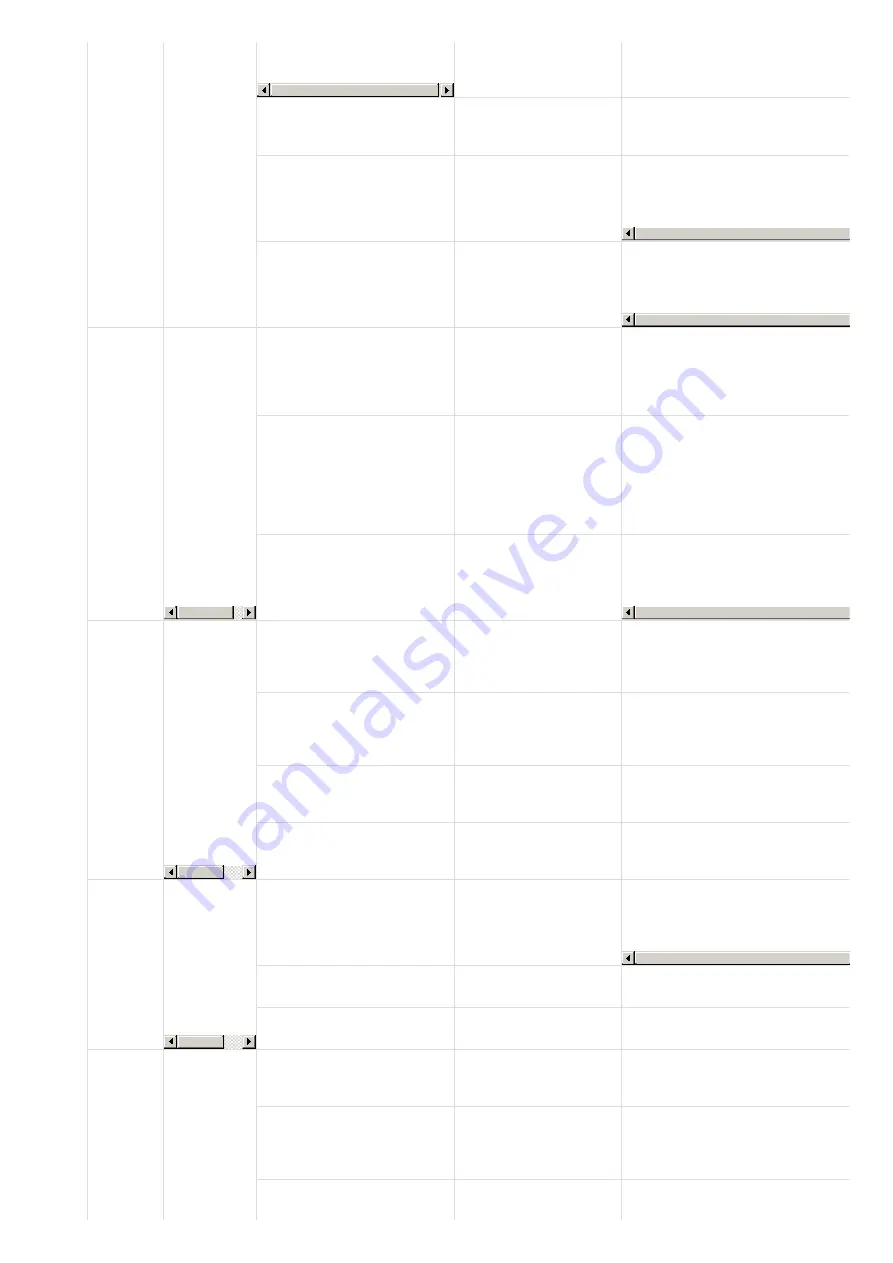
A.Cb0
Encoder
Echoback
Error
because of influence from
machines on the servomotor
side, such as the welder.
Check the encoder
cable layout.
Properly ground the machines to
separate from encoder FG.
Excessive vibration and
shocks were applied to the
encoder.
Check the operating
environment.
Reduce the machine vibration or
correctly install the servomotor.
An encoder fault occurred.
--
Turn the power supply OFF and then
ON again. If the alarm still occurs,
the servomotor may be faulty.
Replace the servomotor.
A SERVOPACK fault
occurred.
--
Turn the power supply OFF and then
ON again. If the alarm still occurs,
the SERVOPACK may be faulty.
Replace the SERVOPACK.
A.CC0
Multiturn
Limit
Disagreement
When using a direct drive
(DD) servo motor, the
multiturn limit value
(Pn205) is different from
that of the encoder.
Check the value of the
Pn205.
Correct the setting of Pn205 (0 to
65535).
The multiturn limit value of
the encoder is different
from that of the
SERVOPACK. Or, the
multiturn limit value of the
SERVOPACK has been
changed.
Check the value of the
Pn205 of the
SERVOPACK.
Execute Fn013 at the occurrence of
alarm.
A SERVOPACK fault
occurred.
--
Turn the power supply OFF and then
ON again. If the alarm still occurs,
the SERVOPACK may be faulty.
Replace the SERVOPACK.
A.CF1
Feedback
Option
Module
Communications
Error
(Reception
error)
Wiring of cable between
serial converter unit and
SERVOPACK is incorrect or
contact is faulty.
Check the external
encoder wiring.
Correct the cable wiring.
The specified cable is not
used between serial
converter unit and
SERVOPACK.
Confirm the external
encoder wiring
specifications.
Use the specified cable.
Cable between serial
converter unit and
SERVOPACK is too long.
Measure the length of
this cable.
Use 20-m cable max.
Sheath of cable between
serial converter unit and
SERVOPACK is broken.
Check the cable for
damage.
Replace the cable.
A.CF2
Feedback
Option
Module
Communications
Error
(Timer stop)
Noise interferes with the
cable between serial
converter unit and
SERVOPACK.
--
Correct the wiring around serial
converter unit, e.g., separating I/O
signal line from main circuit cable or
grounding.
A serial converter unit fault
occurred.
--
Replace the serial converter unit.
A SERVOPACK fault
occurred.
--
Replace the SERVOPACK.
Position
Error
Overflow
(Position
error
exceeded
The servomotor U, V, and W
wirings is faulty.
Check the servomotor
main circuit cable
connection.
Confirm that there is no contact
fault in the motor wiring or encoder
wiring.
The frequency of the
position reference pulse is
too high.
Reduce the reference
pulse frequency, and
operate the
SERVOPACK.
Reduce the position reference pulse
frequency or acceleration of
position reference. Or, reconsider
the electronic gear ratio.
The position reference
acceleration is too fast.
Reduce the reference
acceleration, and
operate the
Apply the smoothing function, such
as using position reference
acceleration/deceleration time
Содержание SGDV-R70F
Страница 23: ...5 Read Position actual internal value 6 Set the negative of that value to home offset 7 Cycle power to drive...
Страница 25: ...Factor and Offset Analog Monitor 1 Pn006 XX02 Load Meter...
Страница 31: ...Install Standoff Install Buffer Board...
Страница 32: ...Reinstall mounting screw Install jumper on servo adaptor J5 pin 2 3 next to the labeled SEN...
Страница 33: ...Install wire from Buffer Board to all Yaskawa servo adaptors for SEN signal...
Страница 34: ...Install Motor Encoder Cable with Battery...