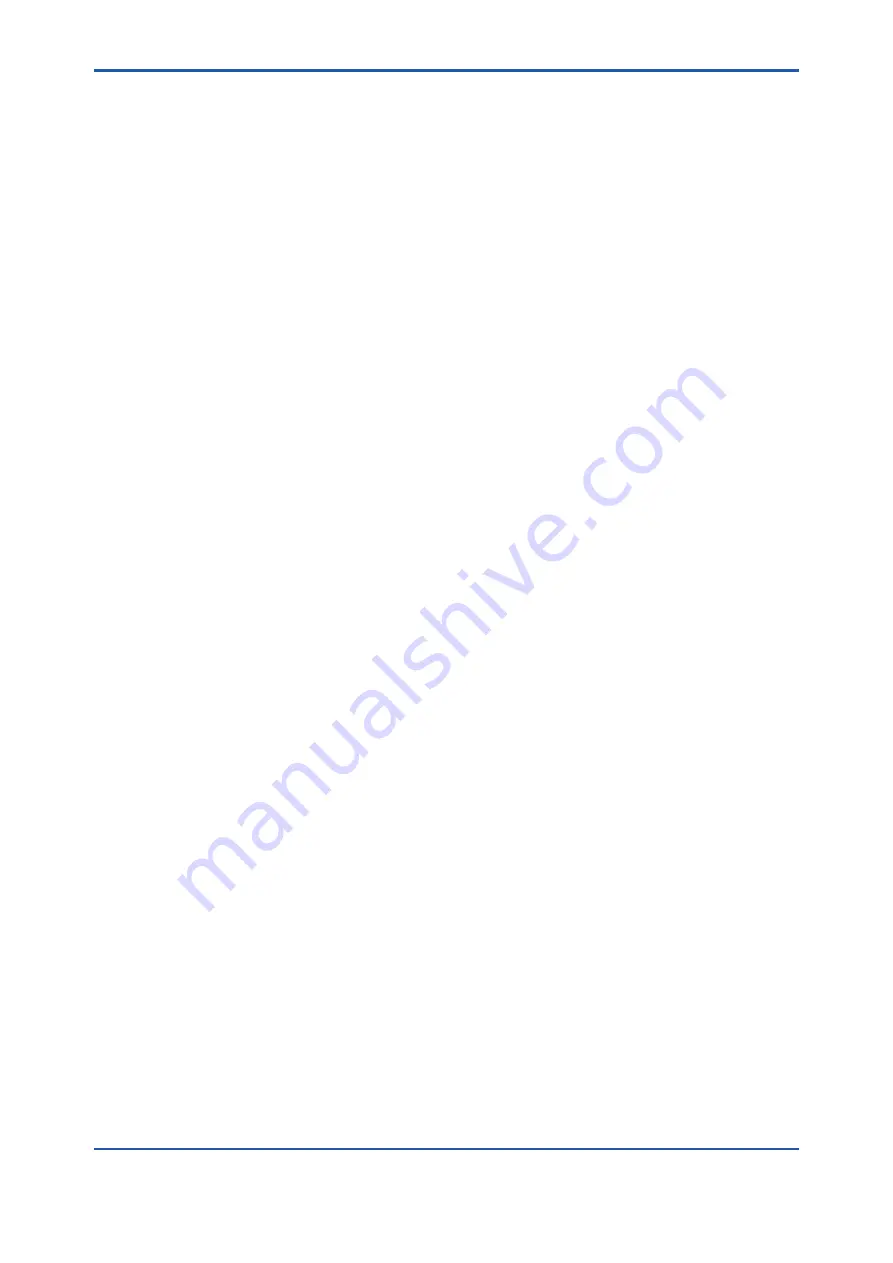
<8. Maintenance>
8-11
IM 12F4A1-01E
14th Edition : Jul. 15, 2020
l
Replacement Procedure
After drive belt replacement, the tension should be adjusted. Without tension adjustment,
negative effects, such as shorter life of the drive belt, may result. Tension adjustment is relatively
time-consuming, so it is recommended that the drive belt be replaced in time with other
maintenance work such as replacement of driven shift assembly or motor assembly unless
replacement is urgently needed, i.e., if the drive belt causes abnormal operation of the electrode
mechanism block. For drive belt replacement, refer to Items (14) and (15) in subsection 8.10.3.
8.10.3
Inspection, Maintenance and Replacement of Driven
Shaft Assembly
l
Inspection and Maintenance Procedure
With the electrode mechanism block working at the time of, for example, zero calibration, the
following inspections should be conducted. The recommended interval is three month.
• Check for abnormal sounds: loud sound, resonant sound or discontinuous sound. If
abnormal sound occurs, defect bearings in the driven shaft assembly are likely. (Other
causes, such as a defect in the motor, are also likely.) Stop the operation of the electrode
mechanism block and check for friction in the driven shaft. (Refer to the instructions
described below in biannual inspections.)
• Check for vibration of the driven shaft and indicator electrode. If vibration occurs, wear of
bearings in the driven shaft assembly are most likely. Stop the operation of the electrode
mechanism block and check for looseness between the driven shaft and the bearings.
(Refer to the instructions described below in biannual inspections.)
The following inspection should be performed approximately every six months. Stop the
operation of the electrode mechanism block for the inspection.
• Turn the driven shaft by hand and check to ensure smooth rotation without looseness. If
looseness occurs, if the driven shaft does not rotated by inertial force with the drive belt
removed, or if friction sound is heard, immediately replace the driven shaft assembly.
l
Replacement Procedure
If failure of bearings occurs, the whole driven shaft assembly, including the bearings, should be
replaced. The replacement, in principle, should be conducted by Yokogawa’s service person.
The replacement procedure is described below just in case the replacement is conducted by the
user. Steps (1) to (9) are a disassembly procedure and steps (10) and the following steps are an
assembly procedure.
(1) Shut off the power fed to the RC400G, then place the electrode mechanism block in the
maintenance position then remove the cover (see Figure 4.7).
(2) Remove indicator electrode and counter electrode.
To remove the indicator electrode, inset the supplied hex key wrench into the socket of the
driven shaft, to stop it from rotating.
Disconnect the three wires connected to the counter electrode, next loosen and remove the
clamp holding the electrode in its holder.
(3) Remove the drive belt together with the pulleys for the driven and drive shafts.
(4) Remove the rotating contact from the driven shaft.
(5) Remove the plate installed to prevent drive belt shavings to enter the electrode holder in the
driven shaft assembly by loosening the 2 screws.
(6) Remove two plates which holds driven shaft assembly in place.
(7) If driven shaft assembly is bad, remove it from motor mounting plate. The place where the
electrode holder base is inserted contains an O-ring. This O-ring and the counter electrode
fixing clamp can be reused.
Содержание RC400G
Страница 5: ...Blank Page ...
Страница 9: ...Blank Page ...
Страница 25: ...Blank Page ...
Страница 41: ...Blank Page ...
Страница 95: ...Blank Page ...
Страница 139: ......