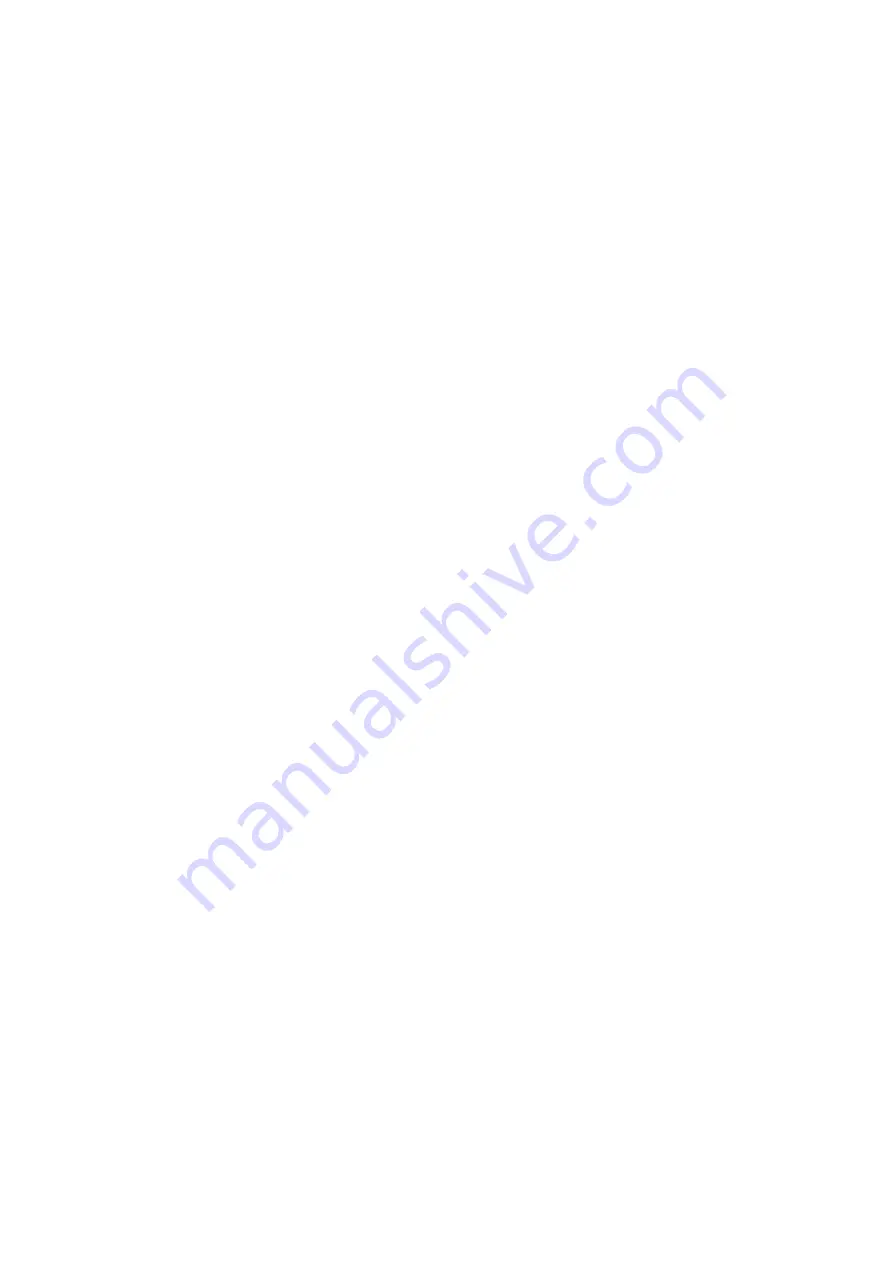
EX-B03E
2
INSTALLATION AND OPERATING PRECAUTIONS FOR TIIS FLAMEPROOF EQUIPMENT
4. Installation of Flameproof Ap-
paratus
(1) Installation Area
Flameproof apparatus may be installed, in accordance with
applicable gases, in a hazardous area in Zone 1 or 2, where
the specified gases are present. Those apparatus shall not be
installed in a hazardous area in Zone 0.
Note: Hazardous areas are classified in zones based upon the
frequency of the appearance and the duration of an explosive
gas atmosphere as follows:
Zone 0: An area in which an explosive gas atmosphere is
present continuously or is present for long periods.
Zone 1: An area in which an explosive gas atmosphere is
likely to occur in normal operation.
Zone 2: An area in which an explosive gas atmosphere is not
likely to occur in normal operation and if it does
occur it will exist for a short period only.
(2) Environmental Conditions
The standard environmental condition for the installation of
flameproof apparatus is limited to an ambient temperature
range from –20
°
C to +40
°
C (for products certified under
Technical Criteria). However, some field-mounted
instruments may be certified at an ambient temperature up to
+60
°
C as indicated on the instrument nameplates. If the
flameproof apparatus are exposed to direct sunshine or
radiant heat from plant facilities, appropriate thermal
protection measures shall be taken.
5. External Wiring for Flameproof
Apparatus
Flameproof apparatus require cable wiring or flameproof
metal conduits for their electrical connections. For cable
wiring, cable glands (cable entry devices for flameproof type)
to wiring connections shall be attached. For metal conduits,
attach sealing fittings as close to wiring connections as
possible and completely seal the apparatus. All non-live
metal parts such as the enclosure shall be securely grounded.
For details, see the “USER’S GUIDELINES for Electrical
Installations for Explosive Gas Atmospheres in General
Industry,” published in 1994.
(1) Cable Wiring
• For cable wiring, cable glands (cable entry devices for
flameproof type) specified or supplied with the apparatus
shall be directly attached to the wiring connections to
complete sealing of the apparatus.
• Screws that connect cable glands to the apparatus are
those for G-type parallel pipe threads (JIS B 0202) with
no sealing property. To protect the apparatus from
corrosive gases or moisture, apply nonhardening sealant
such as liquid gaskets to those threads for waterproofing.
• Specific cables shall be used as recommended by the
“USER’S GUIDELINES for Electrical Installations for
Explosive Gas Atmospheres in General Industry,”
published in 1994.
• In necessary, appropriate protective pipes (conduit or
flexible pipes), ducts or trays shall be used for
preventing the cable run (outside the cable glands) from
damage.
• To prevent explosive atmosphere from being propagated
form Zone 1 or 2 hazardous location to any different
location or non-hazardous location through the protective
pipe or duct, apply sealing of the protective pipes in the
vicinity of individual boundaries, or fill the ducts with
sand appropriately.
• When branch connections of cables, or cable connections
with insulated cables inside the conduit pipes are made,
a flameproof or increased-safety connection box shall be
used. In this case, flameproof or increased-safety cable
glands meeting the type of connection box must be used
for cable connections to the box.
(2) Flameproof Metal Conduit Wiring
• For the flameproof metal conduit wiring or insulated
wires shall be used as recommended by the USER’S
GUIDELINES for Electrical Installations for Explosive
Gas Atmospheres in General Industry, published in
1994.
• For conduit pipes, heavy-gauge steel conduits
conforming to JIS C 8305 Standard shall be used.
• Flameproof sealing fittings shall be used in the vicinity
of the wiring connections, and those fittings shall be
filled with sealing compounds to complete sealing of the
apparatus. In addition, to prevent explosive gases,
moisture, or flame caused by explosion form being
propagated through the conduit, always provide sealing
fittings to complete sealing of the conduit in the
following locations:
(a) In the boundaries between the hazardous and non-
hazardous locations.
(b) In the boundaries where there is a different
classification of hazardous location.
• For the connections of the apparatus with a conduit pipe
or its associated accessories, G-type parallel pipe threads
(JIS B 0202) shall be used to provide a minimum of
five-thread engagement to complete tightness. In
addition, since these parallel threads do not have sealing
property, nonhardening sealant such as liquid gaskets
shall thus be applied to those threads for ensuring
waterproofness.
• If metal conduits need flexibility, use flameproof flexible
fittings.