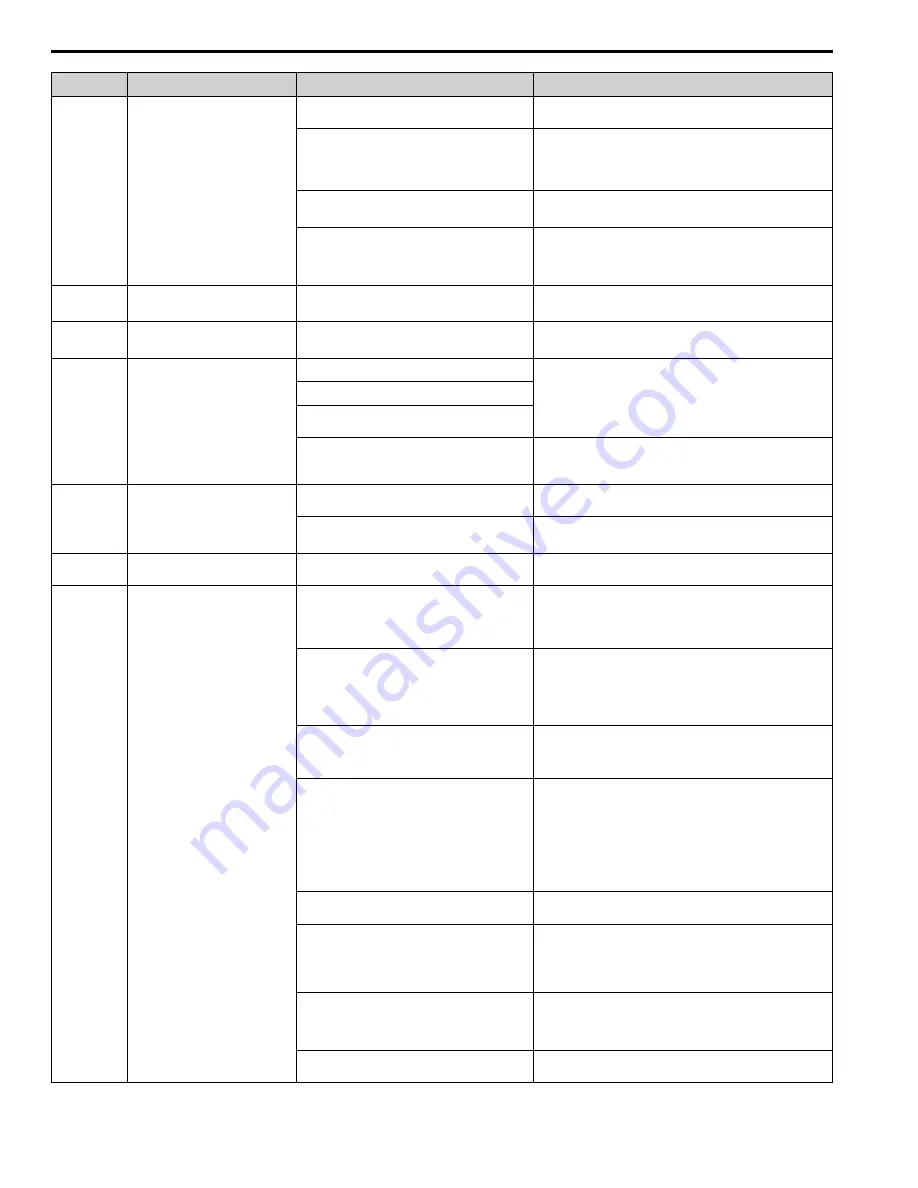
104
YASKAWA
TOEPC71061732E HV600 Drive Installation & Primary Operation
Code
Name
Causes
Possible Solutions
The torque compensation gain is too large.
Decrease the value set in
C4-01 [Torque Compensation Gain]
to
make sure that the motor does not stall.
The speed search-related parameters are set
incorrectly.
•
Examine the settings for all speed search-related parameters.
•
Adjust
b3-03 [Speed Search Deceleration Time]
.
•
Set
b3-24 = 1 [Speed Search Method Selection = Speed
Estimation]
after Auto-Tuning.
Phase loss in the input power supply is causing the
output current to change.
•
Correct errors with the wiring for main circuit drive input power.
•
Make sure that there is no phase loss, and repair problems.
Overload occurred during overexcitation deceleration.
•
Decrease the value set in
n3-13 [OverexcitationBraking (OEB)
Gain]
.
•
Decrease the value set in
n3-21 [HSB Current Suppression
Level]
.
oL3
Overtorque Detection 1
A fault occurred on the machine.
Example: The machine is locked.
Examine the machine and remove the cause of the fault.
oL4
Overtorque Detection 2
A fault occurred on the machine.
Example: The machine is locked.
Examine the machine and remove the cause of the fault.
oL7
High Slip Braking Overload
The load inertia is too large.
An external force on the load side rotated the motor.
Something is preventing deceleration on the load
side.
Decrease deceleration times in
C1-02 and C1-04 [Deceleration
Times]
for applications that do not use High Slip Braking.
The value set in
n3-04 [HSB Overload Time]
is too
small.
•
Increase the value set in
n3-04
.
•
Connect a thermal overload relay to the motor, and set
n3-04 =
1200 s (maximum value)
.
oPr
Keypad Connection Fault
The keypad is not securely connected to the
connector on the drive.
Examine the connection between the keypad and the drive.
The connection cable between the drive and the
keypad is disconnected.
•
Remove the keypad and connect it again.
•
If the cable is damaged, replace it.
oS
Overspeed
There is overshoot.
Decrease
C5-01 [ASR Proportional Gain 1]
and increase
C5-02
[ASR Integral Time 1]
.
ov
Overvoltage
Deceleration time is too short and regenerative energy
is flowing from the motor into the drive.
•
Set
L3-04 = 1 [Stall Prevention during Decel = General
Purpose]
.
•
Increase the values set in
C1-02 or C1-04 [Deceleration Times]
.
•
Perform Deceleration Rate Auto-Tuning.
The acceleration time is too short.
•
Make sure that sudden drive acceleration does not cause the
fault.
•
Increase the values set in
C1-01 or C1-03 [Acceleration Times]
.
•
Increase the value set in
C2-02 [S-Curve Time @ End of Accel]
.
•
Set
L3-11 = 1 [Overvoltage Suppression Select = Enabled]
.
The drive output cable or motor is shorted to ground
(the current short to ground is charging the main
circuit capacitor of the drive through the power
supply).
1.
Examine the motor main circuit cable, terminals, and motor
terminal box, and then remove ground faults.
2.
Re-energize the drive.
If the drive detects
ov
in these conditions, the speed
search-related parameters are incorrect:
•
During speed search
•
During momentary power loss recovery
•
When the drive starts again automatically
•
When you set
A1-02 = 0 [Control Method
Selection = V/f Control]
and do rotational Auto-
Tuning
•
Examine the settings for all speed search related parameters.
•
Set
b3-19 ≠ 0 [Speed Search Restart Attempts ≠ 0 times]
.
•
Adjust
b3-03 [Speed Search Deceleration Time]
setting.
•
Do Stationary Auto-Tuning for Line-to-Line Resistance and then
set
b3-24 = 1 [Speed Search Method Selection = Speed
Estimation]
.
•
Increase the value set in
L2-04 [Powerloss V/f Recovery Ramp
Time]
.
The power supply voltage is too high.
Decrease the power supply voltage to align with the drive rated
voltage.
Electrical interference caused a drive malfunction.
•
Examine the control circuit lines, main circuit lines, and ground
wiring, and decrease the effects of electrical interference.
•
Make sure that a magnetic contactor is not the source of the
electrical interference, then use a Surge Protective Device if
necessary.
The load inertia is set incorrectly.
•
Examine the load inertia settings with KEB, overvoltage
suppression, or stall prevention during deceleration.
•
Adjust
L3-25 [Load Inertia Ratio]
to align with the qualities of
the machine.
The Short Circuit Braking function was used in OLV/
PM control method.
Connect a braking resistor to the drive.