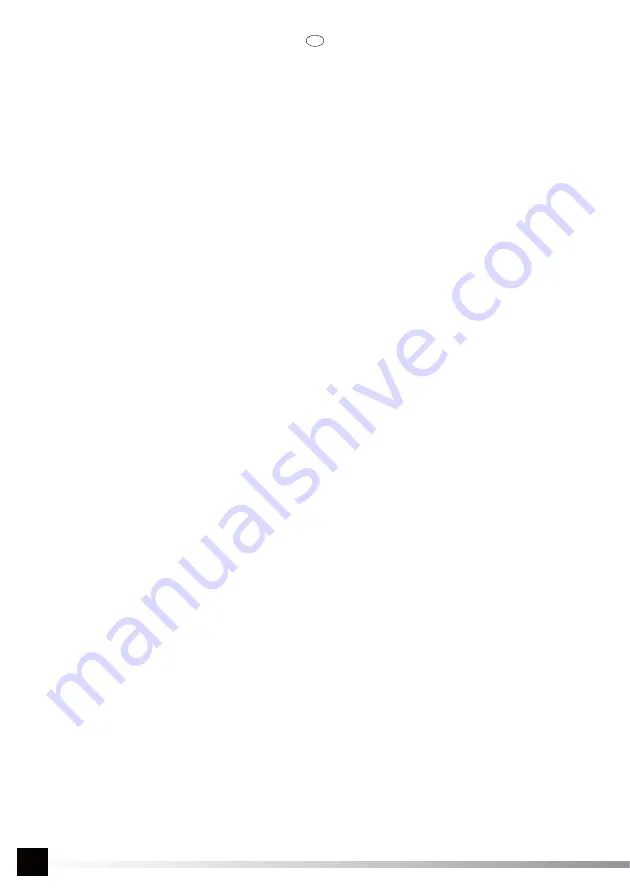
10
GB
O R I G I N A L I N S T R U C T I O N S
they should be immediately replaced with new, faultless elements of the system.
Before each use of the pneumatic system, dry the humidity that condensates inside the tool, the compressor and the dusts.
Connection of the tool to the pneumatic system
The drawing shows the recommended manner of connection of the tool to the pneumatic system. The presented connection
guarantees the most effective operation of the tool and will prolong its durability.
Place a couple of drops of oil (of viscosity SAE 10) to the air inlet.
Into the thread of the air inlet, turn strongly an appropriate terminal that makes it possible to connect an air supply hose. (II)
Install an appropriate terminal on the collector of the tool.
During work with pneumatic tools, use solely the equipment ap-
proved for work with percussive tools.
Adjust a correct direction of rotation. „F” indicates clockwise rotation, „R” – anticlockwise rotation.
Where it is possible, adjust the pressure (turning moment).
Connect the tool to the pneumatic system using a hose of internal diameter 1/2”. Make sure the resistance of the hose is at least
1.38MPa. (III)
Work with thimble percussive wrenches
Before screwing with a wrench starts, place the screw or the nut on the thread manually (at least two turns).
Make sure the size of the wrench is correct for the screwed element. A wrong size may be a cause of damage to the wrench, the
screw or the nut.
Unscrewing and tightening
Adjust the pressure in the pneumatic system so as it does not exceed the maximum value for the given tool.
Set up the appropriate direction of rotation for the tool (F – tightening, R – unscrewing), and the appropriate turning moment. (V)
Install an appropriate thimble wrench on the collector of the tool. (IV)
Connect the key to the pneumatic system.
Place the key with the thimble installed on the element to be unscrewed or tightened.
Gradually release the trigger of the tool.
Once the work has been concluded, dismantle the pneumatic system and perform appropriate maintenance of the tool.
MAINTENANCE
Never use gasoline, solvents or another in
fl
ammable liquid to clean the tool. The fumes may ignite causing an explosion of the
tool and serious injuries.
Solvents used to clean the tool holder and the body of the tool may soften the tightening of the machine. Dry thoroughly the tool
before you start working with it.
If any irregularities in the functioning of the tool are detected, it must be immediately disconnected from the pneumatic system.
All elements of the pneumatic system must be protected from dirt.
Dirt in the pneumatic system may damage the tool and other elements of the pneumatic system.
Maintenance of the tool before every use
Disconnect the tool from the pneumatic system.
Before each use of the tool, place a small amount of maintenance liquid (e.g. WD-40) through the air inlet.
Connect the tool to the pneumatic system and start it for approximately 30 seconds. It will allow spreading the maintenance liquid
inside the tool and cleaning it.
Disconnect the tool from the pneumatic system again.
Place a small amount of SAE 10 oil inside the tool through the air inlet and other appropriate holes. It is recommended to use SAE
10 oil whose purpose is maintenance of pneumatic tools. Connect the tool and start it for a while.
Attention! WD-40 cannot be used as appropriate lubricating oil.
Wipe out the excess of oil that comes out through the outlets. If the oil is left, it may damage the tightening of the tool.
Other maintenance actions
Before each use of the tool, make sure there are no signs of damage on the tool. Collectors, tool holders and spindles must be
kept clean.
Every six months, or every 100 hours of operation, send the tool for revision which must be realized by quali
fi
ed personnel in the
repair shop. If the tool was used without the recommended air supply system, increase the frequency of overhauls of the tool.
Defects
Stop operation of the tool immediately if any defect in its functioning has been detected. Work with a damaged tool may be a
cause of injuries. All repair and replacement of the elements of the tool must be performed by quali
fi
ed personnel in an authorized
repair shop.
Содержание YT-0960
Страница 17: ...17 RUS...
Страница 18: ...18 RUS SAE 10 II F R 1 2 1 38MPa III F R V IV...
Страница 19: ...19 RUS WD 40 30 SAE 10 SAE 10 WD 40 6 100 WD 40 30 1 2 0 3 MPa...
Страница 21: ...21 UA K...
Страница 22: ...22 UA SAE 10 II F R 1 2 1 38MPa III F R V IV...
Страница 23: ...23 UA WD 40 30 SAE 10 SAE 10 WD 40 6 100 WD 40 30 1 2 0 3 MPa...
Страница 52: ...I N S T R U K C J A O R Y G I N A L N A 52...