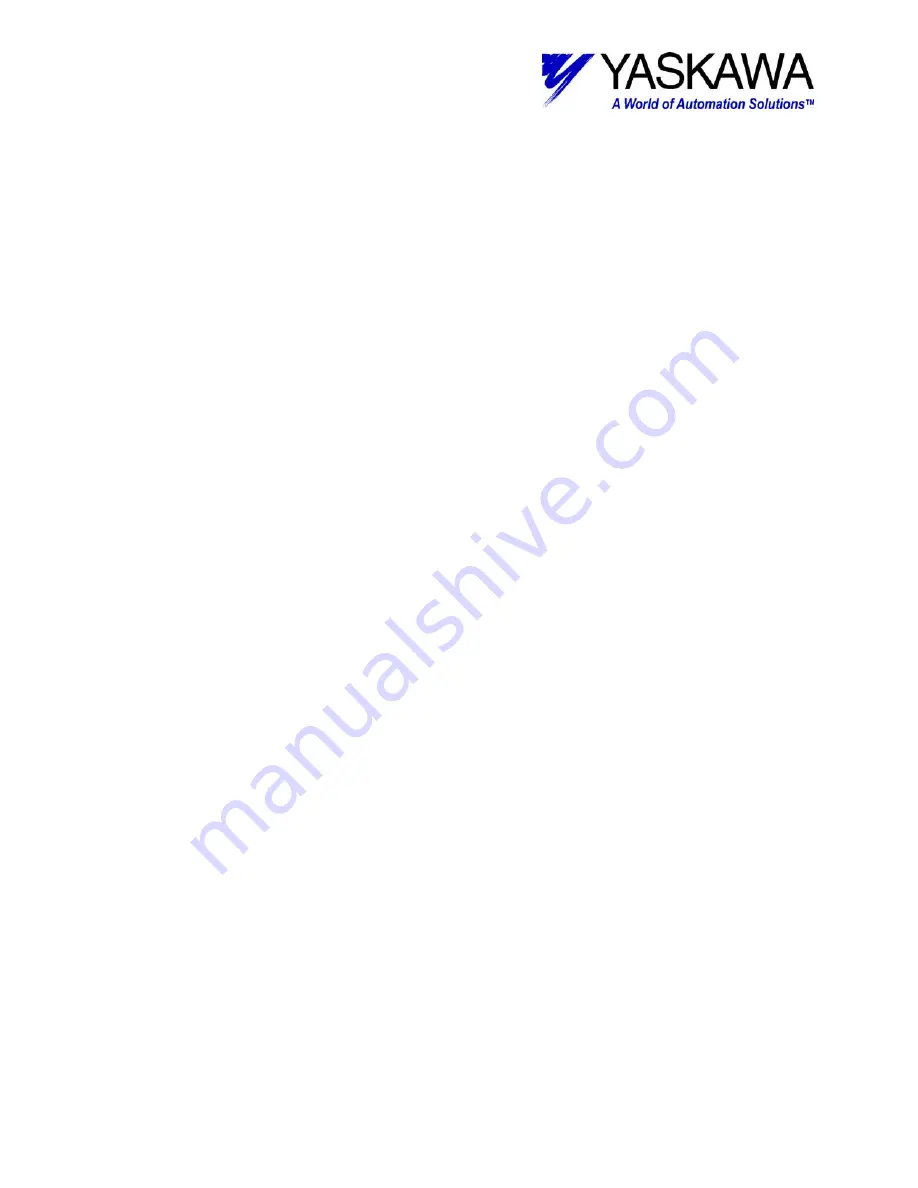
TECHNICAL NOTE
MOTION APPLICATION ENGINEERING GROUP
Yaskawa Electric America - 2121 Norman Drive South – Waukegan IL 60085
(800) YASKAWA - Fax (847) 887-7280
11/23/2005
21 of 21
eng/05.055/MCD
Low Speed Scan Drawings (L)
L
Low Scan Parent, calls child drawings
L01
HMI interface – put communication code here if necessary
L01.01
HMI to MP Controller Conversions
L01.02
MP Controller to HMI Conversions
L10
Machine common ladder sequencing (machine control
states)
L10.01
Machine Common Ladder sequence (Control Mode [Auto vs
Manual], All Axes Normal, All Stopped, All Axes Enabled,
Home, etc)
L10.02
Sequence A Motion Logic
L10.03
Sequence B Motion Logic
L20
Individual axis sequencing for MCC or FB methods (servo
axis, drive roll)
L20.01
Axis 1 individual sequencing (Axis Normal, Servo On, Jog+,
Jog-, Low Speed motion control, etc.)
L20.02
Axis 2 individual sequencing (Axis Normal, Servo On, Jog+,
Jog-, Low Speed motion control, etc.)
L25
Motion Program sequencing and interlocking for MPL
method (combined groups of axes)
L25.01
Group #1 motion sequencing and interlock (Low speed
Ladder sequence to control the group or Motion Program)
L25.02
Group #2 motion sequencing and interlock (Low speed
Ladder sequence to control the group or Motion Program)
L30
Low speed auxiliary machine devices (on/off devices, fan,
pump, air cylinder)
L30.01
Aux. device 1 (pump#1)
L30.02
Aux. device 2 (fan #1)
L40
Machine
Constants
L40.01
Axis 1 Constants
L40.02
Axis 2 Constants
Now the systems functional specifications are documented, motion-programming methods are
selected in addition to the program architecture. With the control application outlined, it is now
viable to accurately allocate memory for coding the application as discussed in the next section.