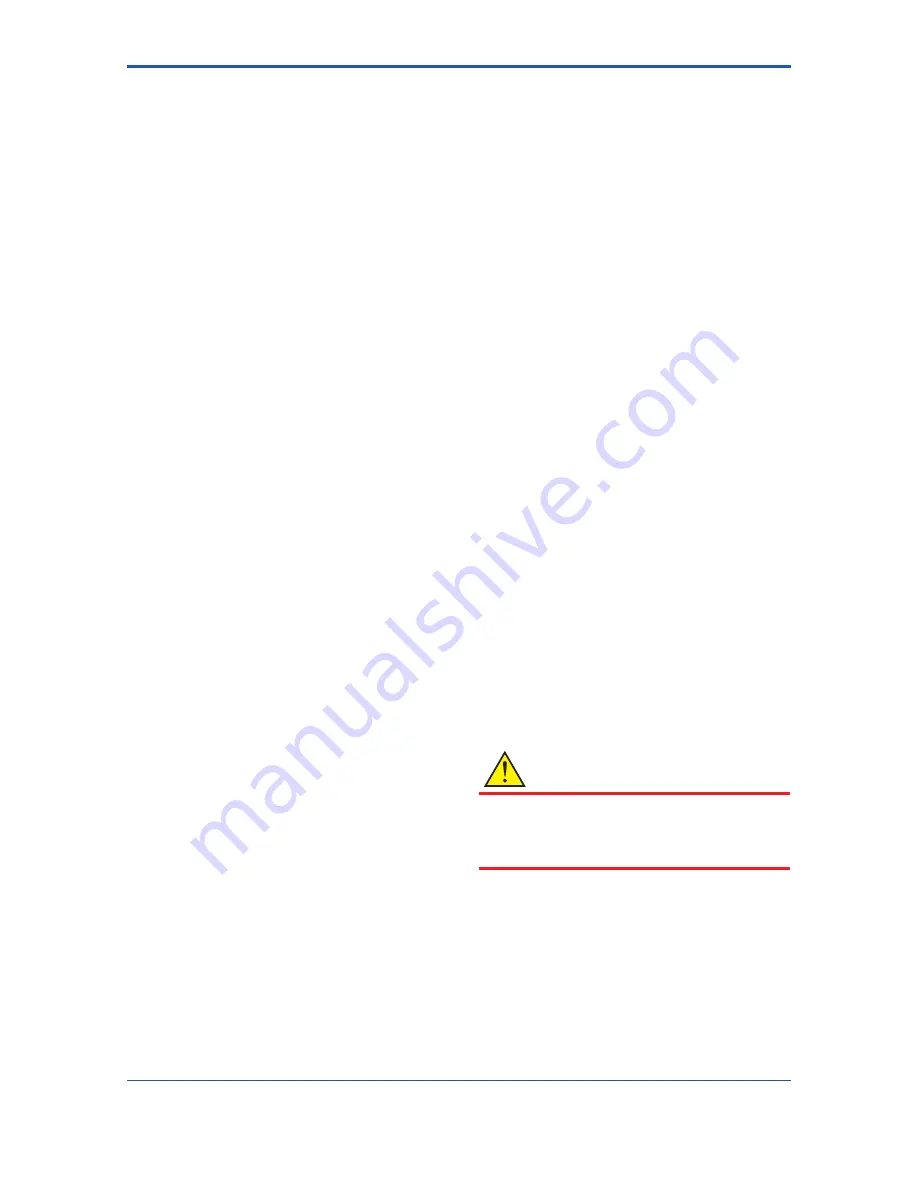
<Installation and Operating Precautions for TIIS Intrinsically Safe Equipment>
33
EX-A03E
(1) A safety barrier which meets the combination requirements
by referring to its safety rating and combination parameters
shall be selected.
(2) For pressure transmitters, pH transmitters, temperature
detectors and the like, safety barriers that can be combined
are already speci
fi
ed. Other safety barriers cannot be used.
Note 2: Testing Intrinsically Safe System
An assembly (as a system) in which intrinsically safe apparatus
and safety barriers are combined is assessed to ensure that its
safety requirements are satis
fi
ed. A tested and certi
fi
ed system
incorporates a certi
fi
cation number (intrinsically safe apparatus
and safety barriers have the same certi
fi
cation number).
Note 3: Impossible Combinations of Apparatus Certi
fi
ed Under Different
Standards
Intrinsically safe apparatus certi
fi
ed under technical criteria and
safety barriers certi
fi
ed under the “Recommended Practice for
Explosion-Protected Electrical Installations in General Industries”
(1979) and vice versa cannot be combined even if their
combination requirements are satis
fi
ed.
5. Installation of Intrinsically Safe Apparatus and
Safety Barriers
(1) Classifi cation of installation location
Intrinsically safe apparatus may be installed, depending upon
applicable gases, in a hazardous area in Zone 0, 1 or 2 (Note 4
below), where the speci
fi
ed gases are present. However, note
that apparatus certi
fi
ed under Technical Criteria, in category “ib”
shall be installed only in Zone 1 or 2. Safety barriers (associated
apparatus) that are combined with these intrinsically safe
apparatus shall be installed only in a non-hazardous area. In
cases where safety barriers are installed in a hazardous area,
they shall be enclosed, for example, in a
fl
ameproof enclosure.
Note 4: Hazardous areas are classi
fi
ed in zones based upon the
frequency of the appearance and the duration of an explosive gas
atmosphere as follows:
Zone 0: An area in which an explosive gas atmosphere is
present continuously or is present for long periods.
Zone 1: An area in which an explosive gas atmosphere is likely
to occur in normal operation.
Zone 2: An area in which an explosive gas atmosphere is not
likely to occur in normal operation and if it does occur it
will exist for a short period only.
(2) Ambient temperature limits for intrinsically safe
apparatus
Intrinsically safe apparatus shall be installed in a location where
the ambient temperature ranges from –20° to +40°C (for those
certi
fi
ed under Technical Criteria) or –10° to +40°C (for those
certi
fi
ed under the “Recommended Practice for Explosion-
Protected Electrical Installations in General Industries” (1979).
However, some
fi
eld-mounted intrinsically safe apparatus
may be used at an ambient temperature up to 60°C. So,
speci
fi
cations should be checked before installing intrinsically
safe apparatus.
If the intrinsically safe apparatus are exposed to direct sunshine
or radiant heat from plant facilities, appropriate thermal
protection measures shall be taken.
6. Wiring for Intrinsically Safe Circuits
In intrinsically safe construction, safety shall be maintained as
an intrinsically safe system involving intrinsically safe apparatus
and safety barriers connected thereto, and electrical wiring
(through intrinsically safe circuits) interconnected between them.
In other words, even when safety requirements are maintained
individually by intrinsically safe apparatus and safety barriers,
they shall not be affected by electrical or magnetic energy
caused by electrical wiring.
To make electrical wiring for intrinsically safe circuits, you must:
(a) refer to the equipment con
fi
guration diagram and make
electrical wiring properly;
(b) prevent intrinsically safe wiring from being contacted with
non-intrinsically safe wiring, and separate the intrinsically
safe circuit from other electrical circuits;
(c) prevent intrinsically safe wiring from being electrostatically
and magnetically affected by non-intrinsically safe wiring;
(d) reduce wiring inductance and capacitance produced
between the intrinsically safe apparatus and safety barrier
where possible, and use a shorter cable between the
intrinsically safe apparatus and safety barrier than speci
fi
ed
if the maximum permissible inductance of the cable is
speci
fi
ed as operating conditions;
(e) conform to conditions of installation such as wiring method,
earthing or the like, if any; and
(f) protect the outer sheath of cables from damage with
appropriate measures.
7. Maintenance and Inspection of Intrinsically Safe
Apparatus and Safety Barriers
Maintenance and inspection of intrinsically safe apparatus and
safety barriers shall be limited to within the instructions described
in applicable instruction manuals. If other than this is required,
contact the manufacturers. For more information, refer to the
“USER’S GUIDELINES for Electrical Installations for Explosive
Gas Atmospheres in General Industry” issued in 1994 by the
Japanese Ministry of Labour, the Research Institute of Industrial
Safety.
(1) Requirements for maintenance personnel
Maintenance and inspection of intrinsically safe apparatus and
safety barriers shall be conducted by maintenance personnel
skilled in intrinsically safe construction and installation of
electrical devices as well as capable of applying associated
rules.
(2) Maintenance and Inspection
(a) Visual inspection
Visually inspect the external connections of intrinsically safe
apparatus and safety barriers, and cables for damage or
corrosion as well as other mechanical and structural defects.
(b) Adjustments
Zero, span and sensitivity adjustments shall be made
with applicable adjusting potentiometers and mechanical
adjustment screws.
These maintenance adjustments shall be made in a non-
hazardous location.
CAUTION
If intrinsically safe apparatus and safety barriers require
maintenance service and checking, a gas detector shall be
used to ensure that there is no explosive gas in the location
(maintenance servicing shall be conducted in a non-
hazardous location).
(3) Repair
Intrinsically safe apparatus and safety barriers shall be repaired
by manufacturers.
(4) Prohibition of modifi cations and specifi cation
changes
Do not attempt to make modi
fi
cations or change speci
fi
cations
which may affect safety.
Содержание Dpharp vigilantplant EJA110A
Страница 2: ......