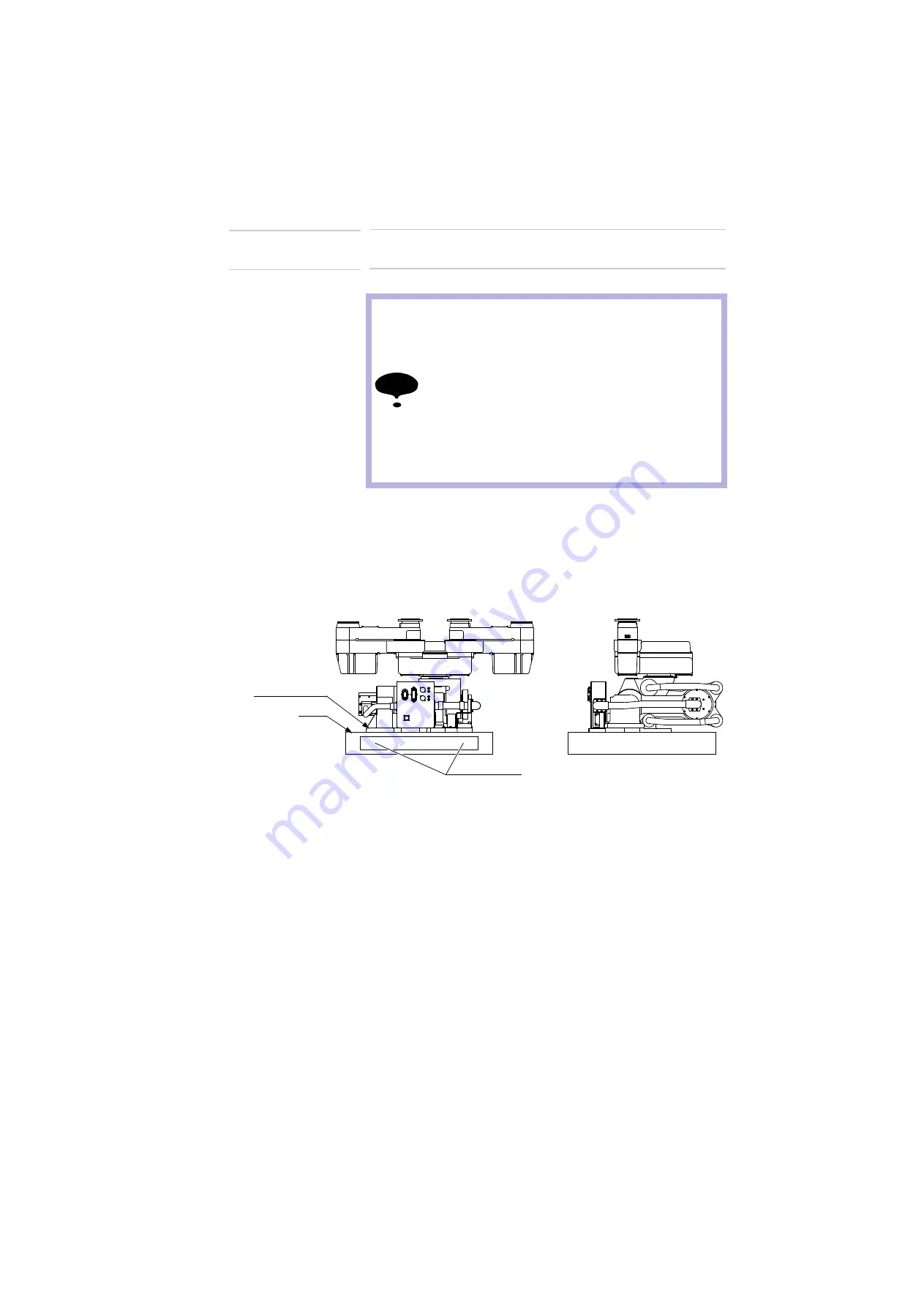
2-3
179394-1CD
HW1483905
2
Transporting
2.1 Transporting Method
MFL15D-875/-1600
2.1.2 Using a Forklift
When using a forklift, the manipulator should be fixed on a pallet with
shipping bolts and brackets as shown in
. Insert
forks under the pallet and lift the manipulator with the pallet. The pallet
must be strong enough to support the manipulator.
Transport the manipulator slowly in order to avoid overturning or slippage.
Fig. 2-2: Using a Forklift
NOTE
•
Check that the eyebolts are securely fastened.
•
The mass of the manipulator is approximately 420 kg
(MFL15D-875) and 610 kg (MFL15D-1600) with
shipping bolts and brackets included. Use a wire rope
strong enough to withstand the mass.
•
Attached eyebolts are designed to support the
manipulator mass. Do not use them for anything other
than transporting the manipulator.
•
Avoid external force on the arm or motor unit in
transporting the manipulator. Use caution when using
transporting equipment other than a crane or a forklift, to
avoid injury.
B
Forklift fork entry
Bolt M16 (4 bolts)
Pallet
19 of 74